ਸ਼ੀਟ ਮੈਟਲ ਪ੍ਰੋਸੈਸਿੰਗ ਦੇ ਖੇਤਰ ਵਿੱਚ, ਸਤਹ ਦਾ ਇਲਾਜ ਨਾ ਸਿਰਫ ਉਤਪਾਦ ਦੀ ਦਿੱਖ ਨੂੰ ਪ੍ਰਭਾਵਤ ਕਰਦਾ ਹੈ, ਬਲਕਿ ਸਿੱਧਾ ਇਸਦੀ ਟਿਕਾ riction ਰਚਨਾ, ਕਾਰਜਸ਼ੀਲਤਾ ਅਤੇ ਮਾਰਕੀਟ ਮੁਕਾਬਲੇਬਾਜ਼ੀ ਨਾਲ ਸੰਬੰਧਿਤ ਹੈ. ਕੀ ਇਹ ਉਦਯੋਗਿਕ ਉਪਕਰਣਾਂ, ਵਾਹਨ ਨਿਰਮਾਣ, ਜਾਂ ਇਲੈਕਟ੍ਰਾਨਿਕ ਉਪਕਰਣਾਂ, ਉੱਚ-ਗੁਣਵੱਤਾ ਵਾਲੇ ਸਤਹ ਦੇ ਇਲਾਜ ਦੀਆਂ ਪ੍ਰਕਿਰਿਆਵਾਂ ਵਿੱਚ ਕਾਫ਼ੀ ਸੁਧਾਰ ਕਰ ਸਕਦੀਆਂ ਹਨ. ਹੇਠ ਦਿੱਤੇ 10 ਮੁੱਖ ਸੁਝਾਅ ਸ਼ੀਟ ਮੈਟਲ ਸਤਹ ਦੇ ਇਲਾਜ ਦੇ ਪ੍ਰਕਿਰਿਆ ਦੇ ਪ੍ਰਵਾਹ ਨੂੰ ਅਨੁਕੂਲ ਬਣਾਉਣ ਵਿੱਚ ਤੁਹਾਡੀ ਸਹਾਇਤਾ ਲਈ ਡਿਜ਼ਾਇਨ ਕੀਤੇ ਗਏ ਹਨ ਅਤੇ ਵਧੇਰੇ ਪ੍ਰਭਾਵਸ਼ਾਲੀ ਨਤੀਜਿਆਂ ਨੂੰ ਪ੍ਰਾਪਤ ਕਰਨ ਵਿੱਚ ਸਹਾਇਤਾ ਕਰਦੇ ਹਨ.
ਸੰਕੇਤ 1: ਸਹੀ ਪ੍ਰੀ-ਟ੍ਰੀਟਮੈਂਟ
ਕਿਸੇ ਵੀ ਸਤਹ ਦੇ ਇਲਾਜ ਦੀ ਪ੍ਰਕਿਰਿਆ ਸ਼ੁਰੂ ਹੋਣ ਤੋਂ ਪਹਿਲਾਂ, ਸਤਹ ਦੇ ਇਲਾਜ ਨੂੰ ਪੂਰਾ ਕਰਨ ਦੇ ਪ੍ਰਭਾਵ ਨੂੰ ਪੂਰਾ ਕਰਨ ਦਾ ਪੂਰਾ ਅਧਾਰ ਹੈ.
ਸਤਹ ਦਾ ਤੇਲ ਹਟਾਉਣਾ, ਆਕਸਾਈਡ ਅਤੇ ਜੰਗਾਲ ਪਹਿਲਾ ਕੰਮ ਹੈ. ਤੁਸੀਂ ਭਿੱਜੇ, ਛਿੜਕਾਅ ਜਾਂ ਮੈਨੂਅਲ ਪੀਆਈਪੀਐਸ ਦੇ ਨਾਲ ਮਿਲ ਕੇ, ਪੇਸ਼ੇਵਰ ਡੀਗਰੀਆਰਜ਼ ਜਾਂ ਜੰਗਾਲਾਂ ਦੇ ਜੰਗਾਲਾਂ ਦੀ ਵਰਤੋਂ ਕਰ ਸਕਦੇ ਹੋ.
