Precision-Engineered Turbo Wastegate Bracket for Automotive Applications
● Product type: Turbine Accessories
● Material: Stainless steel, Carbon steel, etc.
● Surface treatment: Galvanizing, Electrophoresis
● Applicable exhaust valve diameter: 38mm-60mm
● Thread specifications: M6, M8, M10
Customizable
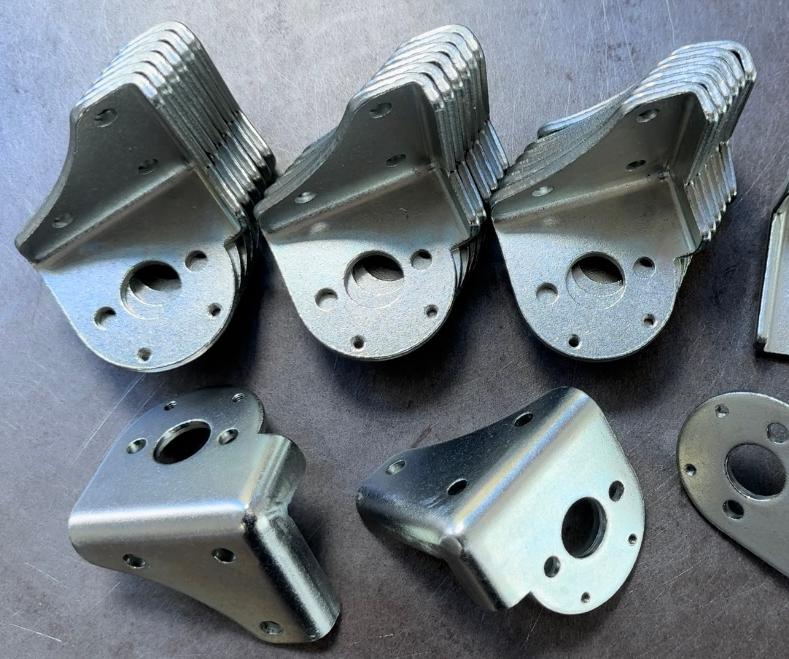
Application Scenarios:
● Racing engines: Enhance engine stability and response speed, suitable for a range of high-performance racing automobiles.
● Heavy machinery: Offers enduring endurance and support under demanding operating conditions and heavy loads, ideal for industrial turbocharger systems and heavy-duty engine parts.
