Galvanized L bracket Steel Load Switch Mounting Bracket
● Length: 105 mm
● Width: 70 mm
● Height: 85 mm
● Thickness: 4 mm
● Hole length: 18 mm
● Hole width: 9 mm-12 mm
Customization supported
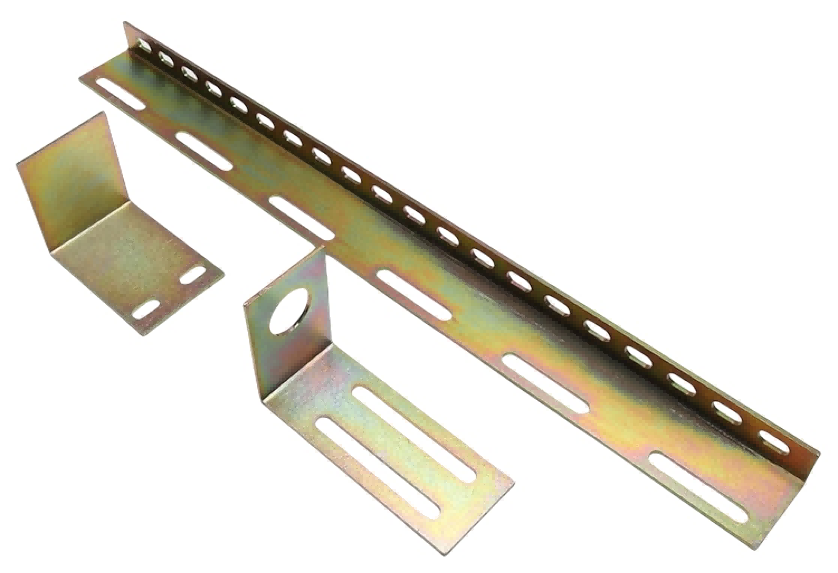
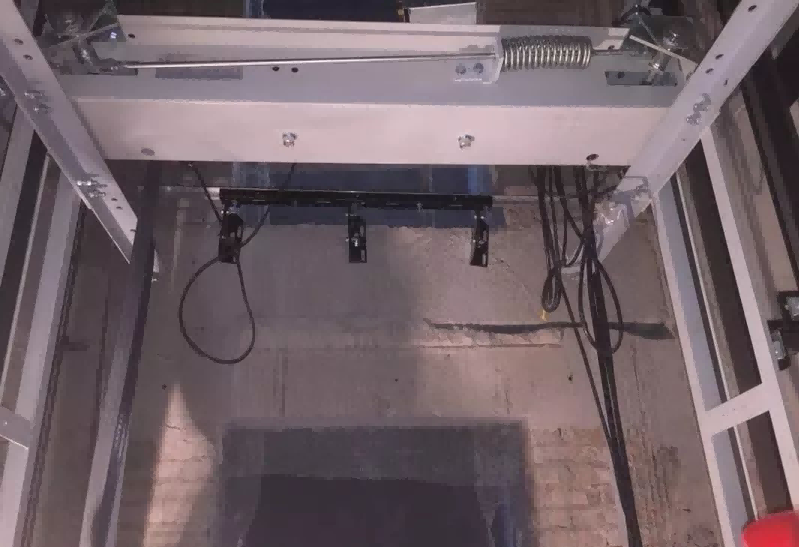
● Product type: elevator accessories
● Material: Q235 steel
● Process: shearing, bending, punching
● Surface treatment: hot-dip galvanizing, electro-galvanizing
● Application: fixing, connecting
● Weight: about 1.95KG
Product Advantages
Sturdy structure: Made of high-strength steel, it has excellent load-bearing capacity and can withstand the weight of elevator doors and the pressure of daily use for a long time.
Precise fit: After precise design, they can perfectly match various elevator door frames, simplify the installation process and reduce commissioning time.
Anti-corrosion treatment: The surface is specially treated after production, which has corrosion and wear resistance, suitable for various environments, and prolongs the service life of the product.
Diverse sizes: Custom sizes can be provided according to different elevator models.
Cost comparison between electrogalvanized bracket and hot-dip galvanized bracket
1. Raw material cost
Electrogalvanized bracket: Electrogalvanizing generally uses cold-rolled sheet as the substrate. The cost of cold-rolled sheet itself is relatively high, and a large amount of chemical materials such as zinc salts are required to configure the electroplating solution during the production process. The cost of these materials should not be underestimated.
