Çapaklar, metal işleme sürecinde kaçınılmaz bir sorundur. Delme, tornalama, frezeleme veya plaka kesme olsun, çapak oluşumu ürünün kalitesini ve güvenliğini etkileyecektir. Çapaklar sadece kolayca kesilmekle kalmaz, aynı zamanda sonraki işleme ve montajı da etkileyerek üretim maliyetlerini artırır. Bitmiş ürünün doğruluğunu ve yüzey kalitesini sağlamak için çapak alma, özellikle hassas parçalar için vazgeçilmez bir ikincil işleme süreci haline gelmiştir. Çapak alma ve kenar bitirme, bitmiş ürünün maliyetinin %30'undan fazlasını oluşturabilir. Ancak, çapak alma sürecini otomatikleştirmek genellikle zordur ve bu da üretim verimliliği ve maliyet kontrolünde zorluklara neden olur.
Yaygın çapak alma yöntemleri
Kimyasal çapak alma
Kimyasal çapak alma, çapakları kimyasal reaksiyonla gidermektir. Parçaları belirli bir kimyasal çözeltiye maruz bırakarak, kimyasal iyonlar parçaların yüzeyine yapışarak korozyonu önleyen koruyucu bir film oluşturur ve çapaklar yüzeyden dışarı taştığı için kimyasal reaksiyonla giderilir. Bu yöntem, özellikle hassas parçaların çapaklarını gidermek için pnömatik, hidrolik ve mühendislik makineleri alanlarında yaygın olarak kullanılır.
Yüksek sıcaklıkta çapak alma
Yüksek sıcaklıkta çapak alma, parçaları kapalı bir bölmede hidrojen ve oksijen karışımı gazla karıştırmak, onları yüksek bir sıcaklığa ısıtmak ve çapakları yakmak için patlatmaktır. Patlamanın ürettiği yüksek sıcaklık yalnızca çapaklara etki ettiğinden ve parçalara zarar vermediğinden, bu yöntem özellikle karmaşık şekillere sahip parçalar için uygundur.
Davul çapak alma
Tambur çapak alma, aşındırıcılar ve parçaları birlikte kullanarak çapakları giderme yöntemidir. Parçalar ve aşındırıcılar kapalı bir tambura yerleştirilir. Tamburun dönüşü sırasında aşındırıcılar ve parçalar birbirine sürtünerek çapakları gidermek için taşlama kuvveti oluşturur. Yaygın olarak kullanılan aşındırıcılar arasında kuvars kumu, odun yongaları, alüminyum oksit, seramik ve metal halkalar bulunur. Bu yöntem büyük ölçekli üretim için uygundur ve yüksek işleme verimliliğine sahiptir.
Manuel çapak alma
Manuel çapak alma en geleneksel, zaman alıcı ve emek yoğun yöntemdir. Operatörler çapakları manuel olarak taşlamak için çelik törpüler, zımpara kağıdı ve taşlama başlıkları gibi aletler kullanır. Bu yöntem küçük partiler veya karmaşık şekillere sahip parçalar için uygundur, ancak düşük üretim verimliliğine ve yüksek işçilik maliyetlerine sahiptir, bu nedenle kademeli olarak diğer daha verimli yöntemlerle değiştirilmektedir.
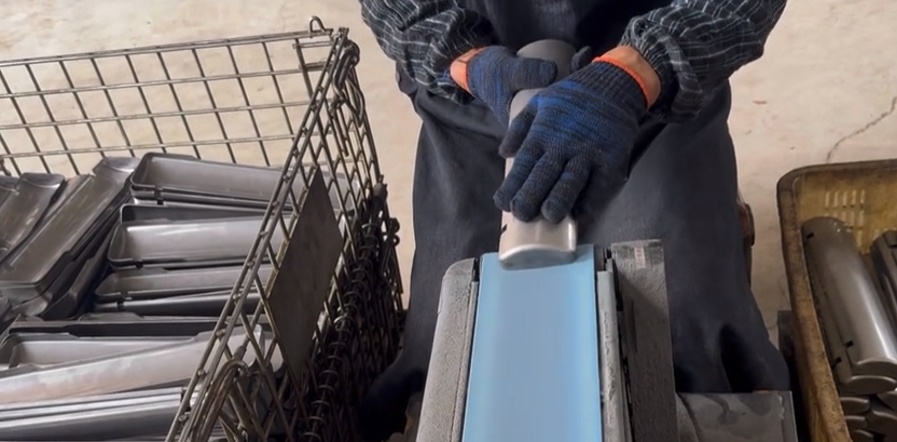
İşlem çapaksızlaştırma
İşlem çapak alma, metal parçaların kenarlarını yuvarlayarak keskin köşeleri giderir. Kenar yuvarlama sadece keskinliği veya çapakları gidermekle kalmaz, aynı zamanda parçaların yüzey kaplamasını iyileştirir ve korozyon dirençlerini artırır. Yuvarlak kenarlar genellikle lazerle kesilmiş, damgalanmış veya işlenmiş parçalar için uygun olan döner törpüleme ile gerçekleştirilir.