● Performance automobiles and modified cars: Offer tailored turbocharger modification solutions and custom engine brackets to satisfy professional car owners' demands.
● Industrial engines: Useful for industrial turbocharger systems, ensuring sustained and effective performance in high-performance industrial engines.
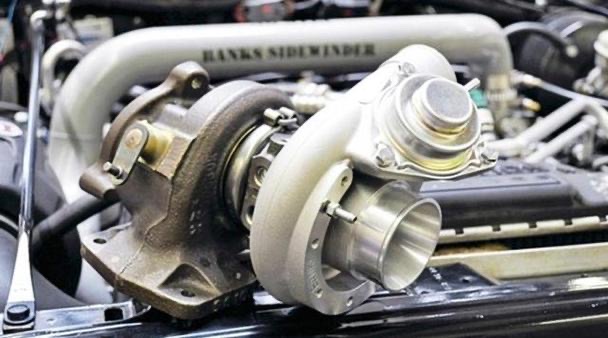
Quality Management
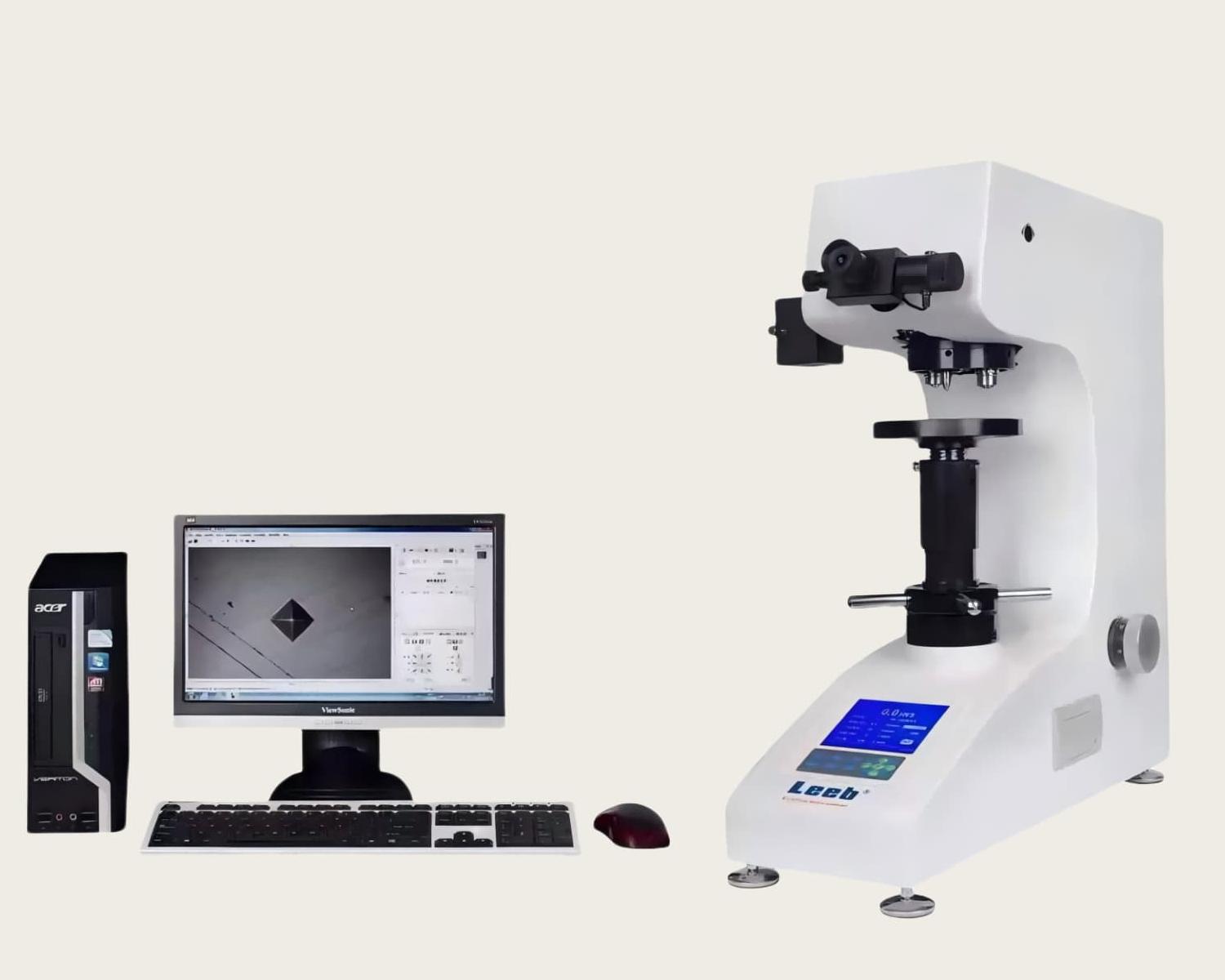
Vickers Hardness Instrument
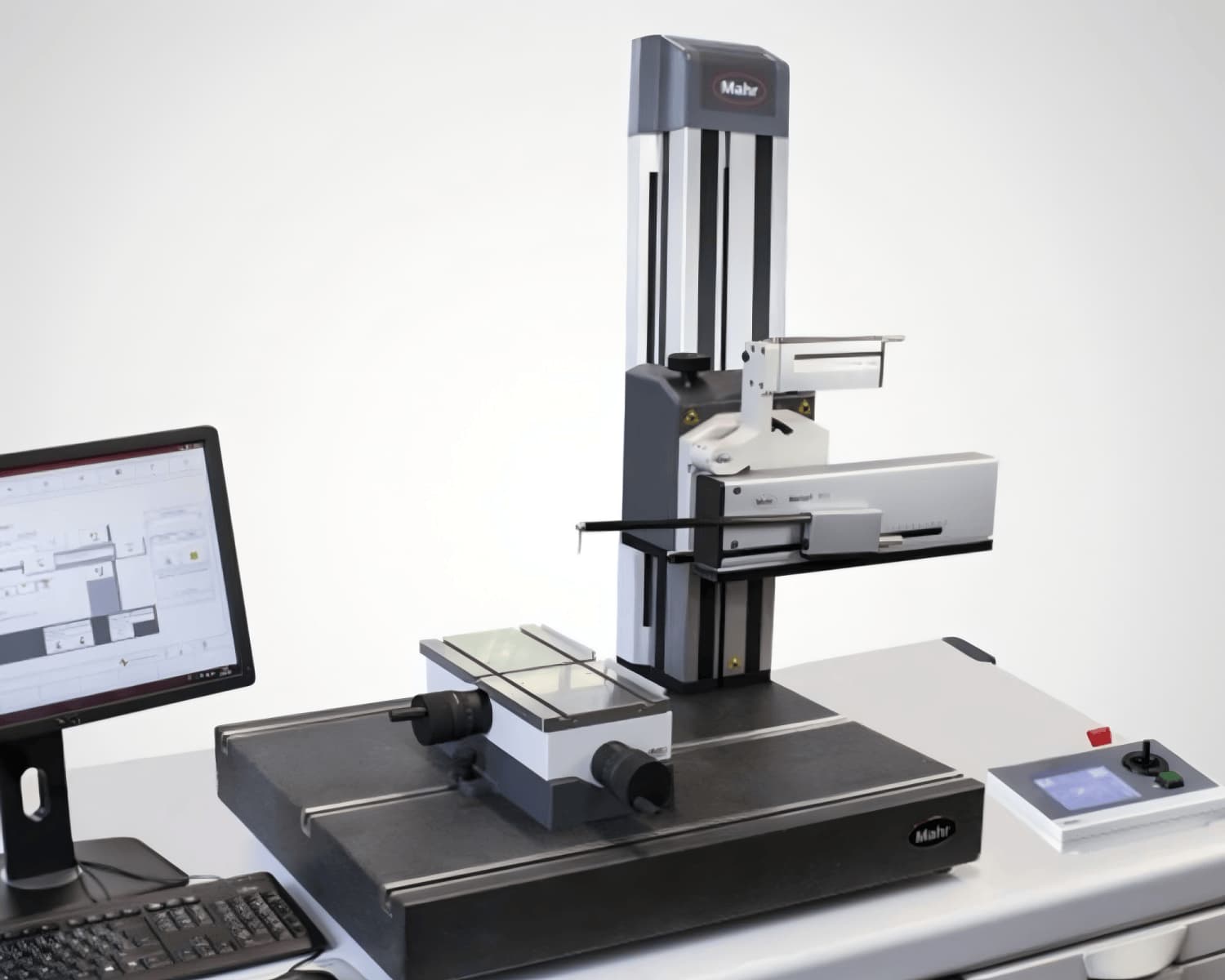
Profile Measuring Instrument
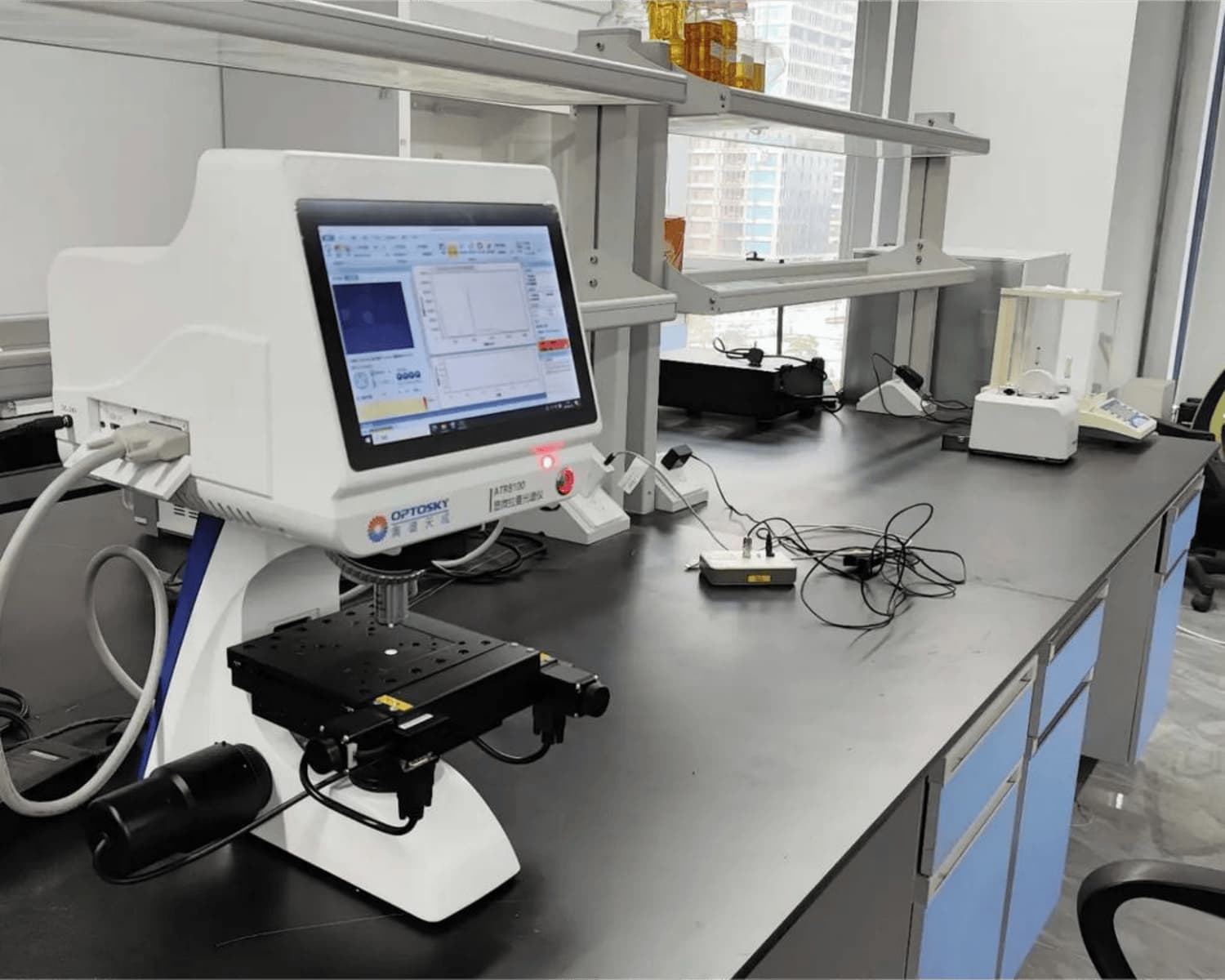