Hot-dip galvanized bracket: The substrate for hot-dip galvanizing can be hot-rolled sheet, which is usually cheaper than cold-rolled sheet. Although hot-dip galvanizing consumes a large amount of zinc ingots, due to its relatively low requirements for the substrate, the raw material cost is relatively close to that of electrogalvanized brackets. However, in large-scale production, the raw material cost of hot-dip galvanized brackets may be slightly lower.
2. Equipment and energy costs
Electrogalvanized bracket: Electrogalvanizing requires professional equipment such as electrolysis equipment and rectifiers, and the investment cost of these equipment is relatively high. Moreover, during the electroplating process, electric energy needs to be continuously consumed to maintain the electrolytic reaction. The cost of electric energy accounts for a large proportion of the entire production cost. Especially for large-scale production, the cumulative effect of energy costs is more significant.
Hot-dip galvanized bracket: Hot-dip galvanizing requires pickling equipment, annealing furnaces, and large zinc pots. The investment in annealing furnaces and zinc pots is relatively large. In the production process, the zinc ingots need to be heated to a high temperature of about 450℃-500℃ to melt them for dipping operations. This process consumes a lot of energy, such as natural gas and coal, and the energy cost is also high.
3. Production efficiency and labor costs
Electrogalvanized bracket: The production efficiency of electrogalvanizing is relatively low, especially for some brackets with complex shapes or large sizes, the electroplating time may be longer, thus affecting the production efficiency. In addition, the operation in the electrogalvanizing process is relatively delicate, and the technical requirements for workers are high, and the labor cost will increase accordingly.
Hot-dip galvanized bracket: The production efficiency of hot-dip galvanizing is relatively high. A large number of brackets can be processed in one dip plating, which is suitable for large-scale production. Although the operation and maintenance of hot-dip galvanizing equipment requires certain professionals, the overall labor cost is slightly lower than that of electrogalvanized brackets.
4. Environmental protection cost
Electrogalvanized bracket: The wastewater and waste gas generated by the electrogalvanizing process contain pollutants such as heavy metal ions, which need to undergo strict environmental protection treatment before they can meet the discharge standards. This increases the investment and operation costs of environmental protection equipment, such as the purchase and maintenance costs of wastewater treatment equipment, waste gas purification equipment, etc., as well as the corresponding chemical agent consumption.
Hot-dip galvanized bracket: Some pollutants are also generated during the hot-dip galvanizing process, such as pickling wastewater and zinc smoke, but with the continuous advancement of environmental protection technology, its environmental protection treatment cost is slightly lower than that of electrogalvanized brackets, but a certain amount of funds still need to be invested in the construction and operation of environmental protection facilities.
5. Later maintenance cost
Electrogalvanized bracket: The electrogalvanized layer is relatively thin, generally 3-5 When used in harsh environments such as outdoor, the corrosion resistance is relatively poor, and it is easy to rust and corrode. Regular inspection and maintenance are required, such as re-galvanizing and painting, which increases the cost of later maintenance.
Hot-dip galvanized bracket: The hot-dip galvanized layer is thicker, usually between 18-22 microns, with good corrosion resistance and durability. Under normal use conditions, the service life is long and the later maintenance cost is relatively low.
6. Comprehensive cost
On the whole, under normal circumstances, the cost of hot-dip galvanized brackets will be higher than that of electro-galvanized brackets. According to relevant data, the cost of hot-dip galvanizing is about 2-3 times that of electro-galvanizing. However, the specific cost difference will also be affected by many factors such as market supply and demand, raw material price fluctuations, production scale, processing technology and product quality requirements.
