ഷീറ്റ് മെറ്റൽ പ്രോസസ്സിംഗ് ഫീൽഡിൽ, ഉപരിതല ചികിത്സ ഉൽപ്പന്നത്തിന്റെ രൂപത്തെ ബാധിക്കുന്നില്ല, പക്ഷേ അതിന്റെ കാലാനുസൃതവും വിപണിയിലെയും മത്സരശേഷിയുമായി നേരിട്ട് ബന്ധപ്പെട്ടിരിക്കുന്നു. ഇത് വ്യാവസായിക ഉപകരണങ്ങളിലേക്കും വാഹന നിർമ്മാണം അല്ലെങ്കിൽ ഇലക്ട്രോണിക് ഉപകരണങ്ങളിലേക്കും പ്രയോഗിച്ചാലും ഉയർന്ന നിലവാരമുള്ള ഉപരിതല ചികിത്സ പ്രക്രിയകൾക്ക് ഉൽപ്പന്ന നിലവാരവും അധിക മൂല്യവും ഗണ്യമായി മെച്ചപ്പെടുത്താൻ കഴിയും. ഷീറ്റ് മെറ്റൽ ഉപരിതല ചികിത്സയുടെ പ്രോസസ്സ് പ്രവാഹം ഒപ്റ്റിമൈസ് ചെയ്യുന്നതിനും മികച്ച ഫലങ്ങൾ കൂടുതൽ കാര്യക്ഷമമായി നേടാൻ സഹായിക്കുന്നതിനും ഇനിപ്പറയുന്ന 10 പ്രധാന ടിപ്പുകൾ രൂപകൽപ്പന ചെയ്തിരിക്കുന്നു.
നുറുങ്ങ് 1: കൃത്യമായ ചികിത്സ
ഏതെങ്കിലും ഉപരിതല ചികിത്സ പ്രക്രിയ ആരംഭിക്കുന്നതിന് മുമ്പ് തുടർന്നുള്ള ചികിത്സയുടെ ഫലം ഉറപ്പാക്കുന്നതിനുള്ള അടിസ്ഥാനമാണ് സമഗ്രമായ ഉപരിതല പ്രീട്രീം.
ഉപരിതല എണ്ണ, ഓക്സൈഡുകൾ, തുരുമ്പ് എന്നിവ നീക്കംചെയ്യുന്നു. കുതിർക്കുന്ന, സ്പ്രേ ചെയ്യുന്ന അല്ലെങ്കിൽ മാനുവൽ തുടയ്ക്കുന്നതുമായി നിങ്ങൾക്ക് പ്രൊഫഷണൽ ഡിക്രീസർമാരുമായുള്ളോ റസ്റ്റ് റിമൂവറുകളോ ഉപയോഗിക്കാം.
ധാർഷ്ട്യമുള്ള മലിനീകരണം, മെക്കാനിക്കൽ പൊടിക്കുന്നത് (സാൻഡ്പേപ്പർ, പൊടിക്കുന്ന ചക്രം മുതലായവ) ഉപയോഗിക്കാം.
പ്രവർത്തിക്കുമ്പോൾ ശ്രദ്ധിക്കുക:സബ്സ്ട്രേറ്റ് ഉപരിതലത്തെ നശിപ്പിക്കുന്നത് ഒഴിവാക്കാൻ ശക്തി നിയന്ത്രിക്കുക, പ്രത്യേകിച്ച് കനംകുറഞ്ഞ ഷീറ്റ് മെറ്റൽ ഭാഗങ്ങൾക്കായി.
മെച്ചപ്പെടുത്തൽ നിർദ്ദേശങ്ങൾ: പ്രോസസ്സിംഗ് കാര്യക്ഷമതയും സ്ഥിരതയും ഉറപ്പാക്കുന്നതിന് യാന്ത്രിക പ്രീട്രീറ്റ്മെന്റ് ഉപകരണങ്ങൾ (സ്പ്രേ സിസ്റ്റങ്ങൾ പോലുള്ളവ ഉപയോഗിക്കുക), പ്രത്യേകിച്ച് കൂട്ട ഉൽപാദനത്തിൽ.