Spectrograph Instrument
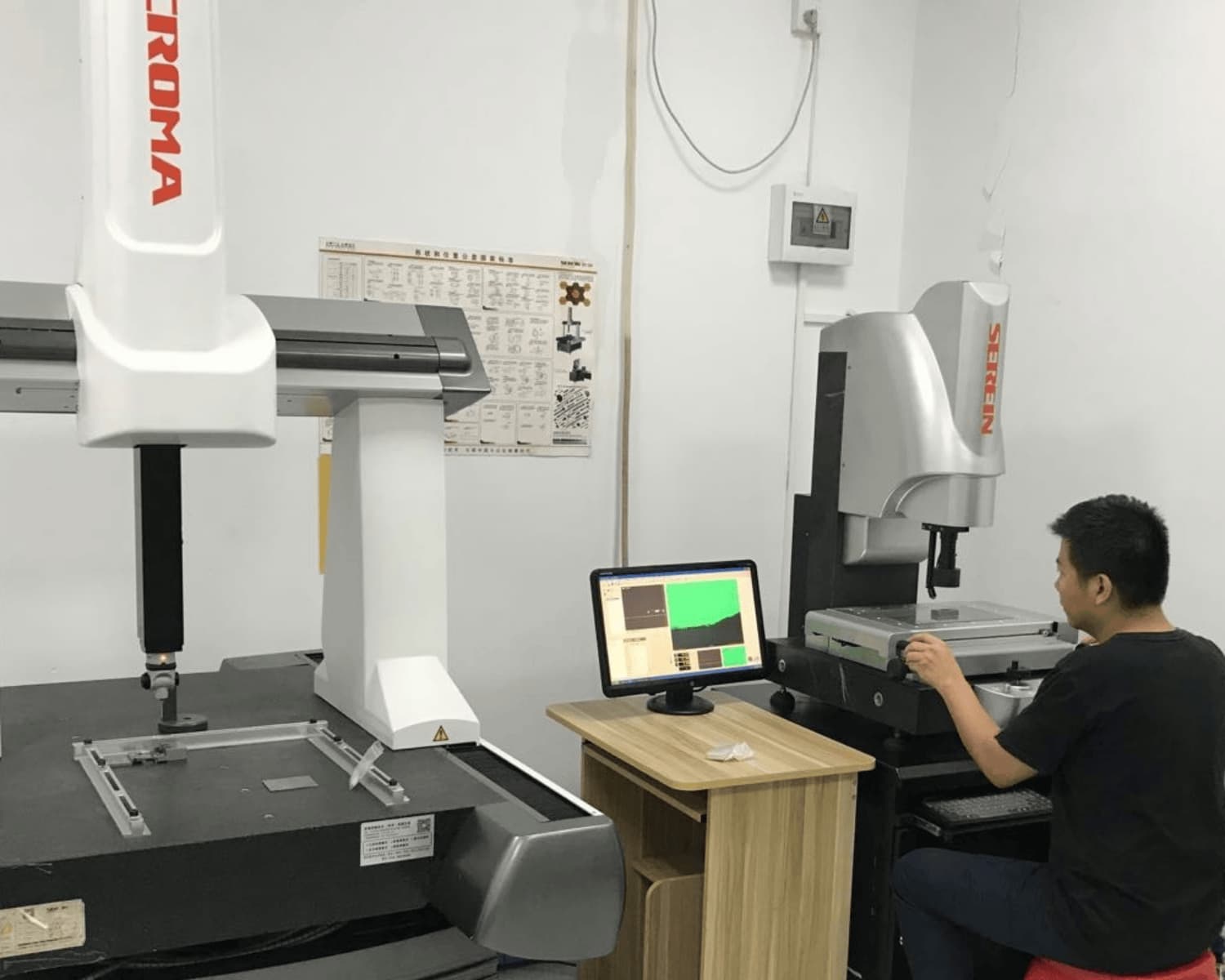
Three Coordinate Instrument
Company Profile
Xinzhe Metal Products Co., Ltd. was established in 2016 and focuses on the production of high-quality metal brackets and components, which are widely used in the construction, elevator, bridge, power, automotive parts and other industries. The main products include seismic pipe gallery brackets, fixed brackets, U-channel brackets, angle brackets, galvanized embedded base plates, elevator mounting brackets and fasteners, etc., which can meet the diverse project needs of various industries.
The company uses cutting-edge laser cutting equipment in conjunction with bending, welding, stamping, surface treatment, and other production processes to guarantee the precision and longevity of the products.
As an ISO 9001 certified company, we have worked closely with many international machinery, elevator and construction equipment manufacturers and provide them with the most competitive customized solutions.
According to the company's "going global" vision, we are dedicated to offering top-notch metal processing services to the global market and are constantly working to improve the quality of our products and services.