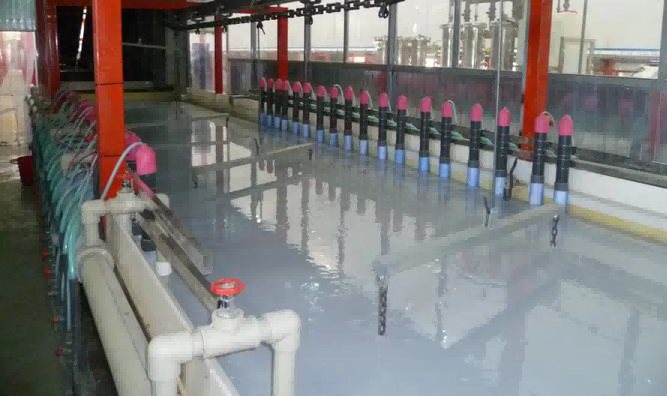
Applicable Elevator Brands
● Otis
● Schindler
● Kone
● TK
● Mitsubishi Electric
● Hitachi
● Fujitec
● Hyundai Elevator
● Toshiba Elevator
● Orona
● Xizi Otis
● HuaSheng Fujitec
● SJEC
● Cibes Lift
● Express Lift
● Kleemann Elevators
● Giromill Elevator
● Sigma
● Kinetek Elevator Group
Quality Management
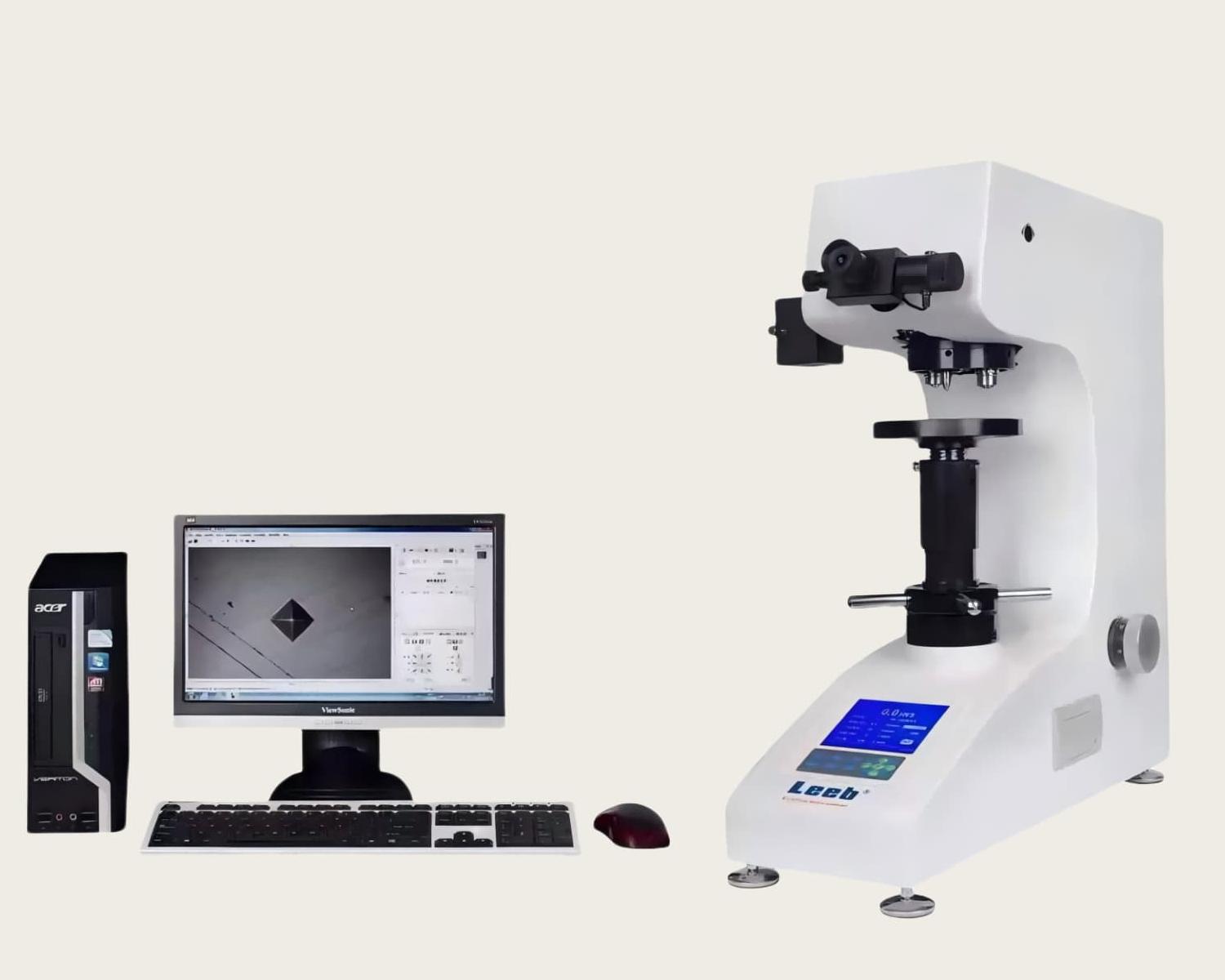
Vickers Hardness Instrument