ਜ਼ਿੱਦੀ ਗੰਦਗੀ ਲਈ, ਮਕੈਨੀਕਲ ਪੀਸ (ਜਿਵੇਂ ਕਿ ਸੈਂਡਪੇਪਰ, ਪੀਸਣਾ ਚੱਕਰ, ਆਦਿ) ਦੀ ਵਰਤੋਂ ਕੀਤੀ ਜਾ ਸਕਦੀ ਹੈ.
ਓਪਰੇਟਿੰਗ ਕਰਨ ਵੇਲੇ ਧਿਆਨ ਦਿਓ:ਘਟਾਓਣਾ ਸਤਹ ਨੂੰ ਨੁਕਸਾਨ ਪਹੁੰਚਾਉਣ ਤੋਂ ਬਚਣ ਲਈ ਤਾਕਤ ਨੂੰ ਨਿਯੰਤਰਿਤ ਕਰੋ, ਖ਼ਾਸਕਰ ਪਤਲੇ ਸ਼ੀਟ ਮੈਟਲ ਹਿੱਸਿਆਂ ਲਈ.
ਸੁਧਾਰ ਦੇ ਸੁਝਾਅ: ਪ੍ਰੋਸੈਸਿੰਗ ਕੁਸ਼ਲਤਾ ਅਤੇ ਇਕਸਾਰਤਾ ਨੂੰ ਯਕੀਨੀ ਬਣਾਉਣ ਲਈ ਸਵੈਚਾਲਤ ਪ੍ਰੀਟਰੀਮੈਂਟ ਉਪਕਰਣ (ਜਿਵੇਂ ਕਿ ਸਪਰੇਅ ਪ੍ਰਣਾਲੀਆਂ) ਦੀ ਵਰਤੋਂ ਕਰੋ, ਖ਼ਾਸਕਰ ਵੱਡੇ ਪੱਧਰ 'ਤੇ ਉਤਪਾਦਨ ਵਿਚ.
ਸੰਕੇਤ 2: ਸਹੀ ਕੋਟਿੰਗ ਸਮੱਗਰੀ ਦੀ ਚੋਣ ਕਰੋ
ਵੱਖ ਵੱਖ ਵਰਤੋਂ ਦੇ ਦ੍ਰਿਸ਼ਾਂ ਦੀਆਂ ਸ਼ੀਟ ਮੈਟਲ ਹਿੱਸਿਆਂ ਦੀ ਕੋਟਿੰਗ ਸਮੱਗਰੀ ਲਈ ਵੱਖਰੀਆਂ ਜ਼ਰੂਰਤਾਂ ਹਨ:
ਬਾਹਰੀ ਵਾਤਾਵਰਣ: ਇਹ ਉੱਚ ਮੌਸਮ ਦੇ ਵਿਰੋਧ ਦੇ ਨਾਲ ਕੋਟਿੰਗ ਵਰਤਣ ਦੀ ਸਿਫਾਰਸ਼ ਕੀਤੀ ਜਾਂਦੀ ਹੈ, ਜਿਵੇਂ ਫਲੋਰੋਕਵਰਬਨ ਕੋਟਿੰਗ ਜਾਂ ਐਕਰੀਲਿਕ ਕੋਟਿੰਗ.
ਉੱਚ ਰਗੜ ਦੇ ਹਿੱਸੇ: ਪੌਲੀਯੂਰੇਥੇਨ ਕੋਟਿੰਗ ਜਾਂ ਵਸਰਾਵਿਕ ਪਰਤ ਪਾਉਣ ਵਾਲੇ ਵਿਰੋਧ ਨੂੰ ਵਧਾਉਣ ਨੂੰ ਤਰਜੀਹ ਦਿੰਦੇ ਹਨ.
