In the field of sheet metal processing, surface treatment not only affects the appearance of the product, but is also directly related to its durability, functionality and market competitiveness. Whether it is applied to industrial equipment, automobile manufacturing, or electronic appliances, high-quality surface treatment processes can significantly improve product quality and added value. The following 10 key tips are designed to help you optimize the process flow of sheet metal surface treatment and help achieve excellent results more efficiently.
Tip 1: Accurate pre-treatment
Before any surface treatment process begins, thorough surface pretreatment is the basis for ensuring the effect of subsequent treatment.
Removing surface oil, oxides and rust is the first task. You can use professional degreasers or rust removers, combined with soaking, spraying or manual wiping.
For stubborn contamination, mechanical grinding (such as sandpaper, grinding wheel, etc.) can be used.
Pay attention when operating: control the force to avoid damaging the substrate surface, especially for thinner sheet metal parts.
Improvement suggestions: Use automated pretreatment equipment (such as spray systems) to ensure processing efficiency and consistency, especially in mass production.
Tip 2: Choose the right coating material
Different usage scenarios have different requirements for the coating materials of sheet metal parts:
Outdoor environment: It is recommended to use a coating with high weather resistance, such as fluorocarbon coating or acrylic coating.
High friction parts: Polyurethane coating or ceramic coating is preferred to increase wear resistance.
At the same time, attention should also be paid to the adhesion of the coating, which can be improved by primer. For special demand scenarios (such as antibacterial or insulating surfaces), functional coatings can be considered.
Tips: The environmental friendliness and low VOC (volatile organic compound) content of coating materials are becoming a market trend, and green and environmentally friendly coatings can be preferred.
Tip 3: Optimize spraying process parameters
Spraying process parameters directly determine the quality and appearance of the coating:
Spray gun distance: It should be kept between 15-25 cm to avoid sagging or coarse particles.
Spraying pressure: It is recommended to be between 0.3-0.6 MPa to ensure uniform atomization of the paint.
Spraying speed and angle: For workpieces with complex shapes, adjust the angle of the spray gun to ensure uniform coating coverage on the edges and grooves.
Improvement suggestions: Conduct sample coating experiments during the process verification phase to optimize parameter settings and ensure stability in large-scale production.
Tip 4: Use electrostatic spraying technology
Electrostatic spraying has become the first choice for modern surface treatment due to its high adhesion rate and uniformity:
The grounding effect is the key to the quality of spraying, and professional grounding equipment should be used to ensure a stable electric field.
Adjust the electrostatic voltage according to the complexity of the sheet metal, generally controlled between 50-80 KV.
For complex workpieces with blind holes or inner cavities, a dual-gun system or manual assisted spraying can be used to avoid weak areas of the coating caused by the electric field shielding effect.
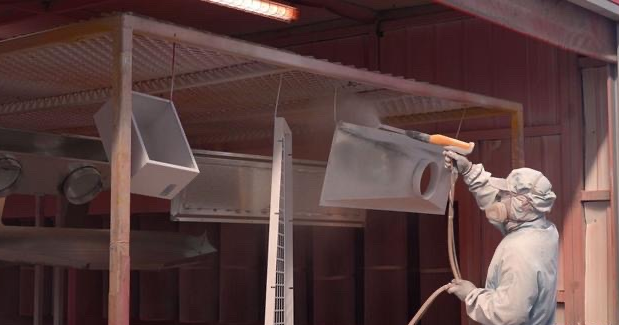
Tip 5: Phosphating treatment enhances anti-corrosion performance
Phosphating treatment can not only improve the corrosion resistance of the substrate, but also enhance the adhesion of subsequent coatings:
Temperature control: The recommended phosphating temperature for steel is between 50-70℃. Too high or too low will affect the uniformity of the phosphating film.
Time setting: Generally 3-10 minutes, adjusted according to material and process requirements.
Upgrade suggestion: Use low-temperature phosphating technology to reduce energy consumption, and combine with environmentally friendly phosphating solution to reduce the pressure of industrial wastewater treatment.
Tip 6: Master the core points of electroplating process
Electroplating can provide excellent decorative and protective properties, but it requires high precision control of the process:
The current density and temperature must be strictly matched. For example, when galvanizing, the temperature should be between 20-30℃ and the current density should be maintained at 2-4 A/dm².
The concentration of additives in the electroplating solution should be monitored regularly to ensure the smoothness and density of the coating.
Note: Cleaning after electroplating is crucial. Residual electroplating solution can cause fogging or corrosion on the surface of the coating.
Tip 7: Anodizing (exclusive for aluminum parts)
Anodizing is the core process to improve the corrosion resistance and decorative effect of aluminum sheet metal parts:
The voltage is recommended to be controlled at 10-20 V, and the processing time is adjusted according to needs (20-60 minutes).
Dyeing and sealing after oxidation are key steps to enhance the antioxidant capacity and color durability.
Advanced technology: Use micro-arc oxidation (MAO) technology to further improve the hardness and wear resistance of the oxide film.
Tip 8: Surface grinding and polishing to improve precision
High-quality surface treatment is inseparable from grinding and polishing:
Sandpaper selection: From coarse to fine, step by step, for example, first use 320#, then transition to 800# or higher mesh.
Consistent operation: The grinding direction must be consistent to avoid cross scratches affecting the appearance.
For workpieces with high gloss requirements, mirror polishing can be used, combined with polishing paste or chromium oxide paste to improve the effect.
Tip 9: Strengthen quality inspection and process control
The stability of surface treatment quality is inseparable from inspection and control:
Coating thickness gauge: detect coating thickness.
Adhesion test: such as cross-cutting or pull-off test, to verify whether the coating is firm.
Salt spray test: to evaluate corrosion resistance.
Improvement suggestions: by introducing automated testing equipment, ensure the efficiency of testing, and combine data analysis for real-time process optimization.
Tip 10: Continuous learning and technological innovation
Surface treatment technology is changing with each passing day, and to maintain technological leadership requires:
Pay attention to industry trends: grasp the latest process trends by participating in exhibitions and seminars.
Technology R&D investment: introduce intelligent equipment and new environmentally friendly materials to improve efficiency and environmental protection level.
For example, emerging technologies such as nano coatings and plasma spraying are gradually being promoted, providing more possibilities for the field of surface treatment.
Post time: Dec-06-2024