No campo do procesamento de chapas, o tratamento superficial non só afecta á aparencia do produto, senón que tamén está directamente relacionado coa súa durabilidade, funcionalidade e competitividade do mercado. Tanto se se aplica a equipos industriais, fabricación de automóbiles ou aparellos electrónicos, os procesos de tratamento superficial de alta calidade poden mellorar significativamente a calidade e o valor engadido do produto. Os seguintes 10 consellos clave están deseñados para axudarche a optimizar o fluxo de proceso de tratamento de superficie de chapa e axudar a obter excelentes resultados de forma máis eficiente.
Consello 1: Pretratamento preciso
Antes de que comece calquera proceso de tratamento superficial, o pretratamento superficial completo é a base para garantir o efecto do tratamento posterior.
A eliminación de aceite superficial, óxidos e ferruxe é a primeira tarefa. Podes usar despregadores profesionais ou eliminadores de ferruxe, combinados con empapado, pulverización ou limpeza manual.
Para a contaminación teimosa, pódese usar moenda mecánica (como papel de lixa, roda de moenda, etc.).
Preste atención ao operar:Controla a forza para evitar danar a superficie do substrato, especialmente para pezas de chapa máis finas.
Suxestións de mellora: use equipos de pretratamento automatizado (como os sistemas de spray) para garantir a eficiencia e coherencia do procesamento, especialmente na produción en masa.
Consello 2: elixe o material de revestimento adecuado
Diferentes escenarios de uso teñen diferentes requisitos para os materiais de revestimento das pezas de chapa:
Medio exterior: recoméndase usar un revestimento con alta resistencia ao tempo, como o revestimento de fluorocarbon ou o revestimento acrílico.
Pezas de alta fricción: prefírese o revestimento de poliuretano ou o revestimento cerámico para aumentar a resistencia ao desgaste.
Ao mesmo tempo, tamén se debe prestar atención á adhesión do revestimento, que se pode mellorar por cebador. Para escenarios de demanda especial (como superficies antibacterianas ou illantes), pódense considerar revestimentos funcionais.
Consellos:A amabilidade ambiental e a baixa COV (composto orgánico volátil) dos materiais de revestimento están a converterse nunha tendencia do mercado e pódense preferir revestimentos verdes e ecolóxicos.
Consello 3: optimizar os parámetros do proceso de pulverización
Os parámetros do proceso de pulverización determinan directamente a calidade e o aspecto do revestimento:
Distancia de pistola de pulverización: debe manterse entre 15-25 cm para evitar partículas de caída ou grosas.
Presión de pulverización: recoméndase estar entre 0,3-0,6 MPa para garantir a atomización uniforme da pintura.
Velocidade e ángulo de pulverización: para pezas de traballo con formas complexas, axusta o ángulo da pistola de pulverización para garantir unha cobertura uniforme de revestimento nos bordos e rañuras.
Suxestións de mellora:Realizar experimentos de revestimento de mostras durante a fase de verificación do proceso para optimizar a configuración de parámetros e garantir a estabilidade na produción a gran escala.
Consello 4: usa a tecnoloxía de pulverización electrostática
A pulverización electrostática converteuse na primeira opción para o tratamento superficial moderno debido á súa elevada taxa de adhesión e uniformidade:
O efecto de terra é a clave para a calidade da pulverización, e os equipos de terra profesional deben usarse para asegurar un campo eléctrico estable.
Axuste a tensión electrostática segundo a complexidade da chapa, xeralmente controlada entre 50-80 kV.
Para pezas complexas con buracos cegos ou cavidades interiores, pódese usar un sistema de dobre armario ou unha pulverización manual asistida para evitar zonas débiles do revestimento causado polo efecto de blindaje de campo eléctrico.