Packaging and Delivery
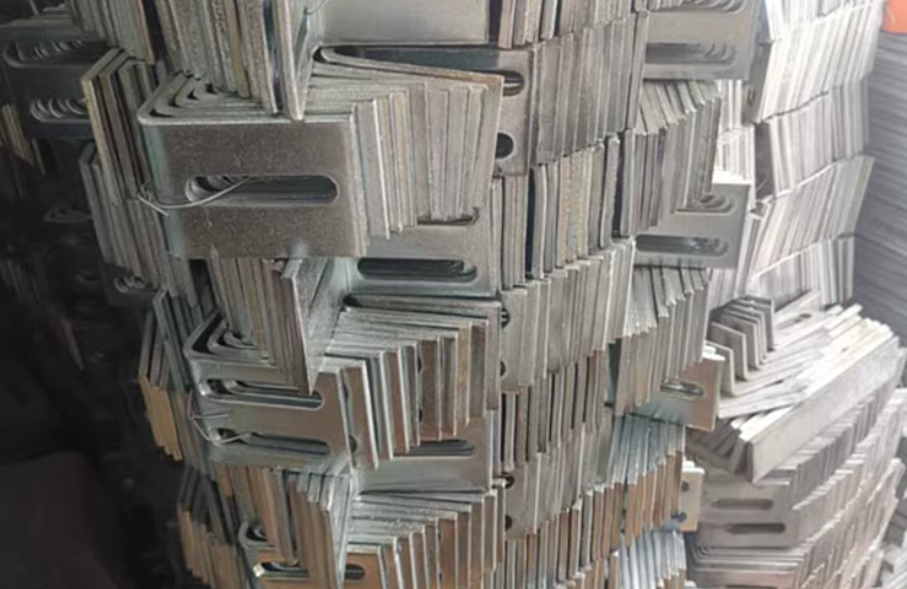
Angle Brackets
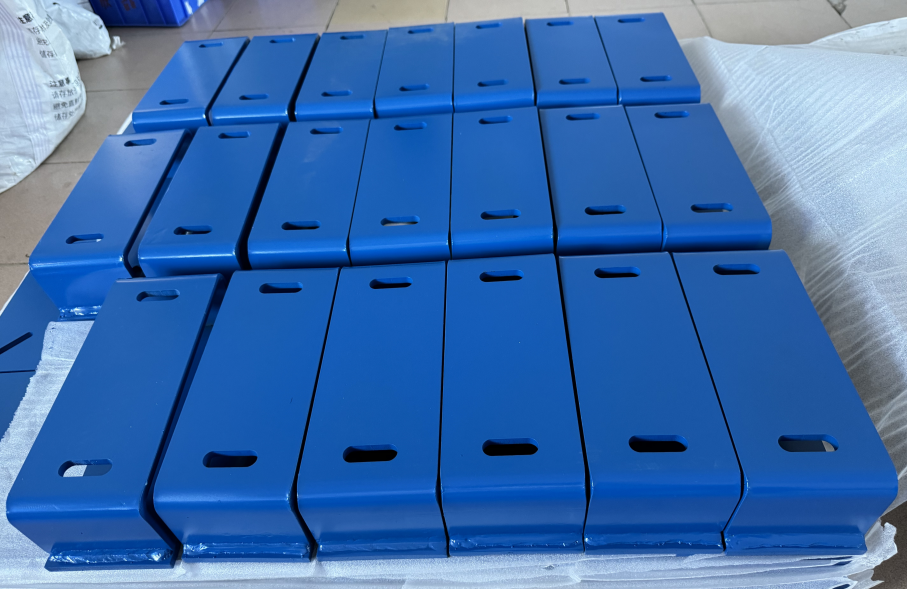
Elevator Mounting Kit
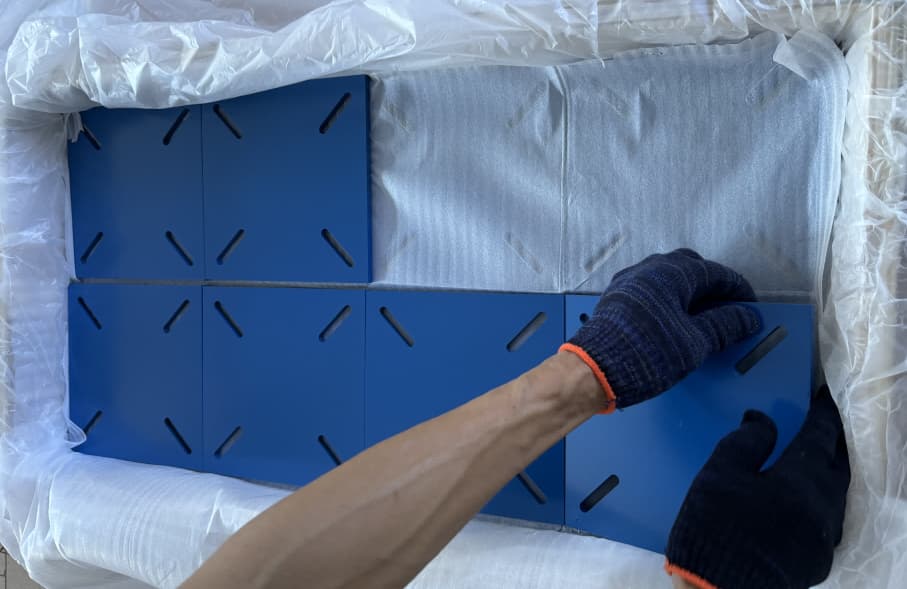
Elevator Accessories Connection Plate
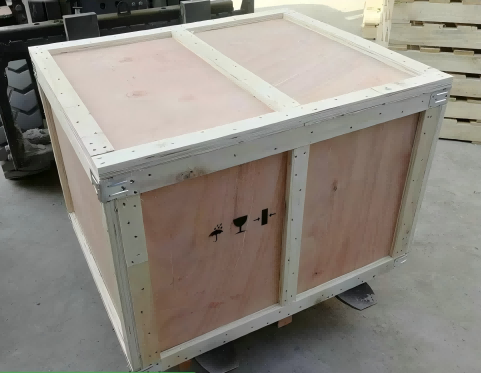
Wooden Box
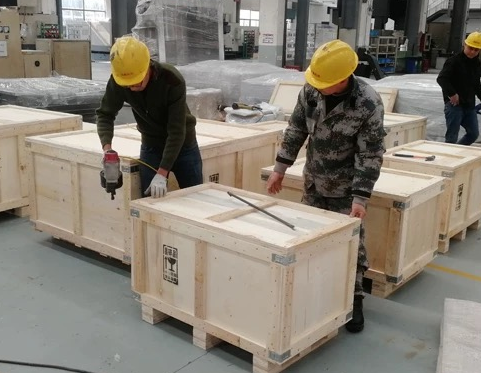
Packing
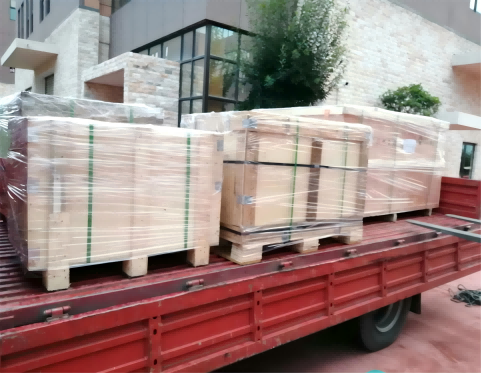
Loading
FAQ
1. What are stamping parts?
Stamping parts are parts that are formed by punching machines and dies on metal sheets. They are widely used in the automotive, mechanical equipment and construction industries.
