L-shaped headlight mounting bracket galvanized
● Material parameters: stainless steel, carbon steel, aluminum alloy
● Processing technology: cutting, stamping
● Surface treatment: spraying, electrophoresis, powder coating
● Connection method: welding, bolt connection, riveting
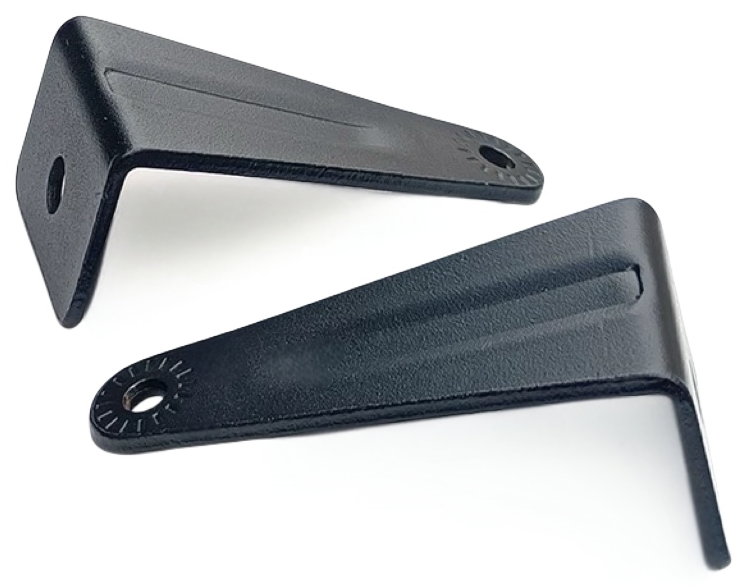
Function and Purpose of Headlight Bracket
Stable installation to ensure driving safety
The main function of the headlight bracket is to provide a stable installation position for the headlight. During the driving process, whether it is a bumpy road or strong wind resistance at high speed, the headlight brackets can ensure that the headlight is stable and does not move, thereby ensuring the normal operation of the headlight and the precise direction of light illumination.
For example, on a rugged mountain road, severe vibrations may cause loose parts that are not firmly installed, and high-quality headlight brackets can effectively absorb vibrations, maintain the stability of the headlights, and improve driving safety.
Flexible adjustment to optimize lighting effects
Some headlight mounting bracket have an adjustment function, which can easily adjust the up and down, left and right angles of the headlights to optimize the lighting range. This function is particularly important, providing the driver with a clear view of the road while avoiding glare interference to other drivers.
For example, when the trunk of the vehicle is loaded with heavy objects and the vehicle body is tilted, the headlight angle can be quickly adjusted through the adjustment screws on the bracket to ensure that the light always covers an appropriate range, improving the comfort and safety of night driving.
What are the common surface treatment processes for headlight mounting brackets?
In order to improve the durability and aesthetics of headlight brackets, different surface treatment processes are widely used in the manufacturing process. The following are several common treatment methods and their characteristics:
1. Galvanizing
Process principle
Galvanizing is to cover the surface of the bracket with a layer of zinc through electroplating or hot-dip plating. The electroplating method uses the principle of electrolysis to deposit the zinc layer, while hot-dip plating immerses the bracket in molten zinc liquid to make the zinc layer firmly adhere.
Features and advantages
Excellent anti-corrosion performance: The zinc layer forms a dense oxide film in the air, which effectively prevents the erosion of air and moisture, and can maintain stable performance even in a humid environment.
Bright appearance: The silver-white zinc layer not only protects the bracket, but also gives it a simple and beautiful decorative effect.
Typical application
Widely used in headlight mounting brackets of ordinary models, especially vehicles that need to take into account both anti-corrosion ability and cost control.
2. Chrome plating
Process principle
A layer of chromium is deposited on the surface of the bracket through an electroplating process. The process is carried out in an electrolyte containing chromic anhydride, and the chromium ions are reduced by electric current to form a high-hardness chrome plating layer.
Features and advantages
High hardness and wear resistance: It can resist tool friction and external vibration during installation and adjustment, and is not easy to scratch.
Mirror gloss: The surface is as bright as a mirror, which enhances the texture and refinement of the overall vehicle.
Corrosion resistance: It effectively prevents the bracket from rusting and prolongs its service life.
Typical applications
Applicable to high-end models such as luxury cars and sports cars, meeting vehicles with high requirements for both appearance and performance.
3. Painting treatment
Process principle
After the paint is evenly sprayed on the surface of the bracket, it is dried and cured to form a paint film. There are various types of paint, including epoxy paint, polyurethane paint, etc.
Features and advantages
Customized appearance: The paint color can be adjusted according to the vehicle theme or body color to achieve personalized design.
