В области обработки листового металла обработка поверхности не только влияет на внешний вид продукта, но также напрямую связан с его долговечностью, функциональностью и конкурентоспособностью рынка. Применяется ли это к промышленному оборудованию, автомобильному производству или электронным приборам, высококачественные процессы обработки поверхности могут значительно улучшить качество продукции и дополнительную стоимость. Следующие 10 ключевых советов предназначены для того, чтобы помочь вам оптимизировать процесс обработки поверхности листового металла и помочь более эффективно достичь превосходных результатов.
Совет 1: Точная предварительная обработка
Перед началом какого -либо процесса обработки поверхности тщательная предварительная обработка поверхности является основой для обеспечения эффекта последующей обработки.
Удаление поверхностного масла, оксидов и ржавчины является первой задачей. Вы можете использовать профессиональные обезжирители или съемки ржавчины в сочетании с замачиванием, распылением или ручным стиранием.
Для упорного загрязнения можно использовать механическое шлифование (например, наждачная бумага, шлифовальное колесо и т. Д.).
Обратите внимание при работе:Управляйте силой, чтобы избежать повреждения поверхности субстрата, особенно для более тонких деталей листового металла.
Предложения по улучшению: используйте автоматизированное оборудование предварительной обработки (например, Spray Systems) для обеспечения эффективности и согласованности обработки, особенно в массовом производстве.
Совет 2: Выберите правильный материал покрытия
Различные сценарии использования имеют разные требования к материалам покрытия листового металла:
Среда на открытом воздухе: рекомендуется использовать покрытие с высокой погодой, например, фторуглеродное покрытие или акриловое покрытие.
Высокие детали для трения: полиуретановое покрытие или керамическое покрытие предпочтительнее, чтобы повысить устойчивость к износу.
В то же время, внимание также должно быть уделено адгезии покрытия, которое может быть улучшено с помощью праймера. Для специальных сценариев спроса (таких как антибактериальные или изолирующие поверхности) можно рассмотреть функциональные покрытия.
Советы:Экологическое дружелюбие и низкое содержание ЛОС (летучие органические соединения) материалов для покрытия становятся рыночной тенденцией, а зеленые и экологически чистые покрытия могут быть предпочтительны.
Совет 3: Оптимизировать параметры процесса распыления
Параметры процесса распыления непосредственно определяют качество и внешний вид покрытия:
Расстояние распылительного пистолета: его следует хранить между 15-25 см, чтобы избежать провисания или грубых частиц.
Давление распыления: рекомендуется составлять от 0,3 до 0,6 МПа, чтобы обеспечить равномерную атомизацию краски.
Скорость распыления и угол: для заготовки со сложными формами отрегулируйте угол распылительного пистолета, чтобы обеспечить однородное покрытие покрытия по краям и канавкам.
Предложения по улучшению:Провести эксперименты по покрытию образца на этапе проверки процесса, чтобы оптимизировать настройки параметров и обеспечить стабильность в крупномасштабном производстве.
Совет 4: Используйте технологию электростатического распыления
Электростатическое распыление стало первым выбором для современной обработки поверхности из -за его высокой скорости и однородности:
Эффект заземления является ключом к качеству опрыскивания, и для обеспечения стабильного электрического поля следует использовать профессиональное оборудование заземляющего оборудования.
Отрегулируйте электростатическое напряжение в соответствии со сложностью листового металла, обычно контролируемого между 50-80 кВ.
Для сложных заготовков со слепыми отверстиями или внутренними полостями можно использовать систему с двойным пулеметом или с помощью ручного распыления, чтобы избежать слабых областей покрытия, вызванных эффектом защиты электрического поля.
