In any manufacturing or assembly process, but especially in the sheet metal fabrication industry, choosing the right fasteners is critical. There are many types of fasteners on the market, each designed for a specific application and material type, and making the right choice can significantly improve the durability, strength, and appearance of your product. The following guidelines can help you choose the right fasteners for your needs.
Consider Materials and Environment
Different environments and uses have different requirements for fasteners. For example, in outdoor environments, fasteners need to have good corrosion resistance to withstand the erosion of wind, rain, and various chemicals. In high temperature or high pressure environments, fasteners must be able to withstand extreme conditions to ensure the reliability of the connection.
Understand Load and Stress Requirements
The accuracy of size and specifications is also an important factor in selecting fasteners. The load and stress level of the fastener are key factors in the selection process. High-strength bolts or fasteners are essential for heavy-duty applications, while lighter loads may only require standard screws or rivets. Be sure to check the load-bearing specifications when selecting to avoid safety hazards.
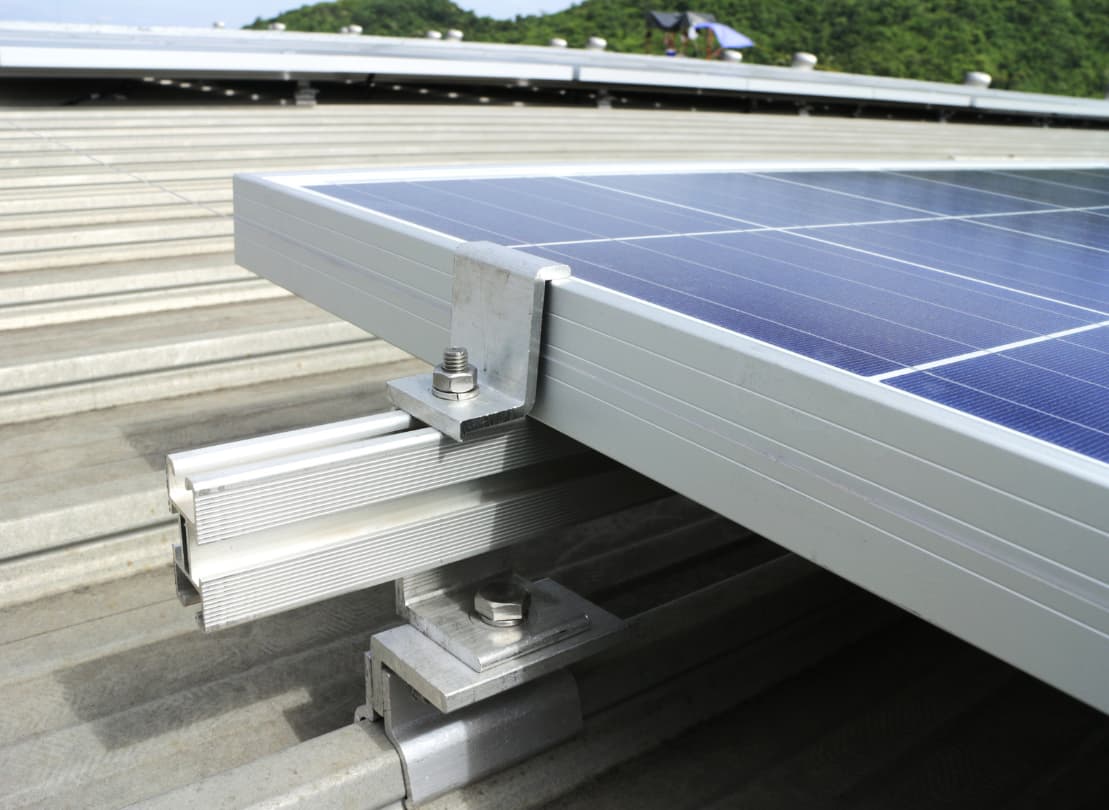
Evaluate fastener types to meet assembly needs
Different types of fasteners can be used for various assembly purposes. For example, DIN 931 hexagonal head half-thread bolts are widely used in machinery manufacturing, construction and other fields; DIN 933 hexagonal head bolts are suitable for applications that require full thread connections; DIN 6921 hexagonal flange bolts have a larger support surface and can provide better tightening effects; DIN 934 hexagonal nuts are used with bolts; DIN 985 nylon lock nuts can prevent loosening; DIN 439 thin hexagonal nuts are suitable for occasions with limited space; DIN 7991 hexagonal countersunk screws have heads that sink into the mounting surface to make the surface look flat; there are also DIN 965 cross recessed pan head screws, DIN 125 flat washers, DIN 9021 large washers, DIN127 spring washers, etc. Bolts and nuts are flexible and reusable, suitable for applications that may require disassembly and maintenance.