ਉਸੇ ਸਮੇਂ, ਇਸ ਨੂੰ ਕੋਟਿੰਗ ਦੇ ਬਾਵਜੂਦ ਵੀ ਧਿਆਨ ਦੇਣਾ ਚਾਹੀਦਾ ਹੈ, ਜਿਸਦਾ ਪ੍ਰਾਈਮਰ ਦੁਆਰਾ ਸੁਧਾਰ ਕੀਤਾ ਜਾ ਸਕਦਾ ਹੈ. , ਵਿਸ਼ੇਸ਼ ਮੰਗ ਦੇ ਦ੍ਰਿਸ਼ਾਂ ਲਈ (ਜਿਵੇਂ ਐਂਟੀਬੈਕਟੀਰੀਅਲ ਜਾਂ ਇਨਸੂਲੇਟਿੰਗ ਸਤਹ), ਕਾਰਜਸ਼ੀਲ ਕੋਟਿੰਗਾਂ 'ਤੇ ਵਿਚਾਰ ਕੀਤਾ ਜਾ ਸਕਦਾ ਹੈ.
ਸੁਝਾਅ:ਵਾਤਾਵਰਣ ਦੀ ਦੋਸਤੀ ਅਤੇ ਘੱਟ VOC (ਅਸਥਿਰ ਜੈਵਿਕ ਅਹਾਤੇ) ਬਾਜ਼ਾਰ ਰੁਝਾਨ ਬਣ ਰਹੇ ਹਨ, ਅਤੇ ਹਰੇ ਅਤੇ ਵਾਤਾਵਰਣ ਦੇ ਅਨੁਕੂਲ ਕੋਟਿੰਗਾਂ ਨੂੰ ਤਰਜੀਹ ਦਿੱਤੀ ਜਾ ਸਕਦੀ ਹੈ.
ਸੰਕੇਤ 3: ਛਿੜਕਾਅ ਪ੍ਰਕਿਰਿਆ ਦੇ ਮਾਪਦੰਡਾਂ ਨੂੰ ਅਨੁਕੂਲ ਬਣਾਓ
ਪ੍ਰਕ੍ਰਿਆ ਦੇ ਮਾਪਦੰਡਾਂ ਨੂੰ ਸਿੱਧੇ ਕੋਟਿੰਗ ਦੀ ਗੁਣਵੱਤਾ ਅਤੇ ਦਿੱਖ ਨਿਰਧਾਰਤ ਕਰੋ:
ਬੰਦੂਕ ਦੀ ਦੂਰੀ: ਹੋਂਦ ਜਾਂ ਮੋਟੇ ਕਣਾਂ ਤੋਂ ਬਚਣ ਲਈ ਇਸ ਨੂੰ 15-25 ਸੈਮੀ ਦੇ ਵਿਚਕਾਰ ਰੱਖਿਆ ਜਾਣਾ ਚਾਹੀਦਾ ਹੈ.
ਛਿੜਕਾਅ ਦਾ ਦਬਾਅ: ਪੇਂਟ ਦੇ ਇਕਸਾਰ ਐਟਮਾਈਜ਼ੇਸ਼ਨ ਨੂੰ ਯਕੀਨੀ ਬਣਾਉਣ ਲਈ 0.0-0.6 ਐਮਪੀਏ ਦੇ ਵਿਚਕਾਰ 0.0-0.6 ਐਮ.ਪੀ.ਏ. ਦੇ ਵਿਚਕਾਰ.
ਸਪਰੇਅ ਸਪੀਡ ਅਤੇ ਐਂਗਲ: ਗੁੰਝਲਦਾਰ ਆਕਾਰ ਦੇ ਵਰਕਪੀਸਾਂ ਲਈ, ਕਿਨਾਰਿਆਂ ਅਤੇ ਗ੍ਰੋਵਿਆਂ ਤੇ ਵਰਦੀ ਕੋਟਿੰਗ ਕਵਰੇਜ ਨੂੰ ਯਕੀਨੀ ਬਣਾਉਣ ਲਈ ਸਪਰੇਅ ਬੰਦੂਕ ਦੇ ਕੋਣ ਨੂੰ ਵਿਵਸਥਿਤ ਕਰੋ.
