板金加工分野において、表面処理は製品の外観に影響を与えるだけでなく、耐久性、機能性、そして市場競争力にも直接関係しています。産業機器、自動車製造、電子機器など、どのような分野においても、高品質な表面処理プロセスは製品の品質と付加価値を大幅に向上させることができます。以下の10の重要なヒントは、板金表面処理のプロセスフローを最適化し、より効率的に優れた結果を達成するために役立つように設計されています。
ヒント1:正確な前処理
あらゆる表面処理プロセスを開始する前に、徹底した表面前処理を行うことが、その後の処理の効果を確実にするための基礎となります。
表面の油分、酸化物、錆を取り除くことが最初の作業です。専門の脱脂剤や錆取り剤を使用し、浸漬、スプレー、または手拭きで拭き取ってください。
頑固な汚れには、機械による研磨(サンドペーパー、砥石など)が使用できます。
操作時に注意してください:特に薄い板金部品の場合、基板表面の損傷を避けるために力を制御します。
改善提案: 特に大量生産においては、処理の効率と一貫性を確保するために、自動化された前処理装置 (スプレー システムなど) を使用します。
ヒント2:適切なコーティング材を選ぶ
使用シナリオによって、板金部品のコーティング材料に対する要件は異なります。
屋外環境:フッ素コーティングやアクリルコーティングなどの耐候性の高いコーティングの使用をお勧めします。
高摩擦部品: 耐摩耗性を高めるには、ポリウレタンコーティングまたはセラミックコーティングが推奨されます。
同時に、コーティングの密着性にも注意を払う必要があります。密着性はプライマーによって向上させることができます。特殊なニーズ(抗菌性や断熱性など)がある場合は、機能性コーティングを検討することもできます。
ヒント:環境への配慮とVOC(揮発性有機化合物)含有量の低さが市場のトレンドになりつつあり、グリーンで環境に優しいコーティングが好まれるようになっています。
ヒント3:スプレープロセスのパラメータを最適化する
スプレープロセスのパラメータはコーティングの品質と外観を直接決定します。
スプレーガンの距離: 垂れ下がったり粒子が粗くなったりしないように、15〜25 cm の距離を保つ必要があります。
噴霧圧力: 塗料の均一な霧化を確保するために、0.3 ~ 0.6 MPa にすることをお勧めします。
スプレー速度と角度: 複雑な形状のワークピースの場合は、スプレーガンの角度を調整して、エッジと溝に均一なコーティングが塗布されるようにします。
改善の提案:プロセス検証フェーズでサンプルコーティング実験を実施し、パラメータ設定を最適化して大規模生産における安定性を確保します。
ヒント4:静電噴霧技術を使用する
静電噴霧は、その高い接着率と均一性により、現代の表面処理の第一選択肢となっています。
接地効果は噴霧品質の鍵であり、安定した電界を確保するために専門的な接地装置を使用する必要があります。
板金の複雑さに応じて静電電圧を調整します。通常は 50 ~ 80 KV の間で制御されます。
止まり穴や内部空洞のある複雑なワークピースの場合、デュアルガン システムまたは手動補助スプレーを使用して、電界シールド効果によって生じるコーティングの弱い領域を回避することができます。
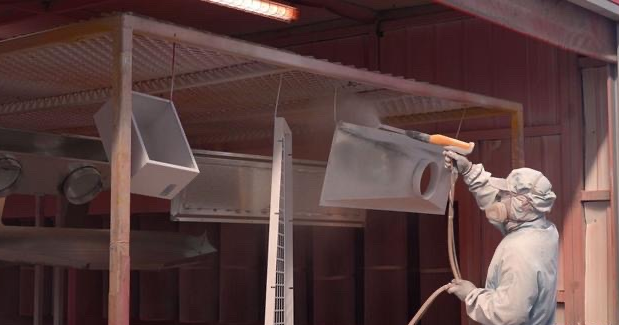
ヒント5:リン酸塩処理は耐腐食性能を高める
リン酸塩処理は、基材の耐食性を向上させるだけでなく、その後のコーティングの密着性も向上させます。
温度管理:鋼材のリン酸塩処理の推奨温度は50~70℃です。温度が高すぎても低すぎても、リン酸塩処理皮膜の均一性に影響を及ぼします。
時間設定: 通常は 3 ~ 10 分ですが、材料とプロセスの要件に応じて調整されます。
アップグレード提案: 低温リン酸塩処理技術を使用してエネルギー消費を削減し、環境に優しいリン酸塩処理溶液と組み合わせて、産業廃水処理の圧力を軽減します。
ヒント6:電気めっきプロセスの核心をマスターする
電気めっきは優れた装飾性と保護性を提供しますが、プロセスの高精度な制御が必要です。
電流密度と温度は厳密に一致させる必要があります。例えば、亜鉛めっきの場合、温度は20~30℃、電流密度は2~4A/dm²に維持する必要があります。
コーティングの滑らかさと密度を確保するために、電気めっき溶液中の添加剤の濃度を定期的に監視する必要があります。
注意:電気めっき後の洗浄は非常に重要です。残留電気めっき液は、コーティング表面に曇りや腐食を引き起こす可能性があります。
ヒント7:陽極酸化処理(アルミニウム部品専用)
陽極酸化処理は、アルミニウム板金部品の耐食性と装飾効果を向上させるための中核プロセスです。
電圧は10〜20Vに制御することが推奨され、処理時間は必要に応じて調整されます(20〜60分)。
酸化後の染色と密封は、抗酸化能力と色の耐久性を高めるための重要なステップです。
先進技術:マイクロアーク酸化(MAO)技術を採用し、酸化膜の硬度と耐摩耗性をさらに向上させます。
ヒント8:精度を向上させるための表面研削と研磨
高品質な表面処理は、研削と研磨と切り離すことはできません。
サンドペーパーの選択: 粗いものから細かいものまで段階的に、たとえば、最初に 320# を使用し、次に 800# 以上のメッシュに移行します。
一貫した操作: 外観に影響を与える横傷を避けるために、研削方向は一貫している必要があります。
高い光沢が求められるワークピースの場合、効果を高めるために研磨ペーストまたは酸化クロムペーストと組み合わせて鏡面研磨を使用できます。
ヒント9:品質検査とプロセス管理を強化する
表面処理品質の安定性は検査と管理と切り離せないものです。
コーティング厚さゲージ:コーティングの厚さを検出します。
接着テスト: クロスカッティングテストやプルオフテストなど、コーティングがしっかりしているかどうかを確認します。
塩水噴霧試験:耐食性を評価します。
改善提案: 自動テスト機器を導入することでテストの効率を確保し、データ分析を組み合わせてリアルタイムのプロセス最適化を実現します。
ヒント10:継続的な学習と技術革新
表面処理技術は日々変化しており、技術的リーダーシップを維持するには以下が必要です。
業界のトレンドに注目する: 展示会やセミナーに参加して、最新のプロセストレンドを把握します。
技術研究開発投資:効率と環境保護レベルを向上させるために、インテリジェントな設備と新しい環境に優しい材料を導入します。
例えば、ナノコーティングやプラズマ噴霧などの新興技術が徐々に推進され、表面処理分野にさらなる可能性をもたらしています。
投稿日時: 2024年12月6日