ടിപ്പ് 2: ശരിയായ കോട്ടിംഗ് മെറ്റീരിയൽ തിരഞ്ഞെടുക്കുക
ഷീറ്റ് മെറ്റൽ ഭാഗങ്ങളുടെ കോട്ടിംഗ് മെറ്റീരിയലുകൾക്കായി വ്യത്യസ്ത ഉപയോഗ സാഹചര്യങ്ങൾ ഉണ്ട്:
Do ട്ട്ഡോർ പരിസ്ഥിതി: ഫ്ലൂറോകാർബൺ കോട്ടിംഗ് അല്ലെങ്കിൽ അക്രിലിക് കോട്ടിംഗ് പോലുള്ള ഉയർന്ന കാലാവസ്ഥാ പ്രതിരോധം ഉപയോഗിക്കാൻ ശുപാർശ ചെയ്യാൻ ശുപാർശ ചെയ്യുന്നു.
ഉയർന്ന ഘർക്ക് ഭാഗങ്ങൾ: പോളിയുറീൻ കോട്ടിംഗ് അല്ലെങ്കിൽ സെറാമിക് കോട്ടിംഗ് വള്ളത്തെ പ്രതിരോധം വർദ്ധിപ്പിക്കുന്നതിനാണ്.
അതേസമയം, പ്രൈമർ മെച്ചപ്പെടുത്താൻ കഴിയുന്ന കോട്ടിംഗിന്റെ പഷീഷനും ശ്രദ്ധ നൽകണം. പ്രത്യേക ഡിമാൻഡ് സാഹചര്യങ്ങൾക്കായി (ആൻറി ബാക്ടീരിയൽ അല്ലെങ്കിൽ ഇൻസുലേറ്റിംഗ് സർഫേസ് പോലുള്ളവ) ഫംഗ്ഷണൽ കോട്ടിംഗുകൾ പരിഗണിക്കാം.
നുറുങ്ങുകൾ:പരിസ്ഥിതി സൗഹൃദവും കുറഞ്ഞ വോക്കും (അസ്ഥിരമായ ഓർഗാനിക് കോമ്പൗണ്ട്) ഉള്ളടക്കം കോട്ടിംഗ് മെറ്റീരിയലുകളുടെ ഉള്ളടക്കം ഒരു വിപണി പ്രവണതയായി മാറുകയാണ്, പച്ചയും പരിസ്ഥിതിക്കും സൗഹൃദ കോട്ടിംഗുകൾ തിരഞ്ഞെടുക്കാം.
ടിപ്പ് 3: സ്പ്രേചെയ്യുന്ന പ്രോസസ്സ് പാരാമീറ്ററുകൾ ഒപ്റ്റിമൈസ് ചെയ്യുക
പ്രോസസ്സ് പ്രോസസ്സ് പാരാമീറ്ററുകൾ കോട്ടിംഗിന്റെ ഗുണനിലവാരവും രൂപവും നിർണ്ണയിക്കുന്നു:
തോക്ക് ദൂരം സ്പ്രേ: വ്രണപ്പെടുത്താതിരിക്കാൻ 15-25 സെന്റിമീറ്റർ വരെ സൂക്ഷിക്കണം.
സ്പ്രേഫിക്കേഷൻ സമ്മർദ്ദം: പെയിന്റിന്റെ ഏകീകൃത ആകാശം ഉറപ്പാക്കുന്നതിന് 0.3-0.6 എംപിഎ ഇടയിലായി.
വേഗതയും ആംഗിളും സ്പ്രേചെയ്യുന്നത്: സങ്കീർണ്ണമായ ആകൃതികളുള്ള വർക്ക്പീസുകൾക്ക്, അരികുകളിൽ ഏകീകൃത കവറേജ് ഉറപ്പാക്കുന്നതിന് സ്പ്രേ തോക്കിന്റെ കോണിലൂടെ ക്രമീകരിക്കുക.
മെച്ചപ്പെടുത്തൽ നിർദ്ദേശങ്ങൾ:പാരാമീറ്റർ ക്രമീകരണങ്ങൾ ഒപ്റ്റിമൈസ് ചെയ്യുന്നതിന് പ്രോസസ്സ് പരിശോധന ഘട്ടത്തിൽ സാമ്പിൾ കോട്ടിംഗ് പരീക്ഷണങ്ങൾ നടത്തുക, കൂടാതെ വലിയ തോതിലുള്ള ഉൽപാദനത്തിൽ സ്ഥിരത ഉറപ്പാക്കുക.