ਸੁਧਾਰ ਦੇ ਸੁਝਾਅ:ਪ੍ਰਕਿਰਿਆ ਦੀ ਤਸਦੀਕ ਦੇ ਸਮੇਂ ਨਮੂਨੇ ਦੇ ਕੋਟਿੰਗ ਪ੍ਰਯੋਗਾਂ ਦਾ ਆਯੋਜਨ ਕਰੋ ਜਦੋਂ ਕਿ ਪੈਰਾਮੀਟਰ ਦੀ ਸੈਟਿੰਗ ਨੂੰ ਅਨੁਕੂਲਿਤ ਕਰੋ ਅਤੇ ਵੱਡੇ ਪੱਧਰ 'ਤੇ ਉਤਪਾਦਨ ਵਿੱਚ ਸਥਿਰਤਾ ਨੂੰ ਯਕੀਨੀ ਬਣਾਓ.
ਸੰਕੇਤ 4: ਇਲੈਕਟ੍ਰੋਸਟੈਟਿਕ ਸਪਰੇਅ ਟੈਕਨੋਲੋਜੀ ਦੀ ਵਰਤੋਂ ਕਰੋ
ਇਸ ਦੀਆਂ ਉੱਚ ਅਡਸੋਨ ਦਰ ਅਤੇ ਇਕਸਾਰਤਾ ਕਾਰਨ ਆਧੁਨਿਕ ਸਤਹ ਦੇ ਇਲਾਜ ਲਈ ਇਲੈਕਟ੍ਰੋਸਟੈਟਿਕ ਸਪਰੇਅ ਕਰਨਾ ਪਹਿਲਾ ਵਿਕਲਪ ਬਣ ਗਿਆ ਹੈ:
ਆਧਾਰਿਤ ਪ੍ਰਭਾਵ ਛਿੜਕਾਅ ਦੀ ਗੁਣਵੱਤਾ ਦੀ ਕੁੰਜੀ ਹੈ, ਅਤੇ ਪੇਸ਼ੇਵਰ ਆਧਾਰਿਤ ਉਪਕਰਣ ਨੂੰ ਸਥਿਰ ਬਿਜਲੀ ਦੇ ਖੇਤਰ ਨੂੰ ਯਕੀਨੀ ਬਣਾਉਣ ਲਈ ਇਸਤੇਮਾਲ ਕੀਤਾ ਜਾਣਾ ਚਾਹੀਦਾ ਹੈ.
ਸ਼ੀਟ ਮੈਟਲ ਦੀ ਜਟਿਲਤਾ ਦੇ ਅਨੁਸਾਰ ਇਲੈਕਟ੍ਰੋਸਟੈਟਿਕ ਵੋਲਟੇਜ ਵਿਵਸਥਿਤ ਕਰੋ, ਆਮ ਤੌਰ ਤੇ 50-80 ਕੇਵੀ ਦੇ ਵਿਚਕਾਰ ਨਿਯੰਤਰਿਤ.
ਅੰਨ੍ਹੇ ਛੇਕ ਜਾਂ ਅੰਦਰੂਨੀ ਛੱਪੜਾਂ ਵਾਲੇ ਗੁੰਝਲਦਾਰ ਵਰਕਪੀਸਾਂ ਲਈ, ਇਲੈਕਟ੍ਰਿਕ ਫੀਲਡ ਸ਼ੇਅਰ ਕੀਤੇ ਪ੍ਰਭਾਵ ਕਾਰਨ ਕੋਟਿੰਗ ਦੇ ਕਮਜ਼ੋਰ ਖੇਤਰਾਂ ਤੋਂ ਬਚਣ ਲਈ ਇਕ ਦੋਹਰਾ-ਗਨ ਪ੍ਰਣਾਲੀ ਜਾਂ ਮੈਨੁਅਲ ਸਪਰੇਅ ਸਪਰੇਅ ਕਰਨ ਲਈ ਵਰਤਿਆ ਜਾ ਸਕਦਾ ਹੈ.