Anti-corrosion protection: The paint layer isolates air and moisture from contacting the bracket, reducing the risk of corrosion.
Typical applications
Mostly used in customized or concept models, especially vehicles that require specific color matching.
4. Powder coating
Process principle
The powder coating is adsorbed on the surface of the bracket by electrostatic spraying technology, and the coating is formed after high-temperature baking and curing.
Features and advantages
Excellent environmental performance: low VOC emissions, in line with modern environmental standards.
The coating is strong and durable: strong adhesion, wear resistance, impact resistance, and not easy to fall off.
Diverse choices: meet a variety of design needs through coatings of different colors or effects.
Typical applications
Suitable for vehicle manufacturers that require environmental protection and high-performance coatings.
Quality Management
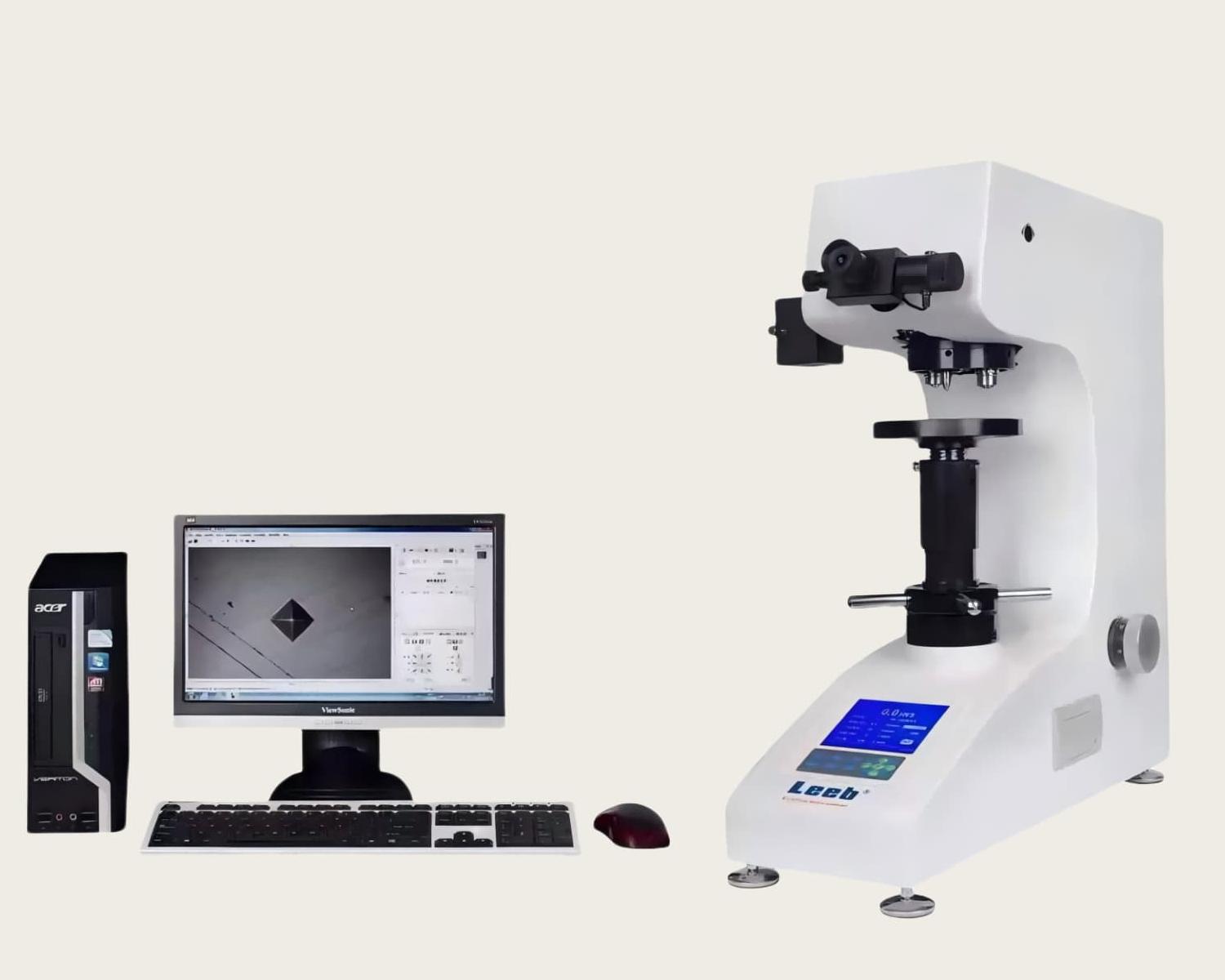
Vickers Hardness Instrument
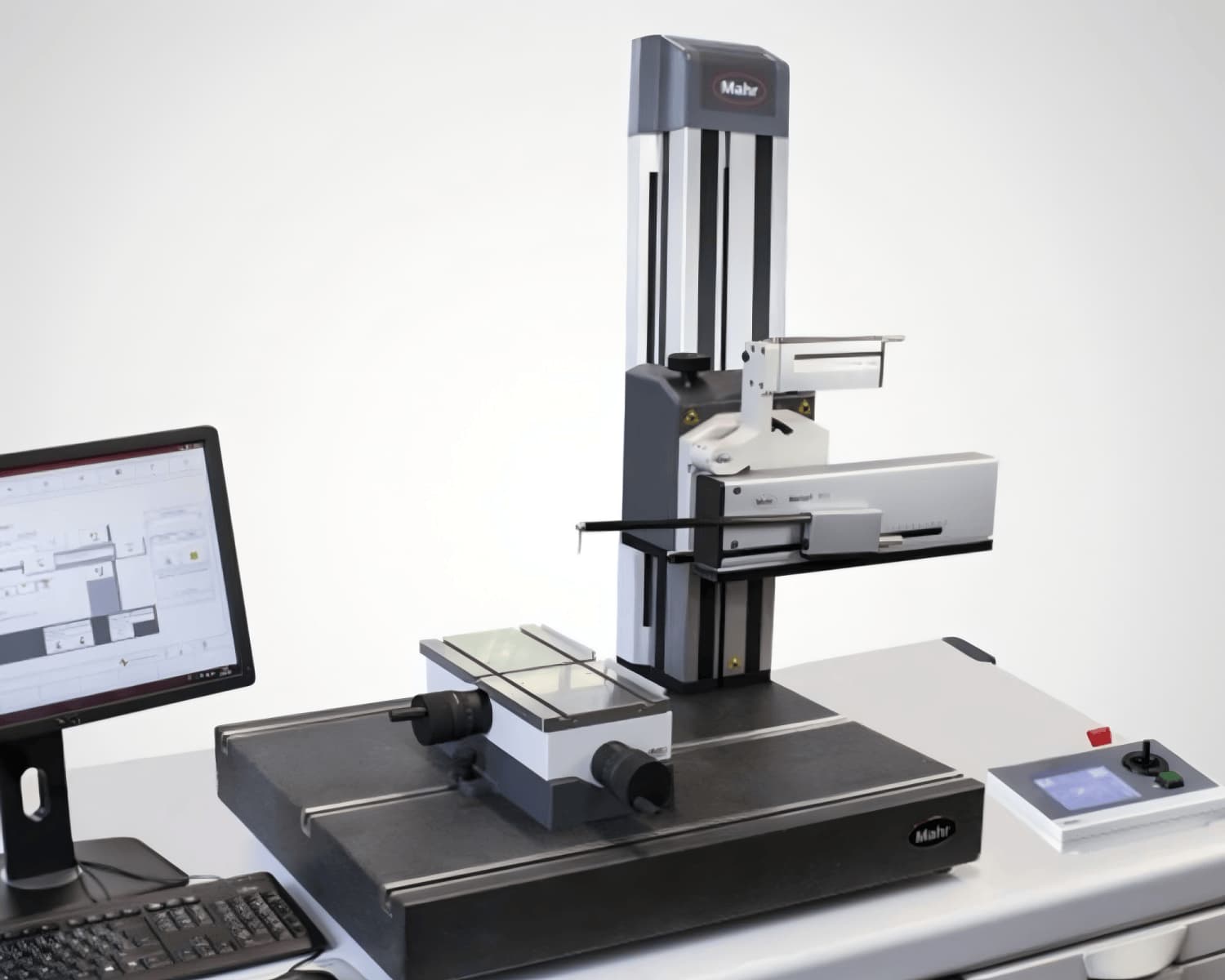
Profile Measuring Instrument
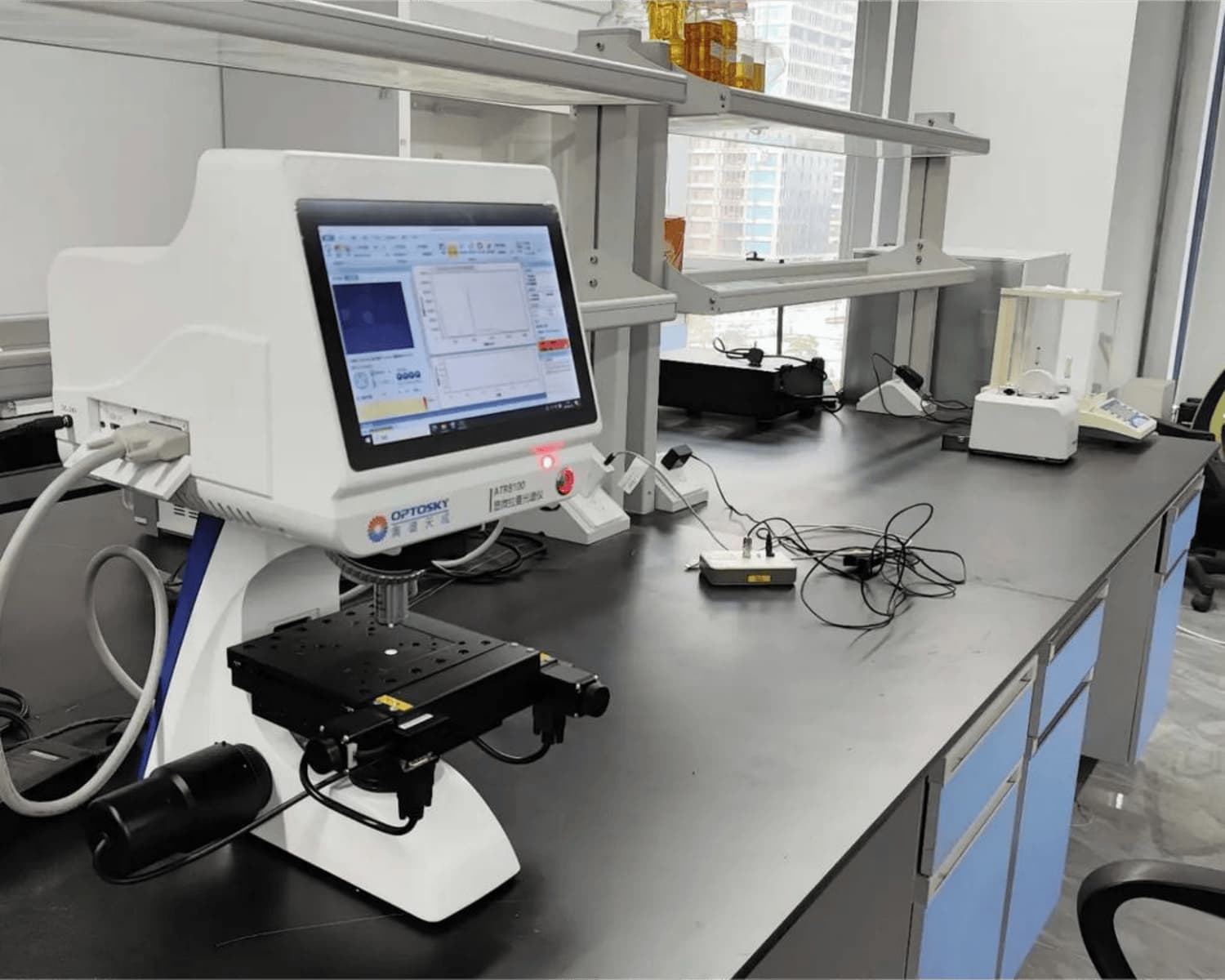
Spectrograph Instrument
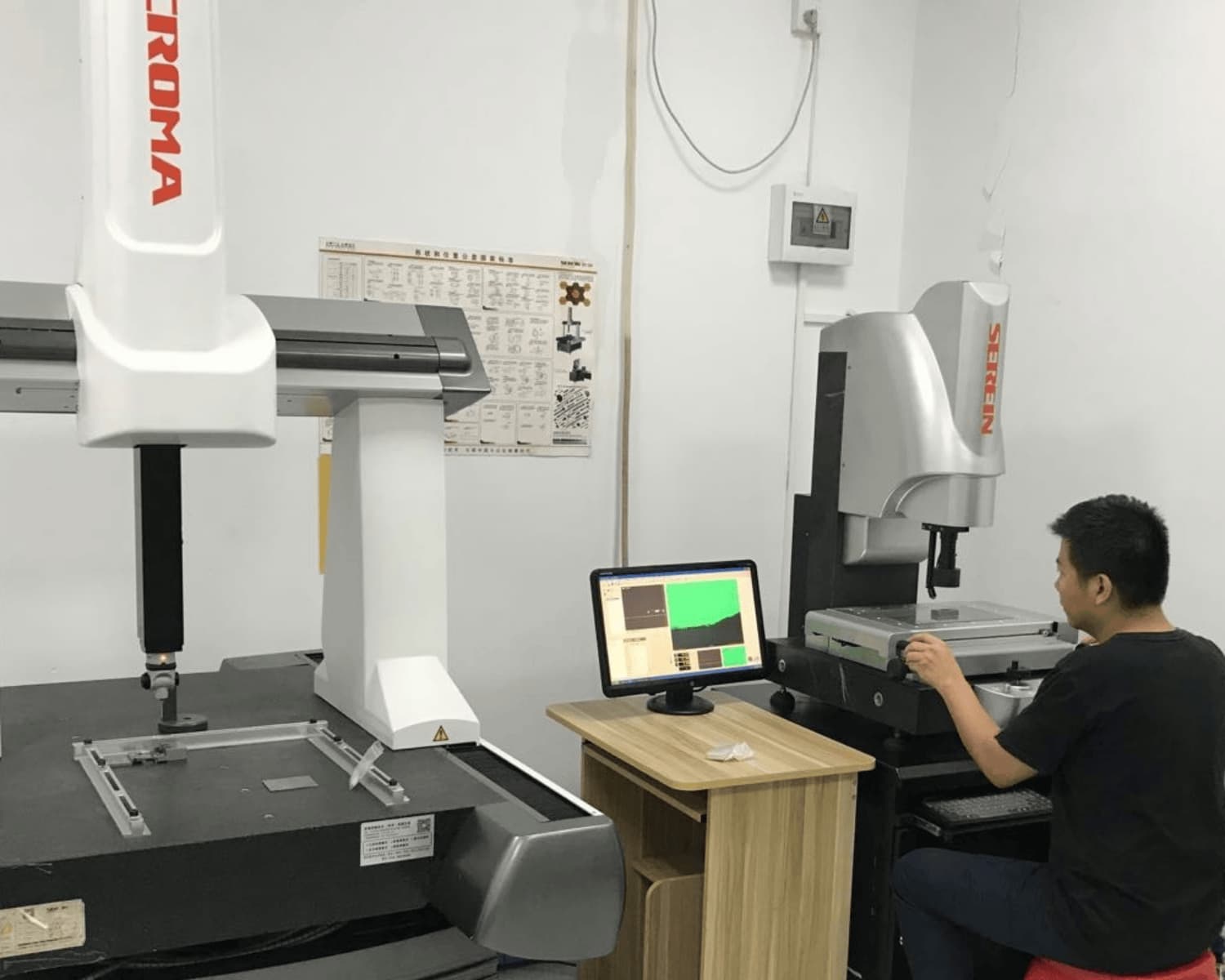
Three Coordinate Instrument
Company Profile
