Zadziory są nieuniknionym problemem w procesie obróbki metalu. Niezależnie od tego, czy chodzi o wiercenie, toczenie, frezowanie czy cięcie płyt, powstawanie zadziorów wpłynie na jakość i bezpieczeństwo produktu. Zadziory nie tylko łatwo powodują skaleczenia, ale także wpływają na późniejszą obróbkę i montaż, zwiększając koszty produkcji. Aby zapewnić dokładność i jakość powierzchni gotowego produktu, gratowanie stało się niezbędnym procesem wtórnego przetwarzania, szczególnie w przypadku części precyzyjnych. Gratowanie i wykańczanie krawędzi może stanowić ponad 30% kosztów gotowego produktu. Jednak proces gratowania jest często trudny do zautomatyzowania, co utrudnia wydajność produkcji i kontrolę kosztów.
Popularne metody gratowania
Gratowanie chemiczne
Gratowanie chemiczne polega na usuwaniu zadziorów poprzez reakcję chemiczną. Poprzez wystawienie części na działanie określonego roztworu chemicznego jony chemiczne przylegają do powierzchni części, tworząc warstwę ochronną zapobiegającą korozji, a zadziory są usuwane poprzez reakcję chemiczną, ponieważ wystają z powierzchni. Ta metoda jest szeroko stosowana w dziedzinie pneumatyki, hydrauliki i maszyn inżynieryjnych, szczególnie do gratowania precyzyjnych części.
Gratowanie w wysokiej temperaturze
Gratowanie w wysokiej temperaturze polega na wymieszaniu części z gazem wodorowo-tlenowym w zamkniętej komorze, podgrzaniu ich do wysokiej temperatury i wysadzeniu w powietrze, aby wypalić zadziory. Ponieważ wysoka temperatura wytworzona przez wybuch działa tylko na zadziory i nie uszkadza części, ta metoda jest szczególnie odpowiednia dla części o złożonych kształtach.
Gratowanie bębna
Gratowanie bębnowe to metoda usuwania zadziorów poprzez jednoczesne użycie materiałów ściernych i części. Części i materiały ścierne umieszczane są w zamkniętym bębnie. Podczas obrotu bębna materiały ścierne i części ocierają się o siebie, generując siłę szlifowania w celu usunięcia zadziorów. Do powszechnie stosowanych materiałów ściernych należą piasek kwarcowy, wióry drzewne, tlenek glinu, ceramika i pierścienie metalowe. Ta metoda nadaje się do produkcji na dużą skalę i charakteryzuje się wysoką wydajnością przetwarzania.
Ręczne gratowanie
Ręczne gratowanie jest najbardziej tradycyjną, czasochłonną i pracochłonną metodą. Operatorzy używają narzędzi, takich jak pilniki stalowe, papier ścierny i głowice szlifierskie, aby ręcznie szlifować zadziory. Ta metoda nadaje się do małych partii lub części o złożonych kształtach, ale ma niską wydajność produkcji i wysokie koszty pracy, więc jest stopniowo zastępowana innymi, bardziej wydajnymi metodami.
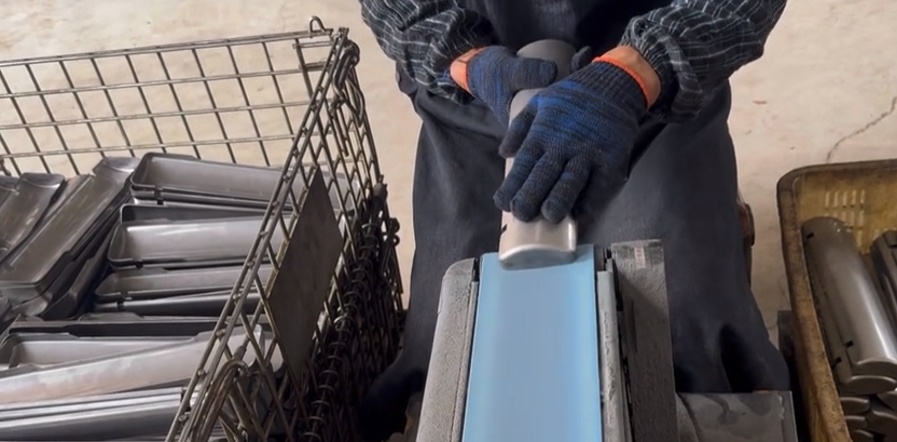
Proces gratowania
Proces gratowania usuwa ostre rogi poprzez zaokrąglanie krawędzi metalowych części. Zaokrąglanie krawędzi nie tylko usuwa ostrość lub zadziory, ale także poprawia powłokę powierzchniową części i zwiększa ich odporność na korozję. Zaokrąglanie krawędzi jest zwykle wykonywane przez obrotowe pilnikowanie, co jest odpowiednie dla części, które zostały wycięte laserowo, wytłoczone lub obrobione maszynowo.
