As an indispensable component in the manufacturing industry, metal brackets play an important role in almost every industrial field. From structural support to assembly and fixation, to improving production efficiency and adapting to complex application scenarios, their application range is very wide and their functions are also diverse.
1. The core role of metal brackets
Provide structural support
Its primary role is to provide structural support to ensure the stability and safety of equipment or systems. For example, in construction projects, metal support brackets are used for stair handrails, pipe supports, bridge reinforcement, etc.; in the field of elevator manufacturing, guide rail brackets are important components to ensure the smooth operation of elevators. High strength and durability enable steel brackets to cope with large loads and harsh environments.
Assembly and fixation
Metal stamping brackets are widely used for component assembly and fixation. They are particularly common in the automotive, home appliance, and mechanical processing industries. For example, in automotive manufacturing, they can be used to fix engines, suspension systems, seat frames, etc.; in the home appliance industry, they are used for refrigerator inner boxes and air conditioner external unit brackets. The precise positioning ability of the bracket significantly improves assembly efficiency and product quality.
Improve production efficiency
In the modern manufacturing industry with an increasingly high degree of automation, metal brackets simplify the production process through modular design. For example, on the assembly line, they are used to fix conveyor belts and robotic arm equipment to ensure efficient operation. Its fast assembly and disassembly characteristics not only shorten the production time, but also provide support for flexible production mode.
Enhance durability and safety
Metal brackets are often designed with anti-fatigue, anti-corrosion, and impact resistance in mind, which makes them particularly prominent in high-demand industries. For example, in the aerospace field, brackets need to withstand high-intensity use and complex environmental conditions; in medical equipment, metal brackets need to support high-precision instruments stably for a long time, and surface treatment technologies (such as hot-dip galvanizing and electrophoretic coating) are used to further improve the durability and protection performance of the brackets.
Achieve lightweight design
The demand for lightweight in the modern manufacturing industry is increasing, especially in automobiles and electronic equipment. Brackets made of materials such as aluminum alloys and stainless steel can reduce weight while maintaining strength. For example, battery brackets in new energy vehicles need to be both lightweight and strong to extend the range and improve safety performance.
There are many types of metal brackets, which can be divided into the following types according to the material:
● Steel bracket
● Carbon steel bracket
● Stainless steel bracket
● Low alloy steel bracket
● Aluminum alloy bracket
● Titanium alloy bracket
● Copper bracket
● Magnesium alloy bracket
● Zinc alloy bracket
● Composite metal bracket
This type of bracket can adapt to complex application scenarios
