The difference and application of galvanizing, electrophoresis and spraying
In the metal processing industry, the surface treatment process directly affects the product's anti-corrosion performance, wear resistance and aesthetics. There are three common surface treatment methods: galvanizing, electrophoresis and spraying. They each have their own characteristics and are suitable for different application scenarios. We will compare and analyze the characteristics, advantages and disadvantages and application fields of these three processes. The data is for reference only.
1. Galvanizing
Process Introduction
Galvanizing is a process that prevents corrosion by covering the metal surface with a layer of zinc, mainly including hot-dip galvanizing and electro-galvanizing.
Main Features
Hot-dip galvanizing: immerse the metal product in a high-temperature zinc solution to form a uniform zinc layer on its surface.
● Zinc layer thickness: 50-150μm
● Corrosion resistance: excellent, suitable for outdoor environments
● Surface state: rough, silver-gray, zinc flowers may appear
Electrogalvanizing
A zinc layer is deposited on the metal surface through an electrolytic process to form a thin protective layer.
Zinc layer thickness: 5-30μm
Corrosion resistance: General, suitable for indoor environments
Surface state: smooth, high brightness
Applicable scenarios
● Hot-dip galvanizing: bridge structures, building supports, power towers, outdoor pipelines, heavy machinery, etc.
● Electrogalvanizing: small fasteners, indoor metal parts, home appliance housings, automotive parts, etc.
Advantages and disadvantages
Advantages: strong anti-corrosion ability, economical and durable, hot-dip galvanizing is suitable for harsh environments
Disadvantages: Electrogalvanizing has relatively weak anti-corrosion ability, and the surface of hot-dip galvanizing is rough, which may affect the appearance
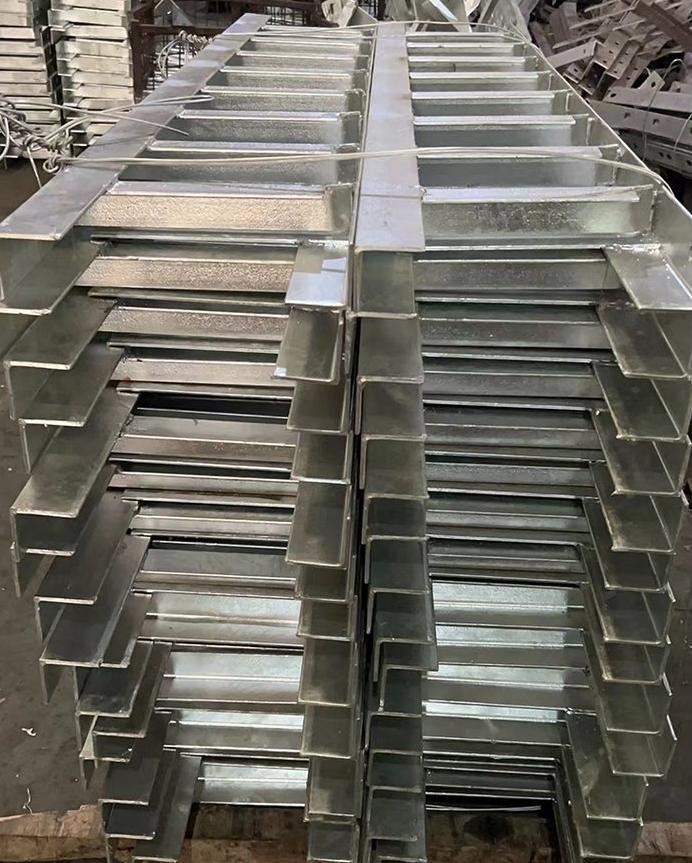
2. Electrophoretic Coating
Process Introduction
Electrophoretic coating is a coating process that uses electric field to make the paint adhere evenly to the metal surface. It is widely used in the automotive, home appliance and other industries.
Main features
● Adopting anodic or cathodic electrophoresis technology, the coating is uniform and the coating utilization rate is high
● Forming a dense organic coating, usually used with phosphating or galvanizing treatment to enhance the anti-corrosion performance
● Film thickness: 15-35μm (adjustable)
● Color: optional (commonly black and gray)
Applicable scenarios
● Car parts (frame, suspension system, brake caliper)
● Building hardware (metal brackets, fasteners, pipe fittings)
● Elevator rails, mechanical parts
Advantages: uniform coating, strong adhesion, good anti-corrosion performance, environmental protection and energy saving
Disadvantages: complex process flow, high requirements for equipment, and high initial cost
3. Spraying
Process Introduction
Spraying is divided into powder spraying (electrostatic spraying) and liquid spraying. Powder spraying uses electrostatic action to make the powder adsorb on the metal surface and form a coating through high temperature curing; liquid spraying uses a spray gun to directly spray paint, which is common in scenes requiring rich colors.
Main features
Powder spraying:
● Coating thickness: 50-200μm
● Excellent wear resistance and corrosion resistance, suitable for outdoor and industrial environments
Environmentally friendly, solvent-free
Liquid spray painting:
● Coating thickness: 10-50μm
● Rich colors, suitable for fine decoration
● Local repairs can be performed
Applicable scenarios
● Powder spraying: building brackets, guardrails, electrical housings, outdoor equipment
● Liquid spray painting: high-end home appliances, decorative metal products, signs
Advantages: Powder spraying has thick coating and good durability; liquid spray painting has rich colors and a wide range of applications
Disadvantages: Powder spraying cannot be locally repaired, and liquid spray painting is less environmentally friendly
Selection suggestions:
● Requires extremely strong anti-corrosion performance (such as bridges, power towers, elevator steel structures) → Hot dip galvanizing
● Requires smooth surface and general anti-corrosion (such as fasteners, auto parts) → Electrogalvanizing
● Requires uniform coating and high corrosion resistance (such as elevator guide rails, auto parts) → Electrophoretic coating
● Need good wear resistance and weather resistance (such as building brackets, electrical housings) → Powder spraying
● Need colorful appearance and fine decoration (such as home appliances, signboards) → Liquid spray painting
Different processes have their own characteristics. Choosing the right surface treatment method needs to be based on the product's use environment, functional requirements and cost considerations. Xinzhe Metal Products can provide professional surface treatment solutions according to customer needs, welcome to consult!
Post time: Apr-03-2025