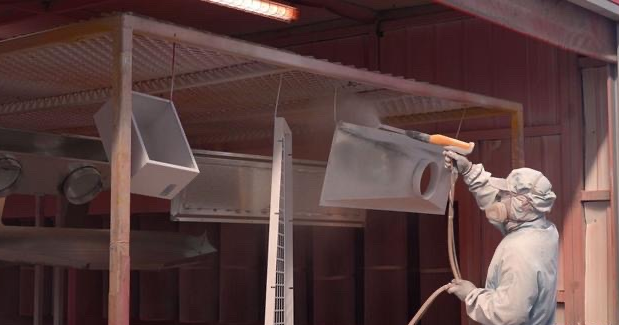
ਸੰਕੇਤ 5: ਫਾਸਫੇਟਿੰਗ ਦਾ ਇਲਾਜ ਐਂਟੀ-ਖੋਰ ਦੀ ਕਾਰਗੁਜ਼ਾਰੀ ਨੂੰ ਵਧਾਉਂਦਾ ਹੈ
ਫਾਸਫੇਟਿੰਗ ਦਾ ਇਲਾਜ ਘਟਾਓਣਾ ਦੇ ਖੋਰ ਟਾਕਰੇ ਨੂੰ ਹੀ ਨਹੀਂ ਸੁਧਾਰ ਸਕਦਾ, ਪਰ ਬਾਅਦ ਵਾਲੇ ਕੋਟਿੰਗਾਂ ਦੀ ਅਡੱਸੀਨ ਨੂੰ ਵਧਾਉਣਾ:
ਤਾਪਮਾਨ ਨਿਯੰਤਰਣ: ਸਟੀਲ ਲਈ ਸਿਫਾਰਸ਼ੀ ਫਾਸਫਿੰਗ ਤਾਪਮਾਨ 50-70 ℃ ਦੇ ਵਿਚਕਾਰ ਹੈ. ਬਹੁਤ ਜ਼ਿਆਦਾ ਜਾਂ ਬਹੁਤ ਘੱਟ ਫਾਸਫੇਟਿੰਗ ਫਿਲਮ ਦੀ ਇਕਸਾਰਤਾ ਨੂੰ ਪ੍ਰਭਾਵਤ ਕਰੇਗਾ.
ਸਮਾਂ ਸੈਟਿੰਗ: ਆਮ ਤੌਰ 'ਤੇ 3-10 ਮਿੰਟ, ਸਮੱਗਰੀ ਅਤੇ ਪ੍ਰਕਿਰਿਆ ਦੀਆਂ ਜ਼ਰੂਰਤਾਂ ਦੇ ਅਨੁਸਾਰ ਵਿਵਸਥਤ.
ਅਪਗ੍ਰੇਡ ਸੁਝਾਅ: ਉਦਯੋਗਿਕ ਰਹਿੰਦ-ਖੂੰਹਦ ਦੇ ਇਲਾਜ ਨੂੰ ਘਟਾਉਣ ਲਈ ਘੱਟ-ਤਾਪਮਾਨ ਫੁੱਫਿੰਗ ਤਕਨਾਲੋਜੀ ਦੀ ਵਰਤੋਂ ਕਰੋ.