Xinzhe Metal Products Co., Ltd. was established in 2016 and focuses on the production of high-quality metal brackets and components, which are widely used in the construction, elevator, bridge, power, automotive parts and other industries.
The main products include steel building brackets, brackets galvanized, fixed brackets, u shaped metal bracket, angle steel brackets, galvanized embedded base plates, elevator brackets, turbo mounting bracket and fasteners, etc., which can meet the diverse project needs of various industries.
The company uses cutting-edge laser cutting equipment, combined with bending, welding, stamping, surface treatment and other production processes to ensure the accuracy and service life of the products.
Being an ISO 9001-certified business, we collaborate closely with numerous foreign producers of construction, elevator, and machinery to offer them the most affordable, tailored solutions.
We are dedicated to offering top-notch metal processing services to the worldwide market and continuously work to raise the caliber of our goods and services, all while upholding the idea that our bracket solutions should be used everywhere.
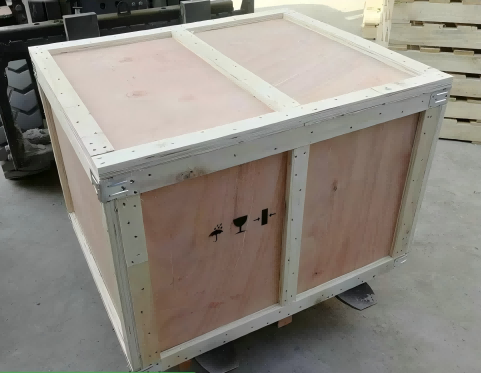
Wooden Box
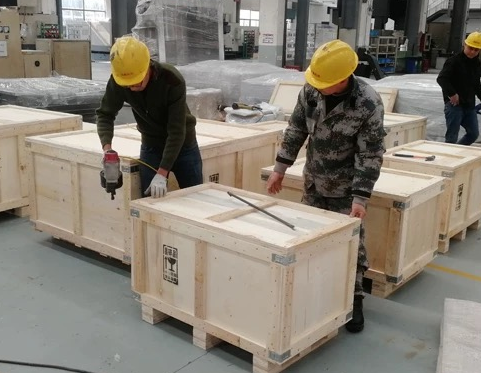
Packing
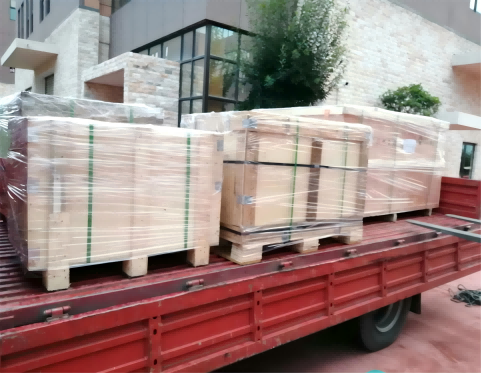
Loading
Packaging and Delivery
How to fix headlight bracket?