Döner törpüleme: Verimli çapaksızlaştırma için bir çözüm
Döner törpüleme, özellikle lazer kesim, damgalama veya işleme sonrası parçaların kenar işlemeleri için çok etkili bir çapak alma aracıdır. Döner törpüleme, sadece çapakları gidermekle kalmaz, aynı zamanda keskin kenarların neden olabileceği güvenlik sorunlarını azaltarak hızla taşlamak için dönerek kenarları pürüzsüz ve yuvarlak hale getirir. Özellikle karmaşık şekillere veya büyük miktarlara sahip parçaları işlemek için uygundur ve üretim verimliliğini ve ürün kalitesini iyileştirmeye yardımcı olur.
İşlem çapaksızlaştırma
İşlem çapak alma, metal parçaların kenarlarını yuvarlayarak keskin köşeleri giderir. Kenar yuvarlama sadece keskinliği veya çapakları gidermekle kalmaz, aynı zamanda parçaların yüzey kaplamasını iyileştirir ve korozyon dirençlerini artırır. Yuvarlak kenarlar genellikle lazerle kesilmiş, damgalanmış veya işlenmiş parçalar için uygun olan döner törpüleme ile gerçekleştirilir.
Döner törpüleme: Verimli çapaksızlaştırma için bir çözüm
Döner törpüleme, özellikle lazer kesim, damgalama veya işleme sonrası parçaların kenar işlemeleri için çok etkili bir çapak alma aracıdır. Döner törpüleme, sadece çapakları gidermekle kalmaz, aynı zamanda keskin kenarların neden olabileceği güvenlik sorunlarını azaltarak hızla taşlamak için dönerek kenarları pürüzsüz ve yuvarlak hale getirir. Özellikle karmaşık şekillere veya büyük miktarlara sahip parçaları işlemek için uygundur ve üretim verimliliğini ve ürün kalitesini iyileştirmeye yardımcı olur.
Uç Frezeleme Çapaklarının Oluşumunu Etkileyen Ana Faktörler
1. Frezeleme parametreleri, frezeleme sıcaklığı ve kesme ortamı çapak oluşumu üzerinde belirli bir etkiye sahip olacaktır. İlerleme hızı ve frezeleme derinliği gibi bazı önemli faktörlerin etkisi, düzlem kesme açısı teorisi ve takım ucu çıkış sırası EOS teorisi tarafından yansıtılır.
2. İş parçası malzemesinin plastisitesi ne kadar iyiyse, tip I çapakları oluşturmak o kadar kolaydır. Kırılgan malzemelerin uç frezeleme işleminde, besleme hızı veya düzlem kesme açısı büyükse, tip III çapaklarının (eksik) oluşumuna elverişlidir.
3. İş parçasının uç yüzeyi ile işlenmiş yüzey arasındaki açı dik açıdan büyük olduğunda, uç yüzeyin destek sertliğinin artması nedeniyle çapak oluşumu önlenebilir.
4. Frezeleme sıvısının kullanımı, takım ömrünü uzatmaya, takım aşınmasını azaltmaya, frezeleme işlemini yağlamaya ve böylece çapak boyutunu küçültmeye yardımcı olur.
5. Takım aşınması çapak oluşumunda büyük bir etkiye sahiptir. Takım belirli bir ölçüde aşındığında, takım ucunun yayı artar, sadece takım çıkış yönündeki çapak boyutu artmakla kalmaz, aynı zamanda takım kesme yönündeki çapaklar da artar.
6. Takım malzemeleri gibi diğer faktörler de çapak oluşumu üzerinde belirli bir etkiye sahiptir. Aynı kesme koşulları altında, elmas takımlar diğer takımlara göre çapak oluşumunu bastırmaya daha elverişlidir.
Aslında, çapaklar işleme sürecinde kaçınılmazdır, bu nedenle aşırı manuel müdahaleden kaçınmak için çapak sorununu bir işlem perspektifinden çözmek en iyisidir. Bir pah kırma uç frezesi kullanmak kırmızı
Yayınlanma zamanı: 14-Kas-2024