Their versatility and high adaptability make them perform well in complex application scenarios. For example, in the field of photovoltaic energy, galvanized brackets can work for a long time in harsh outdoor environments; in industrial equipment, alloy steel brackets need to adapt to high-precision processing and high-strength use requirements.
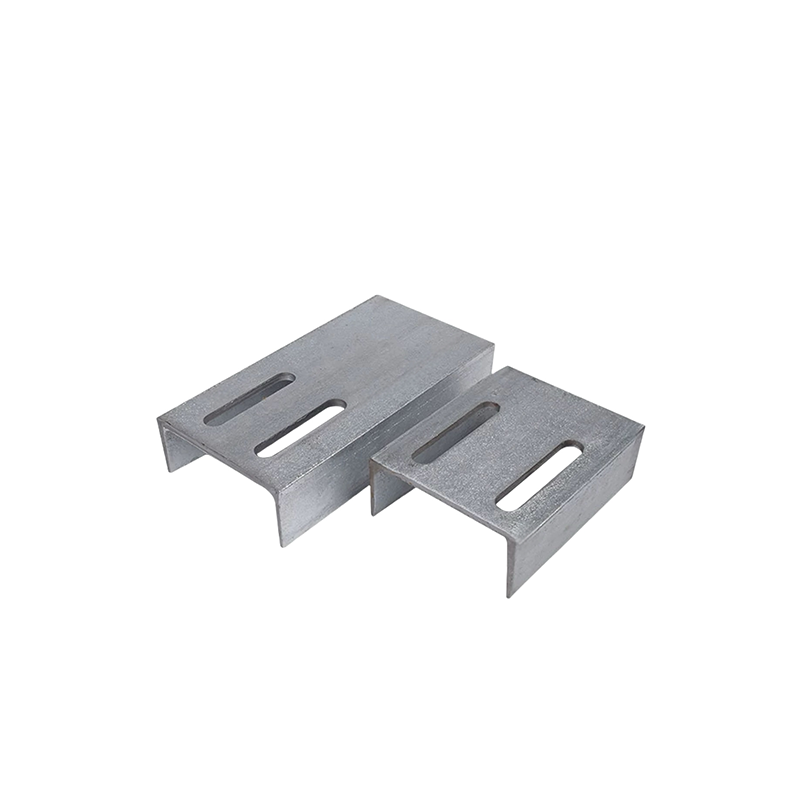
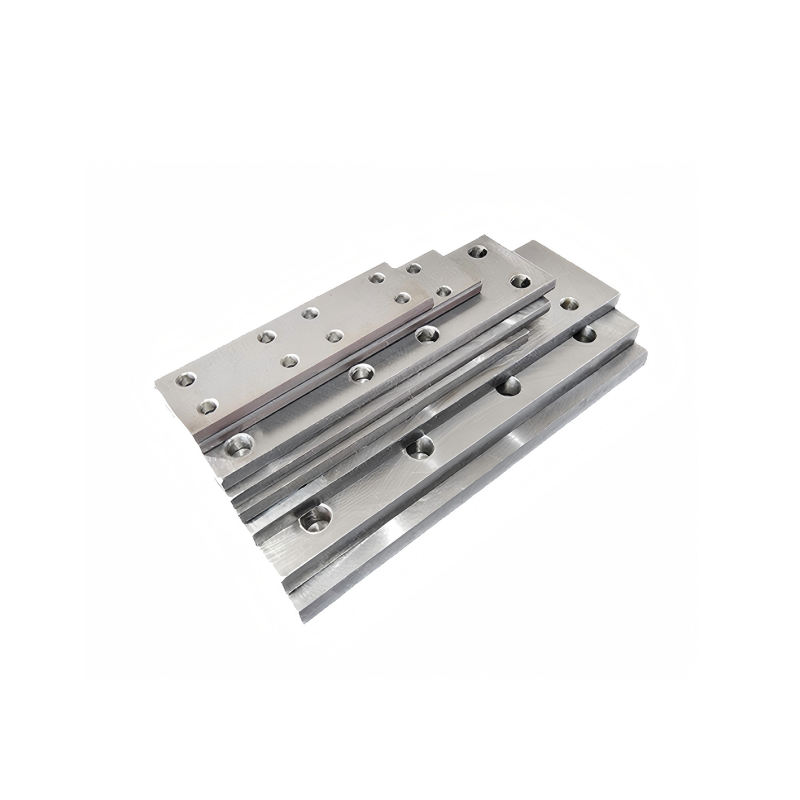
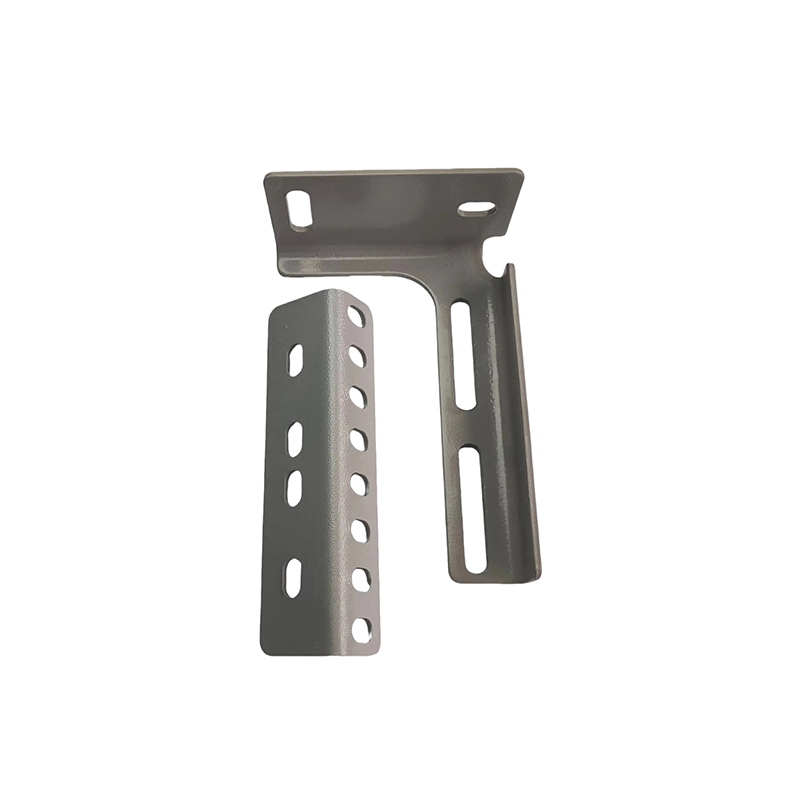
2. Future development trend of metal brackets
Intelligence and automation
With the advancement of Industry 4.0, the design and production of metal brackets are moving towards intelligence. Automated production lines combined with robotic technology can quickly complete processes such as cutting, forming and welding. At the same time, through the Internet of Things technology, real-time monitoring and maintenance prediction of brackets become possible, further improving production efficiency and product quality.
Green manufacturing and environmental protection design
The continuous upgrading of environmental protection regulations has prompted the metal bracket industry to transform to green manufacturing. For example, the use of dry stamping processes and water-based lubricants reduces pollution emissions; the advancement of material recycling and reuse technology is also reducing resource waste. In the future, more environmentally friendly materials and energy-saving processes will be widely used in the manufacture of metal brackets.
Application of high-performance materials
In order to meet the increasingly complex application requirements, advanced materials such as high-strength steel and titanium alloys are becoming an important choice for metal brackets. At the same time, the popularization of hot stamping technology makes the processing of ultra-high-strength materials possible, which is particularly important in the fields of lightweight automobiles and aerospace.
Customization and flexible production
With the increase in personalized needs, the production of metal brackets is shifting from large-scale standardization to small-scale customization. Digital design and rapid mold change technology can quickly respond to customer needs and provide customized bracket solutions. In addition, the flexible production model also improves the response speed of the supply chain and enhances the competitiveness of manufacturers.
Multifunctional integrated design
In the future, metal brackets will not only be limited to supporting functions, but will also assume more multifunctional roles. For example, in industrial equipment, brackets may integrate cable management and heat exchange functions; in photovoltaic systems, brackets may also have angle adjustment and automatic cleaning functions.
3. In general
The role of metal brackets in the manufacturing industry is irreplaceable, from basic structural support to complex functional integration, providing efficient and reliable solutions for all walks of life. With the continuous development of intelligent, green manufacturing and high-performance materials, a variety of metal brackets will show greater potential in the future, injecting new impetus into the upgrading and innovation of the manufacturing industry.
Post time: Dec-12-2024