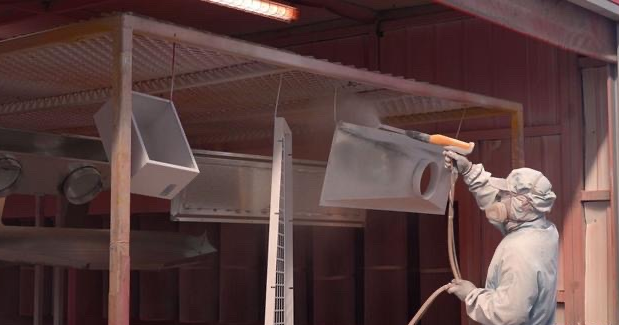
Consello 5: O tratamento fosfatador aumenta o rendemento anticorrosión
O tratamento fosfatador non só pode mellorar a resistencia á corrosión do substrato, senón tamén mellorar a adhesión dos revestimentos posteriores:
Control de temperatura: a temperatura fosfatadora recomendada para o aceiro está entre 50-70 ℃. Demasiado alto ou demasiado baixo afectará á uniformidade da película fosfatadora.
Configuración de tempo: xeralmente 3-10 minutos, axustado segundo os requisitos do material e do proceso.
Suxestión de actualización: use tecnoloxía fosfatadora de baixa temperatura para reducir o consumo de enerxía e combinarse cunha solución fosfatadora ecolóxica para reducir a presión do tratamento de augas residuais industriais.
Consello 6: dominar os puntos fundamentais do proceso de electroplación
A galvanización pode proporcionar excelentes propiedades decorativas e protectoras, pero require un control de alta precisión do proceso:
A densidade e a temperatura de corrente deben ser estrictamente correspondentes. Por exemplo, cando se galvanizan, a temperatura debe estar entre 20-30 ℃ e a densidade actual debe manterse a 2-4 a/dm².
A concentración de aditivos na solución de galvanización debe controlarse regularmente para garantir a suavidade e a densidade do revestimento.
Nota: a limpeza despois da galvanoplada é crucial. A solución de galvanización residual pode causar néboa ou corrosión na superficie do revestimento.
Consello 7: anodizador (exclusivo para pezas de aluminio)
Anodizar é o proceso fundamental para mellorar a resistencia á corrosión e o efecto decorativo das pezas de chapa de aluminio:
Recoméndase a tensión controlada a 10-20 V, e o tempo de procesamento axústase segundo as necesidades (20-60 minutos).
A tinguidura e o selado despois da oxidación son pasos clave para mellorar a capacidade antioxidante e a durabilidade da cor.
Tecnoloxía avanzada: use a tecnoloxía de oxidación de micro-arco (MAO) para mellorar aínda máis a resistencia á dureza e ao desgaste da película de óxido.
Consello 8: moenda e pulido superficial para mellorar a precisión
O tratamento superficial de alta calidade é inseparable da moenda e do pulido:
Selección de papel de lixa: de grosa a fino, paso a paso, por exemplo, primeiro uso 320#, logo transición a 800# ou malla superior.
Funcionamento consistente: a dirección de moenda debe ser consistente para evitar arañazos cruzados que afecten o aspecto.
Para pezas de traballo con altos requirimentos de brillo, pódese usar o pulido de espello, combinado con pasta de pulido ou pasta de óxido de cromo para mellorar o efecto.
Consello 9: Fortalecer a inspección da calidade e o control do proceso
A estabilidade da calidade do tratamento superficial é inseparable da inspección e do control:
Galento de grosor de revestimento: detectar o grosor do revestimento.
Proba de adhesión: como a proba cruzada ou a proba de retirada, para verificar se o revestimento é firme.
Proba de spray de sal: para avaliar a resistencia á corrosión.
Suxestións de mellora: introducindo equipos de proba automatizados, garantir a eficiencia das probas e combinar a análise de datos para a optimización de procesos en tempo real.
Consello 10: aprendizaxe continua e innovación tecnolóxica
A tecnoloxía de tratamento superficial está cambiando con cada día que pasa e para manter o liderado tecnolóxico require:
Preste atención ás tendencias da industria: comprende as últimas tendencias do proceso participando en exposicións e seminarios.
Investimento en I + D de tecnoloxía: introducir equipos intelixentes e novos materiais ecolóxicos para mellorar o nivel de eficiencia e protección ambiental.
Por exemplo, as tecnoloxías emerxentes como os revestimentos de nano e a pulverización de plasma están a ser promovidos gradualmente, proporcionando máis posibilidades para o campo do tratamento superficial.
Tempo de publicación: decembro do 06-2024