ടിപ്പ് 4: ഇലക്ട്രോസ്റ്റാറ്റിക് സ്പ്രേംഗ് ടെക്നോളജി ഉപയോഗിക്കുക
ഉയർന്ന പശ നിരക്കും ഏകതയും കാരണം ആധുനിക ഉപരിതല ചികിത്സയുടെ ആദ്യ തിരഞ്ഞെടുപ്പായി ഇലക്ട്രോസ്റ്റാറ്റിക് സ്പ്രേ മാറിയിരിക്കുന്നു:
സ്പ്രേയുടെ ഗുണനിലവാരത്തിന്റെ താക്കോലാണ് ഗ്രൗണ്ടിംഗ് ഇഫക്റ്റ്, സ്ഥിരതയുള്ള ഇലക്ട്രിക് ഫീൽഡ് ഉറപ്പാക്കാൻ പ്രൊഫഷണൽ ഗ്രൗണ്ടിംഗ് ഉപകരണങ്ങൾ ഉപയോഗിക്കണം.
ഷീറ്റ് ലോഹത്തിന്റെ സങ്കീർണ്ണത അനുസരിച്ച് ഇലക്ട്രോസ്റ്റാറ്റിക് വോൾട്ടേജ് ക്രമീകരിക്കുക, സാധാരണയായി 50-80 കെ.വി.
ബ്ലൈൻഡ് ഹോമുകളോ ആന്തരിക അറകളോ ഉള്ള സങ്കീർണ്ണ ജോലികൾക്കോ അല്ലെങ്കിൽ ഒരു ഡ്യുവൽ ഗൺ സിസ്റ്റം അല്ലെങ്കിൽ മാനുവൽ അസിസ്റ്റഡ് സ്പ്രേകൾ വൈദ്യുത ഫീൽഡ് ഷീൽഡിംഗ് പ്രഭാവം ഒഴിവാക്കാൻ ഉപയോഗിക്കാം.
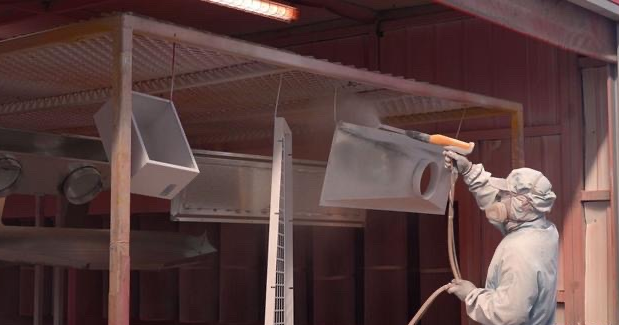
ടിപ്പ് 5: ഫോസ്ഫേറ്റിംഗ് ചികിത്സ ആന്റി-നായക പ്രകടനം വർദ്ധിപ്പിക്കുന്നു
ഫോസ്ഫേറ്റിംഗ് ചികിത്സയ്ക്ക് കെ.ഇ.
താപനില നിയന്ത്രണം: സ്റ്റീലിനായി ശുപാർശ ചെയ്യുന്ന ഫോസ്ഫേറ്റിംഗ് താപനില 50-70 ℃. വളരെ ഉയർന്ന അല്ലെങ്കിൽ വളരെ കുറവ് ഫോസ്ഫേറ്റിംഗ് സിനിമയുടെ ഏകതയെ ബാധിക്കും.
സമയ ക്രമീകരണം: സാധാരണയായി 3-10 മിനിറ്റ്, മെറ്റീരിയലിനനുസരിച്ച് ക്രമീകരിച്ചു.
അപ്ഗ്രേഡുചെയ്യുക നിർദ്ദേശം: energy ർജ്ജ ഉപഭോഗം കുറയ്ക്കുന്നതിന് ആവശ്യമായ താപനില ഫോസ്ഫെറ്റിംഗ് സാങ്കേതികവിദ്യ ഉപയോഗിക്കുക, ഒപ്പം വ്യാവസായിക മലിനജല ചികിത്സയുടെ സമ്മർദ്ദം കുറയ്ക്കുന്നതിന് പരിസ്ഥിതി സൗഹൃദ ഫോസ്ഫേറ്റിംഗ് പരിഹാരവുമായി ഉപയോഗിക്കുക.