2. What are the common materials for stamping parts?
Common materials include carbon steel, stainless steel, aluminum alloy, copper alloy and galvanized sheet, which have different strengths and corrosion resistance.
3. What is the dimensional tolerance of stamping parts?
The dimensional tolerance depends on the design requirements and the accuracy of the die, and is usually controlled within ±0.1mm. Special requirements can be further optimized.
4. What are the options for surface treatment of stamping parts?
Surface treatment methods include spraying, electroplating, polishing, anodizing and electrophoresis to enhance corrosion resistance, appearance and wear resistance.
5. Can stamping parts be customized?
Yes, they can be customized according to the customer's drawings or samples, including shape, size, material and surface treatment.
6. How long is the production cycle of stamping parts?
The production cycle varies depending on the order quantity and complexity. Usually, mold making takes 2-3 weeks, and the batch production cycle is about 1-2 weeks.
7. What is the minimum order quantity for stamping parts?
The minimum order quantity depends on the complexity of the product, generally 500-1000 pieces, and the specific quantity can be negotiated according to customer needs.
Multiple Transportation Options
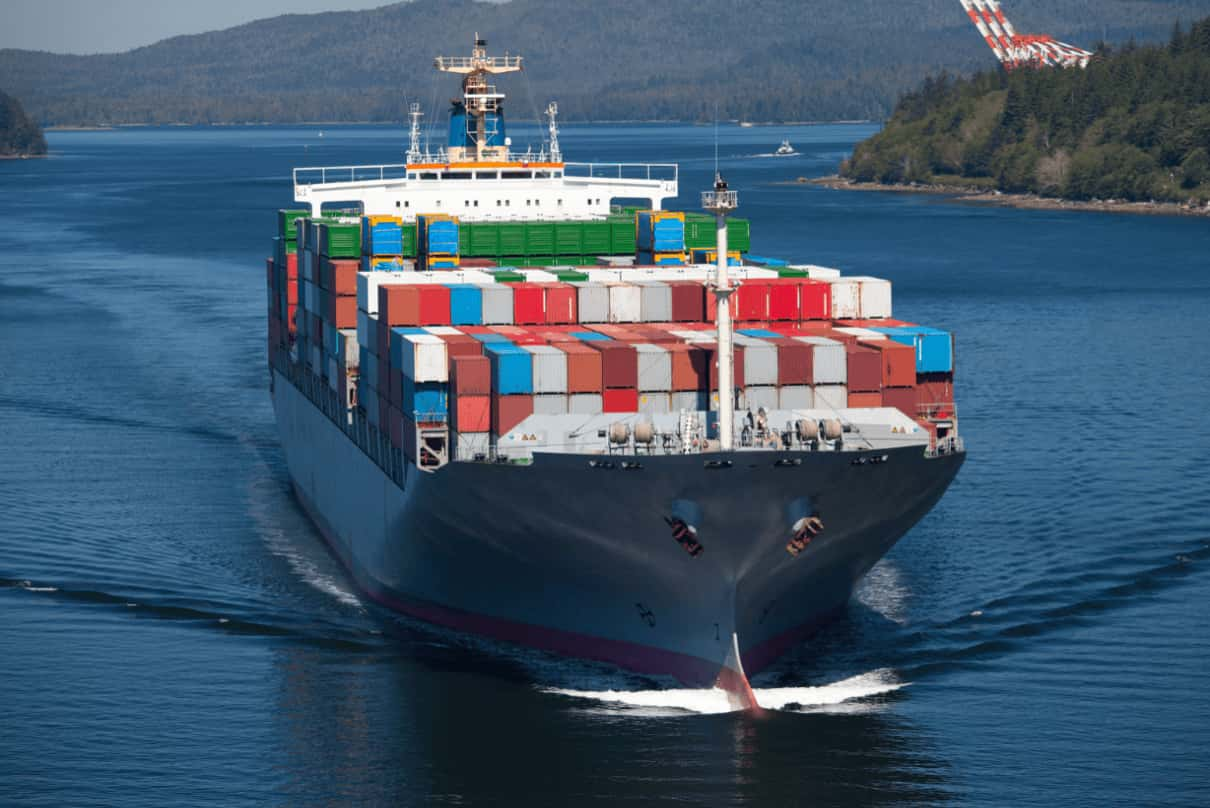
Ocean Freight
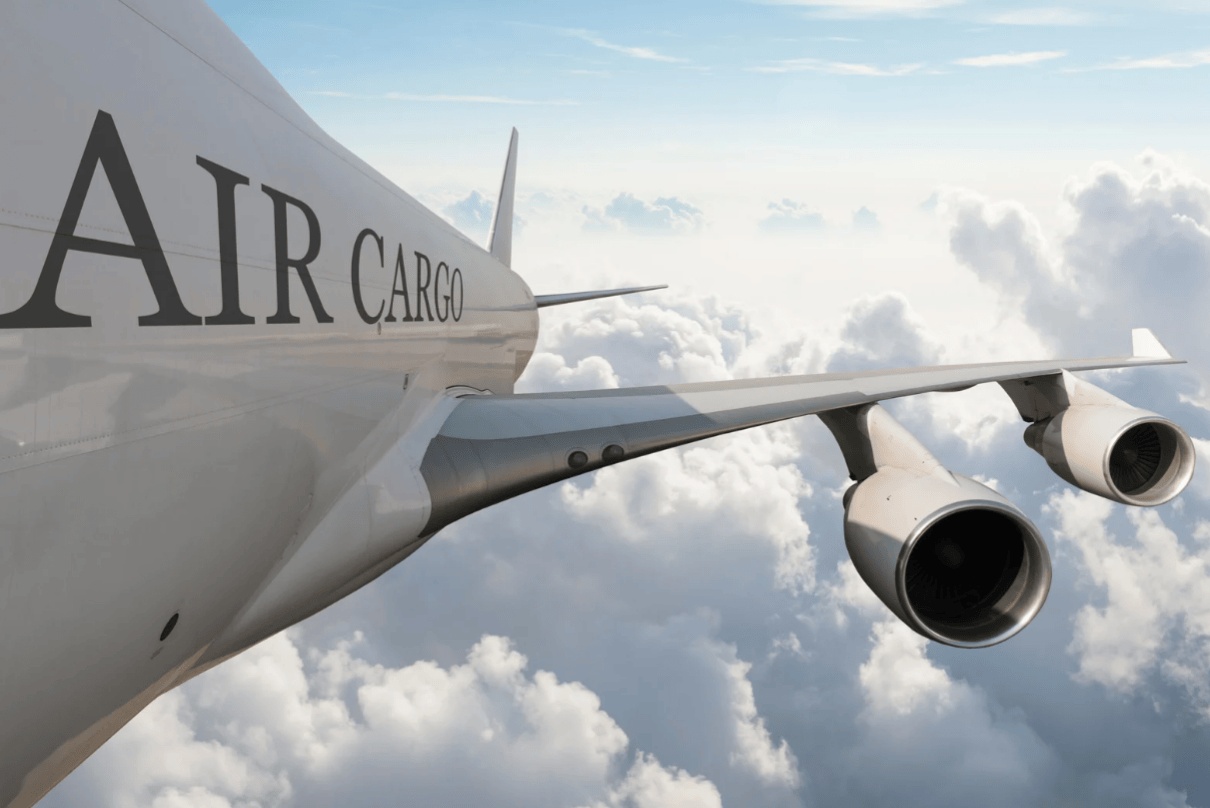
Air Freight
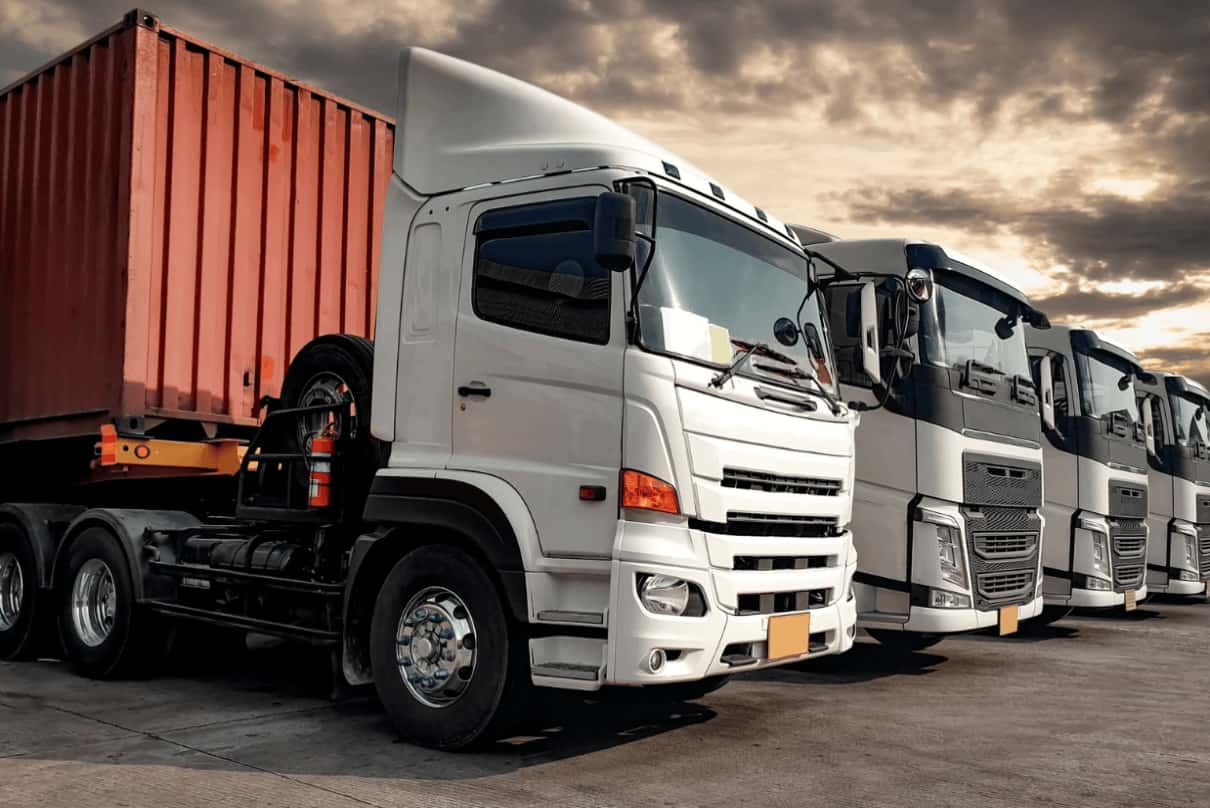
Road Transportation
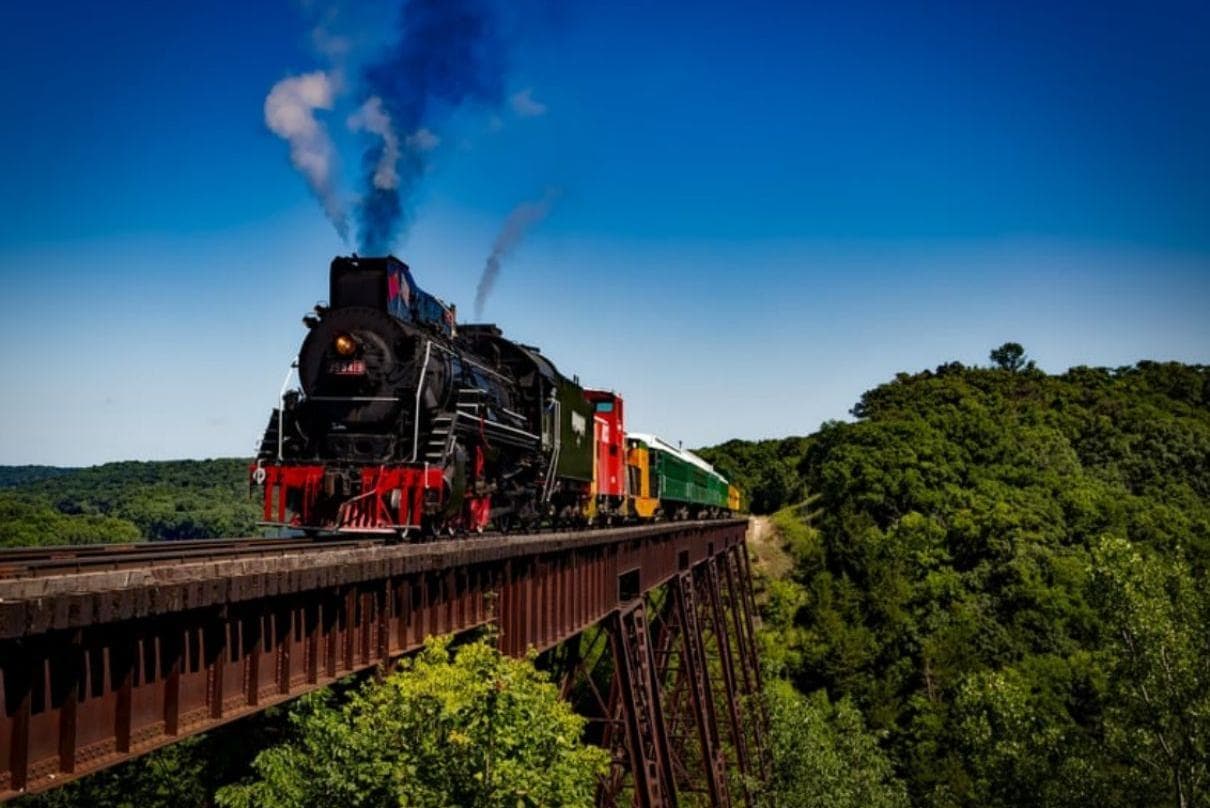