ਸੰਕੇਤ 6: ਇਲੈਕਟ੍ਰੋਲੇਟਿੰਗ ਪ੍ਰਕਿਰਿਆ ਦੇ ਕੋਰ ਪੁਆਇੰਟਸ ਨੂੰ ਮਾਲਕ ਬਣਾਓ
ਇਲੈਕਟ੍ਰੋਲੇਟਿੰਗ ਵਧੀਆ ਸਜਾਵਟੀ ਅਤੇ ਸੁਰੱਖਿਆ ਵਾਲੀਆਂ ਵਿਸ਼ੇਸ਼ਤਾਵਾਂ ਪ੍ਰਦਾਨ ਕਰ ਸਕਦੀ ਹੈ, ਪਰ ਇਸ ਨੂੰ ਪ੍ਰਕਿਰਿਆ ਦੇ ਉੱਚ ਸ਼ੁੱਧਤਾ ਦੇ ਨਿਯੰਤਰਣ ਦੀ ਜ਼ਰੂਰਤ ਹੈ:
ਮੌਜੂਦਾ ਘਣਤਾ ਅਤੇ ਤਾਪਮਾਨ ਦੀ ਸਖਤੀ ਨਾਲ ਮੇਲ ਖਾਂਦਾ ਹੋਣਾ ਚਾਹੀਦਾ ਹੈ. ਉਦਾਹਰਣ ਦੇ ਲਈ, ਜਦੋਂ ਗੈਲਵੈਨਾਈਜ਼ ਕਰਨਾ, ਤਾਪਮਾਨ 20-30 ℃ ਦੇ ਵਿਚਕਾਰ ਹੋਣਾ ਚਾਹੀਦਾ ਹੈ ਅਤੇ ਮੌਜੂਦਾ ਘਣਤਾ ਨੂੰ 2-4 ਏ / ਡੀਐਮਟੀ ਤੇ ਰੱਖਣਾ ਚਾਹੀਦਾ ਹੈ.
ਕੋਟਿੰਗ ਦੇ ਨਿਰਵਿਘਨਤਾ ਅਤੇ ਘਣਤਾ ਨੂੰ ਯਕੀਨੀ ਬਣਾਉਣ ਲਈ ਇਲੈਕਟ੍ਰੋਫਲੇਟਿੰਗ ਦੇ ਹੱਲਾਂ ਦੀ ਗਾੜ੍ਹਾਪਣ ਦੀ ਨਿਯਮਤਤਾ ਦੀ ਨਿਗਰਾਨੀ ਕੀਤੀ ਜਾਣੀ ਚਾਹੀਦੀ ਹੈ.
ਨੋਟ: ਇਲੈਕਟ੍ਰੋਲੇਟਿੰਗ ਤੋਂ ਬਾਅਦ ਸਫਾਈ ਮਹੱਤਵਪੂਰਨ ਹੈ. ਬਚੇ ਹੋਏ ਇਲੈਕਟ੍ਰੋਲੇਟਿੰਗ ਦਾ ਹੱਲ ਕੋਟਿੰਗ ਦੀ ਸਤਹ 'ਤੇ ਧੁੰਦ ਜਾਂ ਖੋਰ ਦਾ ਕਾਰਨ ਬਣ ਸਕਦਾ ਹੈ.
ਸੰਕੇਤ 7: ਅਨੌਡੀਜਿੰਗ (ਅਲਮੀਨੀਅਮ ਦੇ ਹਿੱਸੇ ਲਈ ਵਿਸ਼ੇਸ਼)
ਅਨੌਡਿਅਲਿੰਗ ਕੋਰਿਨੀਅਮ ਸ਼ੀਟ ਮੈਟਲ ਹਿੱਸਿਆਂ ਦੇ ਖੋਰ ਦੇ ਵਿਰੋਧ ਅਤੇ ਸਜਾਵਟੀ ਪ੍ਰਭਾਵ ਨੂੰ ਸੁਧਾਰਨ ਲਈ ਕੋਰ ਪ੍ਰਕਿਰਿਆ ਹੈ:
ਵੋਲਟੇਜ ਨੂੰ 10-20 V 'ਤੇ ਨਿਯੰਤਰਿਤ ਕਰਨ ਦੀ ਸਿਫਾਰਸ਼ ਕੀਤੀ ਜਾਂਦੀ ਹੈ, ਅਤੇ ਪ੍ਰੋਸੈਸਿੰਗ ਸਮਾਂ ਲੋੜਾਂ ਅਨੁਸਾਰ ਵਿਵਸਥਿਤ ਹੁੰਦਾ ਹੈ (20-60 ਮਿੰਟ).