Pilnikowanie obrotowe: rozwiązanie zapewniające wydajne gratowanie
Obrotowe pilniki to bardzo skuteczne narzędzie do gratowania, szczególnie do obróbki krawędzi części po cięciu laserowym, tłoczeniu lub obróbce skrawaniem. Obrotowe pilniki nie tylko usuwają zadziory, ale także wygładzają i zaokrąglają krawędzie poprzez obracanie się w celu szybkiego szlifowania, redukując problemy bezpieczeństwa, które mogą być spowodowane ostrymi krawędziami. Są szczególnie odpowiednie do obróbki części o złożonych kształtach lub dużych ilościach, pomagając zwiększyć wydajność produkcji i jakość produktu.
Proces gratowania
Proces gratowania usuwa ostre rogi poprzez zaokrąglanie krawędzi metalowych części. Zaokrąglanie krawędzi nie tylko usuwa ostrość lub zadziory, ale także poprawia powłokę powierzchniową części i zwiększa ich odporność na korozję. Zaokrąglanie krawędzi jest zwykle wykonywane przez obrotowe pilnikowanie, co jest odpowiednie dla części, które zostały wycięte laserowo, wytłoczone lub obrobione maszynowo.
Pilnikowanie obrotowe: rozwiązanie zapewniające wydajne gratowanie
Obrotowe pilniki to bardzo skuteczne narzędzie do gratowania, szczególnie do obróbki krawędzi części po cięciu laserowym, tłoczeniu lub obróbce skrawaniem. Obrotowe pilniki nie tylko usuwają zadziory, ale także wygładzają i zaokrąglają krawędzie poprzez obracanie się w celu szybkiego szlifowania, redukując problemy bezpieczeństwa, które mogą być spowodowane ostrymi krawędziami. Są szczególnie odpowiednie do obróbki części o złożonych kształtach lub dużych ilościach, pomagając zwiększyć wydajność produkcji i jakość produktu.
Główne czynniki wpływające na powstawanie zadziorów podczas frezowania trzpieniowego
1. Parametry frezowania, temperatura frezowania i środowisko skrawania będą miały pewien wpływ na powstawanie zadziorów. Wpływ niektórych głównych czynników, takich jak prędkość posuwu i głębokość frezowania, odzwierciedla teoria kąta wycięcia płaszczyzny i teoria sekwencji wyjścia końcówki narzędzia EOS.
2. Im większa plastyczność materiału obrabianego, tym łatwiej formować zadziory typu I. W procesie frezowania czołowego kruchych materiałów, jeśli prędkość posuwu lub kąt płaszczyzny cięcia jest duży, sprzyja to tworzeniu się zadziorów typu III (niedobór).
3. Gdy kąt między powierzchnią końcową przedmiotu obrabianego a obrabianą płaszczyzną jest większy od kąta prostego, powstawanie zadziorów można ograniczyć dzięki zwiększonej sztywności podparcia powierzchni końcowej.
4. Stosowanie płynu frezarskiego wydłuża żywotność narzędzia, zmniejsza jego zużycie, zapewnia smarowanie podczas frezowania, a tym samym zmniejsza wielkość zadziorów.
5. Zużycie narzędzia ma duży wpływ na powstawanie zadziorów. Gdy narzędzie jest zużyte do pewnego stopnia, łuk końcówki narzędzia zwiększa się, nie tylko zwiększa się rozmiar zadziorów w kierunku wyjścia narzędzia, ale także zadziory w kierunku cięcia narzędzia.
6. Inne czynniki, takie jak materiały narzędzi, również mają pewien wpływ na powstawanie zadziorów. W tych samych warunkach cięcia narzędzia diamentowe są bardziej sprzyjające powstrzymywaniu powstawania zadziorów niż inne narzędzia.
W rzeczywistości zadziory są nieuniknione w procesie obróbki, dlatego najlepiej jest rozwiązać problem zadziorów z perspektywy procesu, aby uniknąć nadmiernej ingerencji ręcznej. Użycie frezu trzpieniowego do fazowania może
Czas publikacji: 14-11-2024