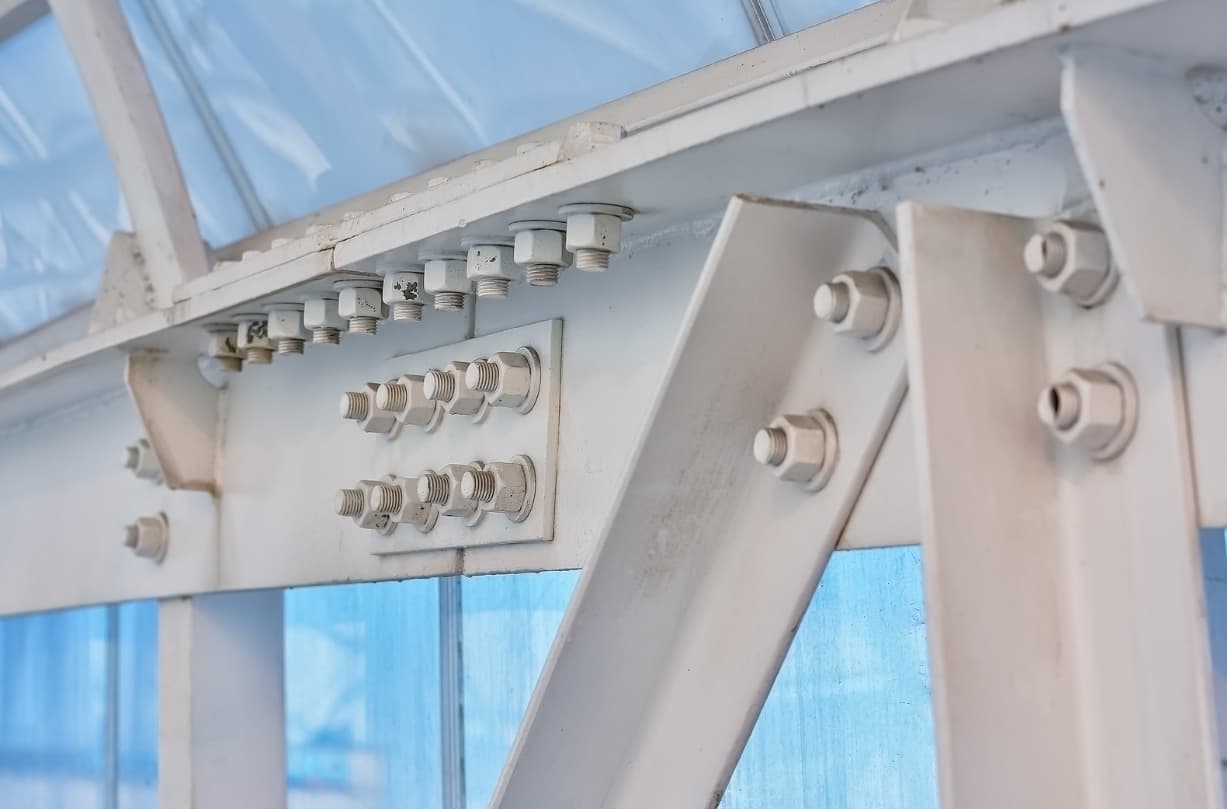
Consider aesthetics and surface treatment
Choosing a surface treatment that complements or matches the material can bring a more refined and professional appearance. Especially for exposed applications, aesthetics and corrosion resistance can be enhanced through a variety of surface treatments, such as zinc, nickel, or anodized coatings.
Consider installation methods and costs
Ease of installation and cost are also important factors. For example, self-tapping screws can simplify the assembly process because they do not require pre-drilling. Automated equipment can be used for rivets and bolts, which can speed up assembly for mass production, but will increase some initial costs.
Make the right choice
Selecting the right fasteners can ensure that the product achieves optimal performance, durability, and appearance. The right fastener selection ultimately helps improve the overall quality and reliability of the finished product, ensuring user satisfaction and long-term cooperation.
Post time: Oct-11-2024