ਸਿੰਜਾਈ ਅਤੇ ਸੀਲਿੰਗ ਤੋਂ ਬਾਅਦ ਐਂਟੀ inuxidentant ਸਮਰੱਥਾ ਅਤੇ ਰੰਗ ਦੀ ਟਿਕਾ .ਤਾ ਨੂੰ ਵਧਾਉਣ ਦੇ ਮੁੱਖ ਕਦਮ ਹਨ.
ਉੱਨਤ ਤਕਨਾਲੋਜੀ: ਆਕਸਾਈਡ ਫਿਲਮ ਦੇ ਕਠੋਰ ਫਿਲਮ ਨੂੰ ਹੋਰ ਵਧਾਉਣ ਲਈ ਮਾਈਕਰੋ-ਆਰਕ ਆਕਸੀਡੇਸ਼ਨ (ਮਾਓ) ਤਕਨਾਲੋਜੀ ਦੀ ਵਰਤੋਂ ਕਰੋ.
ਸੰਕੇਤ 8: ਸਤਹ ਨੂੰ ਪੀਸਣਾ ਅਤੇ ਸ਼ੁੱਧਤਾ ਨੂੰ ਸੁਧਾਰਨ ਲਈ ਪਾਲਿਸ਼ ਕਰਨਾ
ਉੱਚ ਪੱਧਰੀ ਸਤਹ ਦਾ ਇਲਾਜ ਪੀਸਣ ਅਤੇ ਪਾਲਿਸ਼ ਕਰਨ ਤੋਂ ਅਟੁੱਟ ਹੁੰਦਾ ਹੈ:
ਸੈਂਡਪਰ ਚੋਣ: ਮੋਟੇ ਤੋਂ ਜੁਰਮਾਨੇ ਤੋਂ, ਕਦਮ ਦਰ ਕਦਮ 320 # ਜਾਂ ਵੱਧ ਜਾਲ ਵਿੱਚ ਤਬਦੀਲੀ.
ਇਕਸਾਰ ਕਾਰਜ: ਧੱਫੜ ਦੀ ਦਿਸ਼ਾ ਇਕ ਅਜਿਹੀ ਮੌਜੂਦਗੀ ਨੂੰ ਪ੍ਰਭਾਵਤ ਕਰਨ ਵਾਲੇ ਕਰਾਸ ਡਰਾਵਾਂ ਤੋਂ ਬਚਣ ਲਈ ਇਕਸਾਰ ਹੋਣੀ ਚਾਹੀਦੀ ਹੈ.
ਉੱਚ ਗਲੋਸ ਦੀਆਂ ਜ਼ਰੂਰਤਾਂ ਵਾਲੇ ਵਰਕਪੀਸਾਂ ਲਈ, ਪ੍ਰਭਾਵ ਨੂੰ ਬਿਹਤਰ ਬਣਾਉਣ ਲਈ ਸ਼ੀਸ਼ੇ ਦੇ ਪਾਲਿਸ਼ ਕਰਨ ਜਾਂ ਕਪੜੇ ਦੇ ਪੇਸਟ ਜਾਂ ਕ੍ਰੋਮਿਅਮ ਆਕਸਾਈਡ ਪੇਸਟ ਦੇ ਨਾਲ ਜੋੜਿਆ ਜਾ ਸਕਦਾ ਹੈ.
ਸੰਕੇਤ 9: ਕੁਆਲਟੀ ਨਿਰੀਖਣ ਅਤੇ ਪ੍ਰਕਿਰਿਆ ਨਿਯੰਤਰਣ ਨੂੰ ਮਜ਼ਬੂਤ ਕਰੋ
ਸਤਹ ਦੇ ਇਲਾਜ ਦੀ ਗੁਣਵੱਤਾ ਦੀ ਸਥਿਰਤਾ ਨਿਰੀਖਣ ਅਤੇ ਨਿਯੰਤਰਣ ਤੋਂ ਅਟੁੱਟ ਹੈ:
ਪਤੰਗ ਗੇਜ: ਕੋਟਿੰਗ ਮੋਟਾਈ ਦਾ ਪਤਾ ਲਗਾਓ.