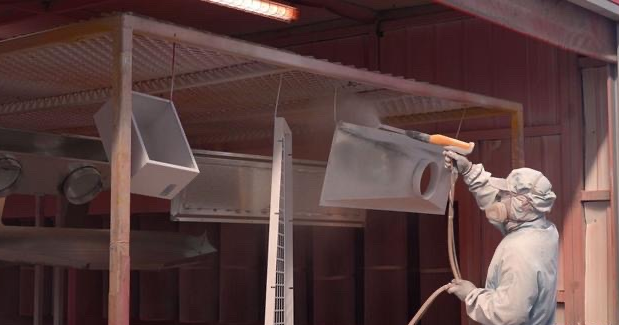
Совет 5: Фосфалирующая обработка повышает производительность против коррозии
Фосфалирующая обработка может не только улучшить коррозионную стойкость субстрата, но и усилить адгезию последующих покрытий:
Управление температурой: рекомендуемая температура фосфатирования для стали составляет от 50 до 70 ℃. Слишком высокий или слишком низкий, повлияет на однородность фосфалирующей пленки.
Настройка времени: обычно 3-10 минут, скорректируется в соответствии с требованиями материала и процесса.
Предложение об обновлении: используйте низкотемпературную технологию фосфалирования для снижения потребления энергии, и в сочетании с экологически чистым фосфалирующим раствором для снижения давления очистки промышленных сточных вод.
Совет 6: Осветите точки ядра процесса гальванизации
Обълектирование может обеспечить отличные декоративные и защитные свойства, но это требует высокого контроля процесса:
Плотность и температура тока должны быть строго сопоставлены. Например, при глизировании температура должна быть между 20-30 ℃, а плотность тока должна сохраняться при 2-4 ат-дм².
Концентрацию добавок в гальванизированном растворе следует регулярно контролировать, чтобы обеспечить плавность и плотность покрытия.
ПРИМЕЧАНИЕ. Очистка после гальванизации имеет решающее значение. Остатовой гальванический раствор может вызвать запотевание или коррозию на поверхности покрытия.
Совет 7: анодирование (эксклюзивный для алюминиевых деталей)
Анодирование является основным процессом для улучшения коррозионной стойкости и декоративного эффекта деталей алюминиевого листового металла:
Напряжение рекомендуется контролировать при 10-20 В, а время обработки корректируется в соответствии с потребностями (20-60 минут).
Окрашивание и уплотнение после окисления являются ключевыми шагами для усиления антиоксидантной способности и долговечности цвета.
Усовершенствованные технологии: используйте технологию микроармонов окисления (MAO) для дальнейшего улучшения твердости и износостойкости оксидной пленки.
Совет 8: Шлифование и полировка поверхности для повышения точности
Высококачественная обработка поверхности неотделима от шлифования и полировки:
Выбор наждачной бумаги: от грубого к мелкому, шаг за шагом, например, сначала используйте 320#, затем переходите к 800# или более высокой сетке.
Последовательная работа: направление шлифования должно быть последовательным, чтобы избежать поперечных царапин, влияющих на внешний вид.
Для заготовки с высоким содержанием блеска можно использовать зеркальную полировку в сочетании с полировочной пастой или пастой оксида хрома для улучшения эффекта.
Совет 9: Усиление проверки качества и управления процессами
Стабильность качества обработки поверхности неотделима от проверки и контроля:
Значение толщины покрытия: обнаружение толщины покрытия.
Тест на адгезию: например, перекрестный тест или перерыв, чтобы проверить, является ли покрытие твердым.
Тест на распыление солевого распыления: для оценки коррозионной устойчивости.
Предложения по улучшению: внедряя автоматизированное испытательное оборудование, обеспечить эффективность тестирования и объединить анализ данных для оптимизации процессов в реальном времени.
Совет 10: Непрерывное обучение и технологические инновации
Технология обработки поверхности меняется с каждым днем, и для поддержания технологического лидерства требуется:
Обратите внимание на тенденции отрасли: понимайте последние тенденции процесса, участвуя в выставок и семинарах.
Технологические инвестиции в исследования и разработки: внедрить интеллектуальное оборудование и новые экологически чистые материалы для повышения уровня эффективности и защиты окружающей среды.
Например, появляются новые технологии, такие как нано -покрытия и распыление плазмы, постепенно продвигаются, что обеспечивает больше возможностей для области обработки поверхности.
Пост времени: декабрь-06-2024