ടിപ്പ് 6: ഇലക്ട്രോപ്പേഷൻ പ്രക്രിയയുടെ പ്രധാന പോയിന്റുകൾ മാസ്റ്റർ ചെയ്യുക
ഇലക്ട്രോപ്പിംഗിന് മികച്ച അലങ്കാരവും സംരക്ഷണവുമായ സ്വത്തുക്കൾ നൽകാൻ കഴിയും, പക്ഷേ ഇതിന് പ്രക്രിയയുടെ ഉയർന്ന കൃത്യത നിയന്ത്രണം ആവശ്യമാണ്:
നിലവിലെ സാന്ദ്രതയും താപനില കർശനമായി പൊരുത്തപ്പെടണം. ഉദാഹരണത്തിന്, ഗാൽവാനിംഗ് ചെയ്യുമ്പോൾ, താപനില 20-30 നും നിലവിലെ സാന്ദ്രത 2-4 എ / ഡിഎംസിയിൽ നിലനിർത്തണം.
കോട്ടിംഗിന്റെ സുഗമതയും സാന്ദ്രതയും ഉറപ്പാക്കുന്നതിന് ഇലക്ട്രോപിടിപ്പിക്കുന്നതിലെ അഡിറ്റീവുകളുടെ സാന്ദ്രത പതിവായി നിരീക്ഷിക്കണം.
കുറിപ്പ്: ഇലക്ട്രോപ്പിൾ നിർണായകമാണെന്ന് വൃത്തിയാക്കൽ. കോട്ടിംഗിന്റെ ഉപരിതലത്തിൽ അവശേഷിക്കുന്ന ഇലക്ട്രോപിടിപ്പിക്കൽ പരിഹാരം മൂടൽമഞ്ഞ് അല്ലെങ്കിൽ നാശത്തെ സൃഷ്ടിക്കും.
ടിപ്പ് 7: അനോഡൈസിംഗ് (അലുമിനിയം ഭാഗങ്ങൾക്കായി എക്സ്ക്ലൂസീവ്
അലുമിനിയം ഷീറ്റ് മെറ്റൽ ഭാഗങ്ങളുടെയും അലങ്കാര പ്രഭാവവും മെച്ചപ്പെടുത്തുന്നതിനുള്ള കോർ പ്രക്രിയയാണ് അനോഡെസിംഗ്: അലുമിനിയം ഷീറ്റ് മെറ്റൽ ഭാഗങ്ങളുടെ അലങ്കാര പ്രഭാവം:
വോൾട്ടേജ് 10-20 v ൽ നിയന്ത്രിക്കാൻ ശുപാർശ ചെയ്യുന്നു, ആവശ്യങ്ങൾ അനുസരിച്ച് പ്രോസസ്സിംഗ് സമയം (20-60 മിനിറ്റ്) ക്രമീകരിക്കുന്നു.
ഓക്സീകരണത്തിന് ശേഷം ഡൈയിംഗും സീലിംഗും സിക്സിഡേഷൻ ആന്റിഓക്സിഡന്റ് ശേഷിയും വർണ്ണ കാലവും വർദ്ധിപ്പിക്കുന്നതിനുള്ള പ്രധാന നടപടികളാണ്.
നൂതന സാങ്കേതികവിദ്യ: കാഠിന്യം കൂടുതൽ മെച്ചപ്പെടുത്തുന്നതിനും ഓക്സൈഡ് ഫിലിമിന്റെ പ്രതിരോധം ധരിക്കുന്നതിനും മൈക്രോ ആർക്ക് ഓക്സിഡേഷൻ (മാവോ) സാങ്കേതികവിദ്യ ഉപയോഗിക്കുക.
ടിപ്പ് 8: കൃത്യത മെച്ചപ്പെടുത്തുന്നതിന് ഉപരിതലം പൊടിക്കുകയും മിനുക്കുകയും ചെയ്യുന്നു
ഉയർന്ന നിലവാരമുള്ള ഉപരിതല ചികിത്സ പൊടിക്കുന്നതിലും മിനുക്കുന്നതിലും നിഷ്ക്രിയമാണ്:
സാൻഡ്പേപ്പർ തിരഞ്ഞെടുക്കൽ: നാടൻ മുതൽ പിഴ വരെ, ഘട്ടം ഘട്ടമായി, ആദ്യം 320 #, തുടർന്ന് 800 # അല്ലെങ്കിൽ ഉയർന്ന മെഷ് ആയി ഉപയോഗിക്കുക.