ਅਦਨ ਦਾ ਟੈਸਟ: ਜਿਵੇਂ ਕਿ ਕਰਾਸ-ਕੱਟਣ ਜਾਂ ਖਿੱਚ-ਰਹਿਤ ਟੈਸਟ, ਇਹ ਤਸਦੀਕ ਕਰਨ ਲਈ ਕਿ ਕੋਟਿੰਗ ਪੱਕਾ ਹੈ.
ਲੂਣ ਸਪਰੇਅ ਟੈਸਟ: ਖੋਰ ਟਾਕਰੇ ਦਾ ਮੁਲਾਂਕਣ ਕਰਨ ਲਈ.
ਸੁਧਾਰ ਦੇ ਸੁਝਾਅ: ਆਟੋਮੈਟਿਕ ਟੈਸਟਿੰਗ ਉਪਕਰਣਾਂ ਨੂੰ ਪੇਸ਼ ਕਰਕੇ, ਟੈਸਟ ਦੀ ਕੁਸ਼ਲਤਾ ਨੂੰ ਯਕੀਨੀ ਬਣਾ ਕੇ, ਰੀਅਲ-ਟਾਈਮ ਪ੍ਰਕਿਰਿਆ ਓਪਟੀਮਾਈਜ਼ੇਸ਼ਨ ਲਈ ਡਾਟਾ ਵਿਸ਼ਲੇਸ਼ਣ ਨੂੰ ਯਕੀਨੀ ਬਣਾਓ.
ਸੰਕੇਤ 10: ਨਿਰੰਤਰ ਸਿਖਲਾਈ ਅਤੇ ਤਕਨੀਕੀ ਅਵਿਸ਼ਕਾਰ
ਸਤਹ ਦਾ ਇਲਾਜ ਤਕਨਾਲੋਜੀ ਹਰ ਲੰਘਦੇ ਦਿਨ ਨਾਲ ਬਦਲ ਰਹੀ ਹੈ, ਅਤੇ ਤਕਨੀਕੀ ਲੀਡਰਸ਼ਿਪ ਨੂੰ ਬਣਾਈ ਰੱਖਣ ਲਈ:
ਉਦਯੋਗ ਦੇ ਰੁਝਾਨਾਂ ਵੱਲ ਧਿਆਨ ਦਿਓ: ਪ੍ਰਦਰਸ਼ਨੀ ਅਤੇ ਸੈਮੀਨਾਰਾਂ ਵਿੱਚ ਹਿੱਸਾ ਲੈਣ ਨਾਲ ਨਵੀਨਤਮ ਪ੍ਰਕਿਰਿਆ ਦੇ ਰੁਝਾਨਾਂ ਨੂੰ ਸਮਝੋ.
ਟੈਕਨੋਲੋਜੀ ਆਰ ਐਂਡ ਡੀ ਇਨਵੈਸਟ: ਕੁਸ਼ਲਤਾ ਅਤੇ ਵਾਤਾਵਰਣ ਸੁਰੱਖਿਆ ਦੇ ਪੱਧਰ ਨੂੰ ਸੁਧਾਰਨ ਲਈ ਬੁੱਧੀਜੀਨ ਉਪਕਰਣਾਂ ਅਤੇ ਦੋ ਵਾਤਾਵਰਣ ਦੇ ਅਨੁਕੂਲ ਸਮੱਗਰੀ ਪੇਸ਼ ਕਰਦੇ ਹਨ.
ਉਦਾਹਰਣ ਦੇ ਲਈ, ਨੈਨੋ ਕੋਟਿੰਗਾਂ ਅਤੇ ਪਲਾਜ਼ਮਾ ਸਪਰੇਅ ਨੂੰ ਹੌਲੀ ਹੌਲੀ ਤਰੱਕੀ ਦਿੱਤੀ ਜਾ ਰਹੀ ਹੈ, ਹੌਲੀ ਹੌਲੀ ਉਤਸ਼ਾਹਿਤ ਕੀਤੀ ਜਾ ਰਹੀ ਹੈ.
ਪੋਸਟ ਟਾਈਮ: ਦਸੰਬਰ-06-2024