1. Diagnose the Problem
● Inspect for cracks, loose hardware, or misalignment.
● Ensure all screws, bolts, or clips are intact.
2. Gather Tools and Materials
● Screwdrivers, wrench set, adhesive/epoxy, and replacement parts if needed.
● Use zip ties or temporary supports for quick fixes.
3. Fix Common Issues
● Loose Bracket: Tighten screws/bolts or replace missing hardware.
● Cracked Bracket: Clean the area, apply epoxy, and reinforce
temporarily if necessary.
● Broken Bracket: Replace with a new one, ensuring proper alignment.
4. Adjust Alignment
● Park 25 feet from a wall and turn on headlights.
● Use adjustment screws to align the beam as per the vehicle’s manual.
5. Test the Repair
● Ensure the bracket and headlight are secure.
● Check for proper illumination and stability.
Pro Tips
● Use genuine parts for durability.
● Regularly inspect brackets during maintenance to prevent future issues.
This streamlined guide helps you quickly fix and secure your headlight bracket!
Multiple Transportation Options
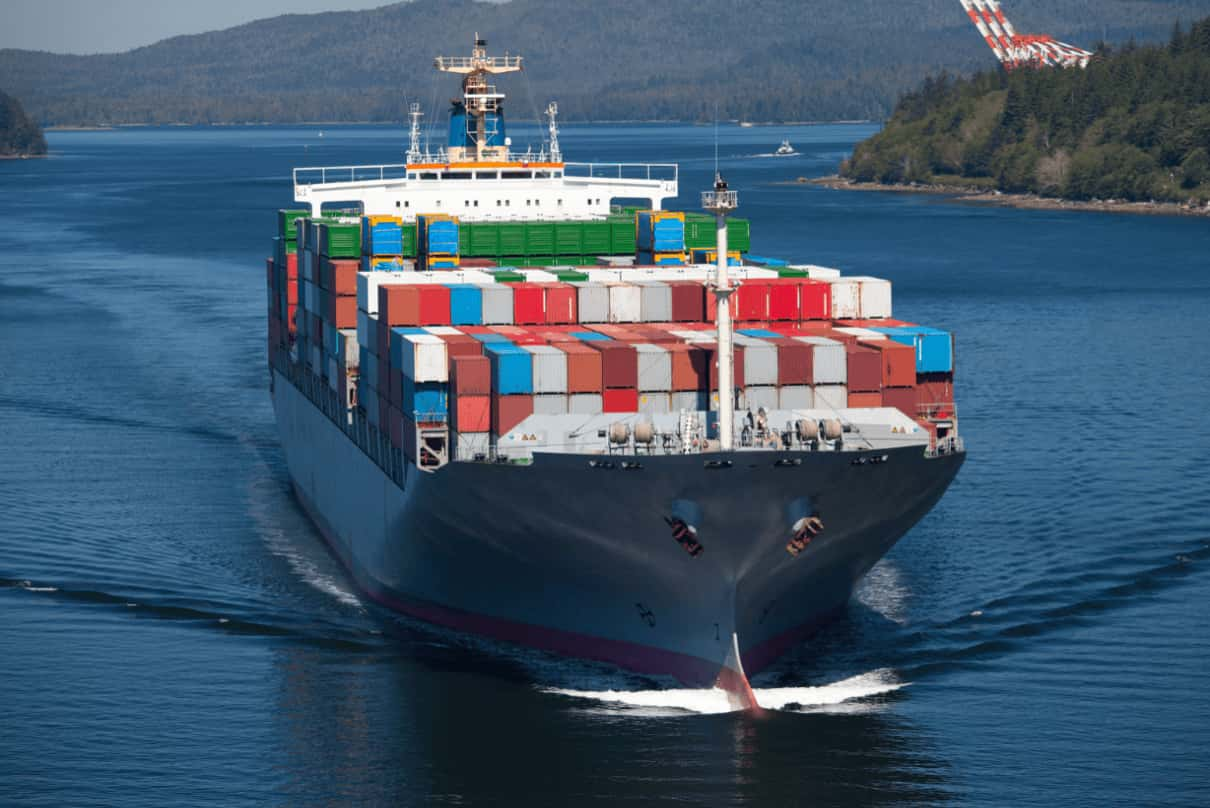
Ocean Freight
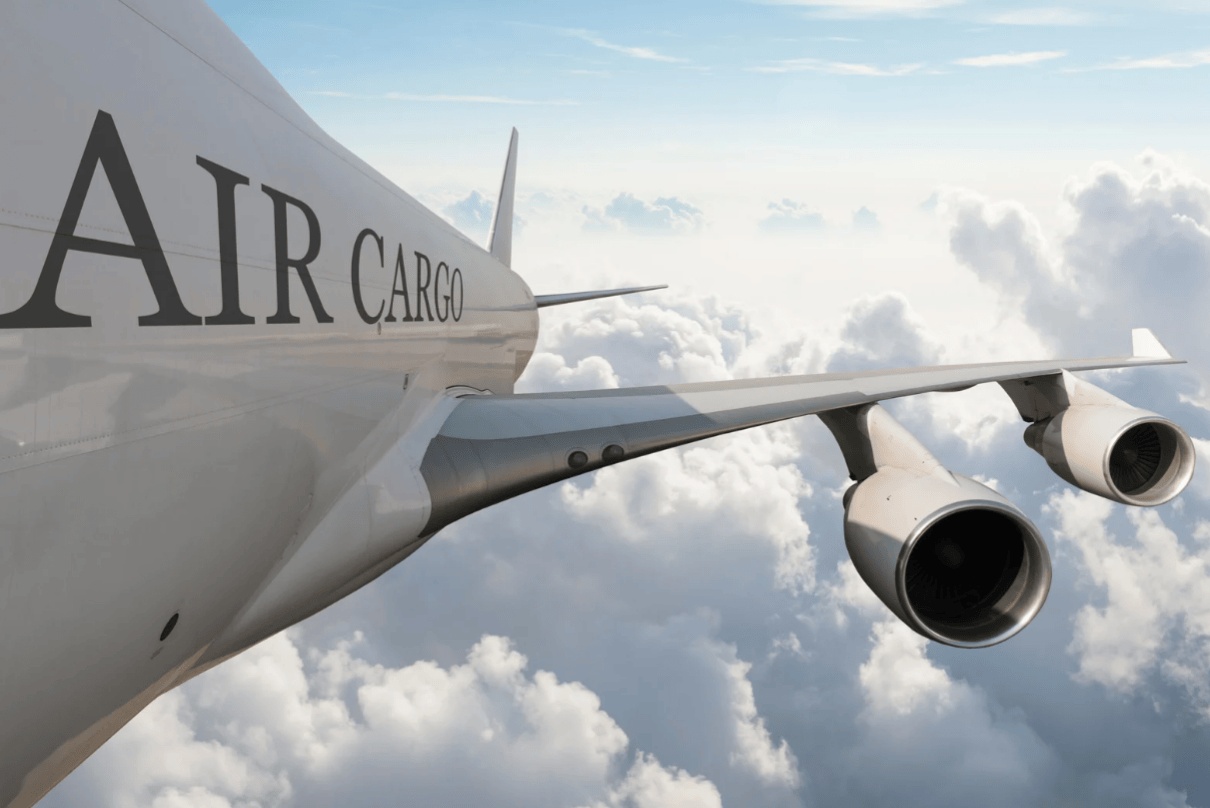
Air Freight
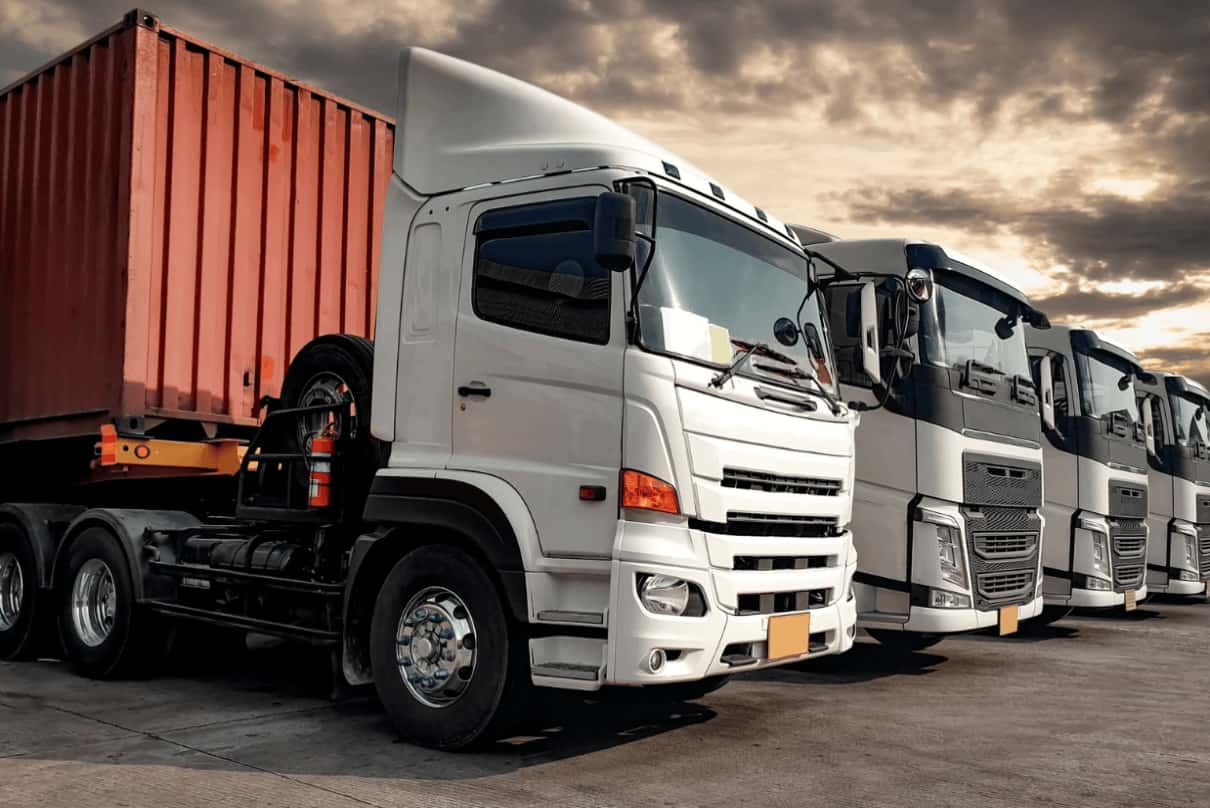
Road Transportation
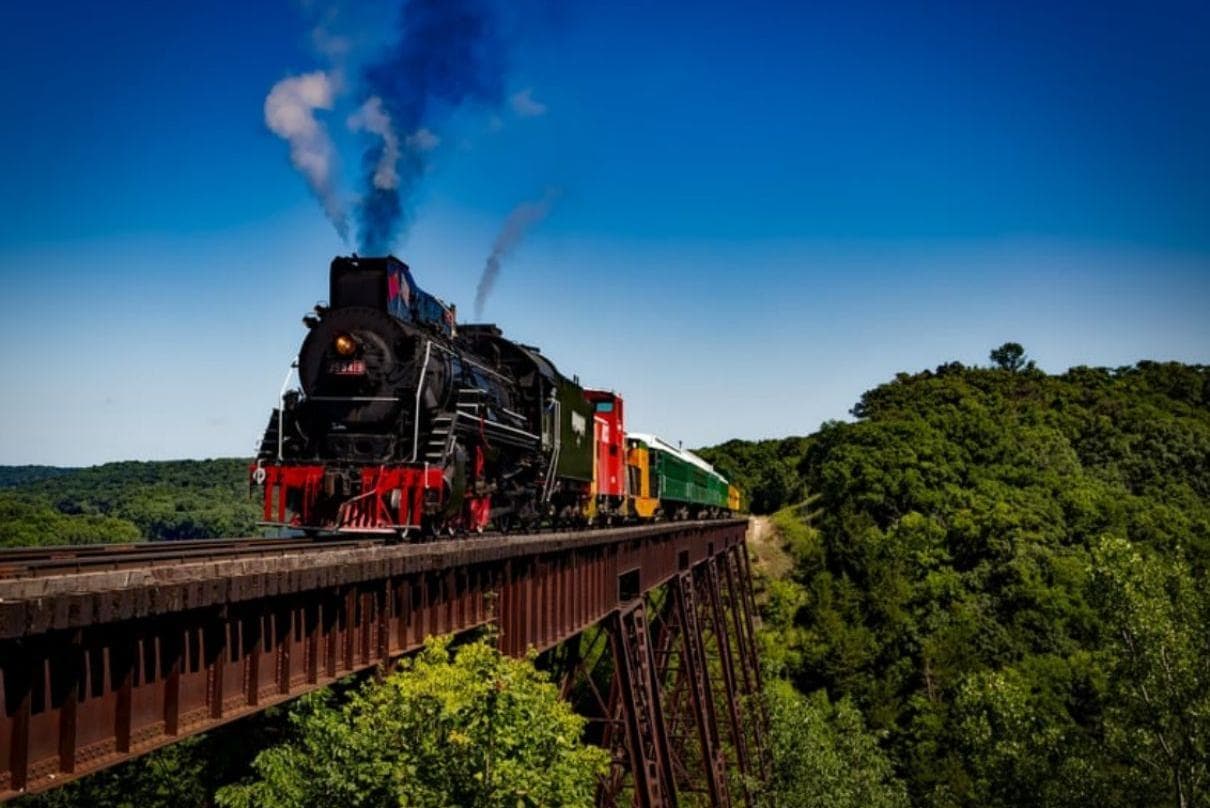