സ്ഥിരമായ പ്രവർത്തനം: കാഴ്ചയെ ബാധിക്കുന്ന ക്രോസ് പോറലുകൾ ഒഴിവാക്കാൻ ഗ്രൈൻഡിംഗ് ദിശ സ്ഥിരത പുലർത്തണം.
ഉയർന്ന ഗ്ലോസ് ആവശ്യകതകളുള്ള വർക്ക്പീസുകൾക്ക്, ഇഫക്ട് മെച്ചപ്പെടുത്തുന്നതിന് മിനുസപ്പുള്ള പേസ്റ്റ് അല്ലെങ്കിൽ ക്രോമിയം ഓക്സൈഡ് പേസ്റ്റ് ഉപയോഗിച്ച് സംയോജിപ്പിച്ച് മിറർ പോളിഷിംഗ് ഉപയോഗിക്കാം.
നുറുങ്ങ് 9: ഗുണനിലവാരമുള്ള പരിശോധനയും പ്രോസസ്സ് നിയന്ത്രണവും ശക്തിപ്പെടുത്തുക
ഉപരിതല ചികിത്സാ ഗുണനിലവാരത്തിന്റെ സ്ഥിരത പരിശോധനയിലും നിയന്ത്രണത്തിലും അഭേദ്യമാണ്:
കോട്ടിംഗ് കനം ഗേജ്: കോട്ടിംഗ് കനം കണ്ടെത്തുക.
കോട്ടിംഗ് ഉറച്ചതാണോ എന്ന് പരിശോധിക്കുന്നതിനായി ക്രോസ് കട്ട് അല്ലെങ്കിൽ പുൾ-ഓഫ് ടെസ്റ്റ് പോലുള്ള ക്രോസ് കട്ട്-ഓഫ് ടെസ്റ്റ്.
സാൾട്ട് സ്പ്രേ ടെസ്റ്റ്: നാരങ്ങ പ്രതിരോധം വിലയിരുത്തുന്നതിന്.
മെച്ചപ്പെടുത്തൽ നിർദ്ദേശങ്ങൾ: ഓട്ടോമേറ്റഡ് ടെസ്റ്റിംഗ് ഉപകരണങ്ങൾ അവതരിപ്പിക്കുന്നതിലൂടെ, പരിശോധനയുടെ കാര്യക്ഷമത ഉറപ്പാക്കുക, തത്സമയ പ്രോസസ്സ് ഒപ്റ്റിമൈസേഷനായി ഡാറ്റ വിശകലനം സംയോജിപ്പിക്കുക.
ടിപ്പ് 10: തുടർച്ചയായ പഠനവും സാങ്കേതികവുമായ പുതുമ
ഉപരിതല ചികിത്സാ സാങ്കേതികവിദ്യ കടന്നുപോകുന്ന ഓരോ ദിവസവും മാറുകയാണ്, സാങ്കേതിക നേതൃത്വം നിലനിർത്തുന്നതിന്:
വ്യവസായ ട്രെൻഡുകൾ ശ്രദ്ധിക്കുക: എക്സിബിഷനുകളിലും സെമിനാറുകളിലും പങ്കെടുക്കുന്നതിലൂടെ ഏറ്റവും പുതിയ പ്രോസസ്സ് ട്രെൻഡുകൾ മനസ്സിലാക്കുക.
സാങ്കേതികവിദ്യ ആർ & ഡി നിക്ഷേപം: കാര്യക്ഷമതയും പരിസ്ഥിതി സംരക്ഷണ നിലയും മെച്ചപ്പെടുത്തുന്നതിന് ഇന്റലിജന്റ് ഉപകരണങ്ങളും പുതിയ പരിസ്ഥിതി സൗഹൃദ വസ്തുക്കളും അവതരിപ്പിക്കുക.
ഉദാഹരണത്തിന്, നാനോ കോട്ടിംഗുകളും പ്ലാസ്മ സ്പ്രേയും പോലുള്ള വളർന്നുവരുന്ന സാങ്കേതികവിദ്യകൾ ക്രമേണ പ്രോത്സാഹിപ്പിക്കുന്നു, ഉപരിതല ചികിത്സയുടെ മേഖലയ്ക്ക് കൂടുതൽ സാധ്യതകൾ നൽകുന്നു.
പോസ്റ്റ് സമയം: ഡിസംബർ -06-2024