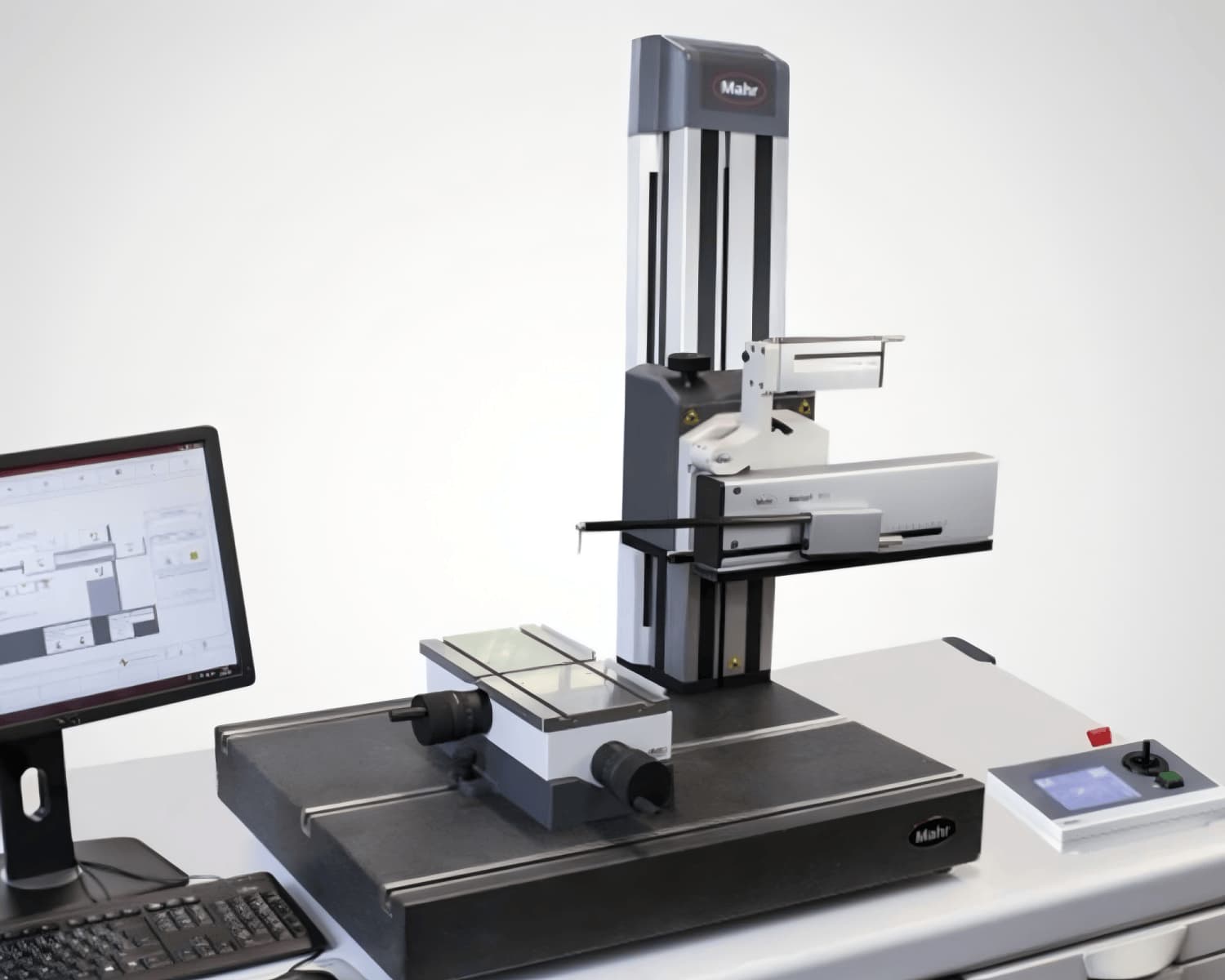
Profile Measuring Instrument
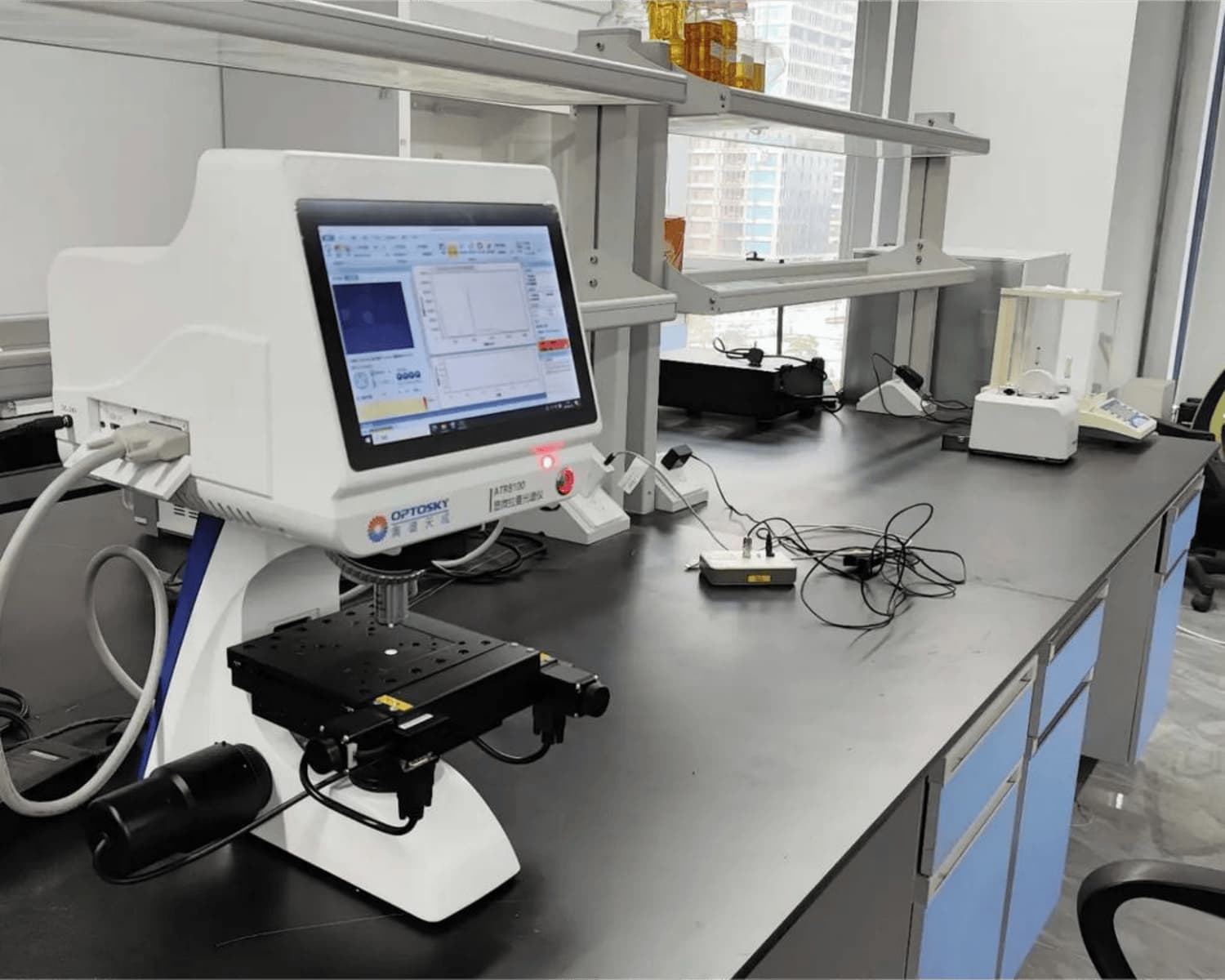
Spectrograph Instrument
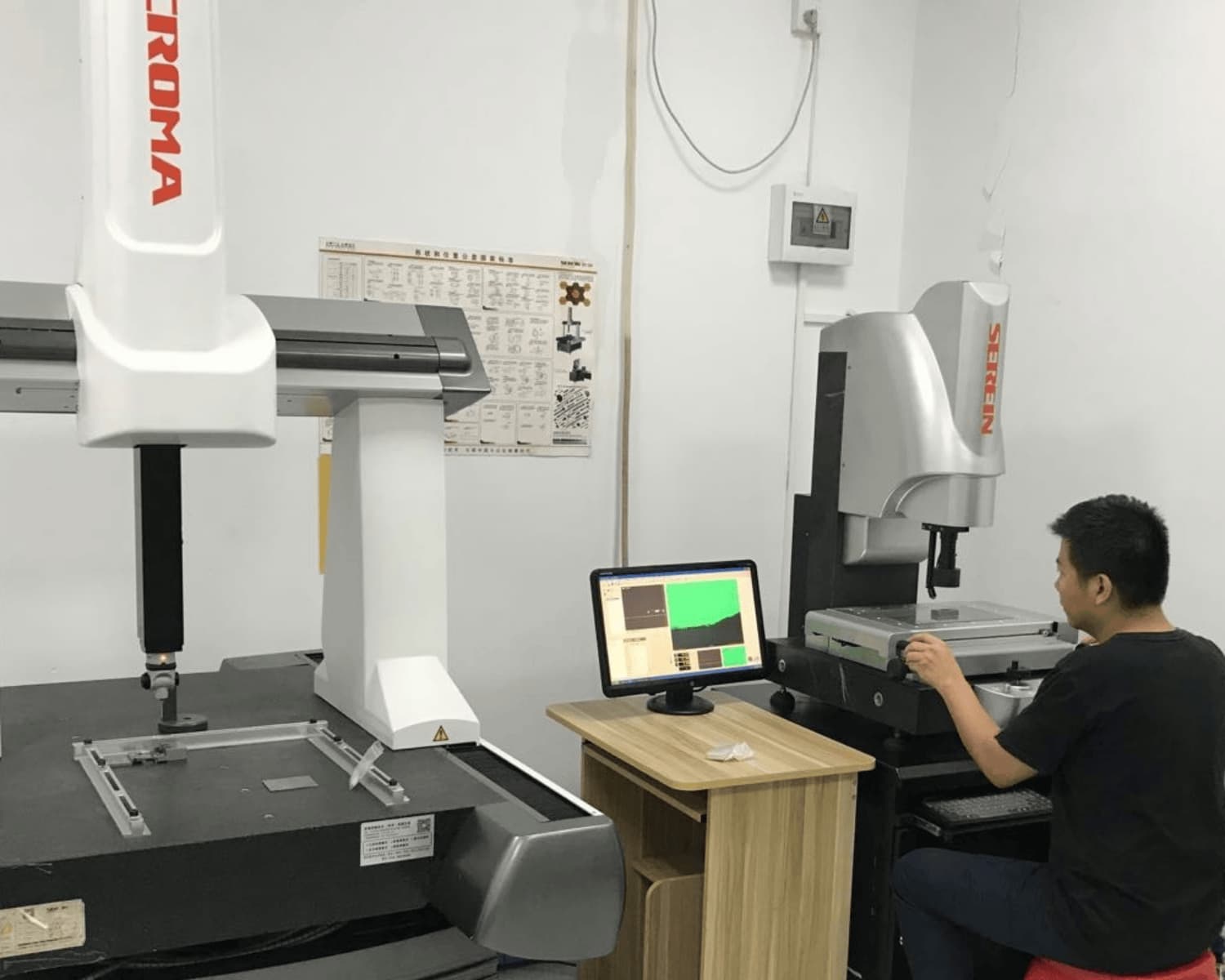
Three Coordinate Instrument
Company Profile
Xinzhe Metal Products Co., Ltd. was established in 2016 and focuses on the production of high-quality metal brackets and components, which are widely used in the construction, elevator, bridge, power, automotive parts and other industries. The main products include seismic pipe gallery brackets, fixed brackets, U-channel brackets, angle brackets, galvanized embedded base plates, elevator mounting brackets and fasteners, etc., which can meet the diverse project needs of various industries.
The company uses cutting-edge laser cutting equipment in conjunction with bending, welding, stamping, surface treatment, and other production processes to guarantee the precision and longevity of the products.
As an ISO 9001 certified company, we have worked closely with many international machinery, elevator and construction equipment manufacturers and provide them with the most competitive customized solutions.
According to the company's "going global" vision, we are dedicated to offering top-notch metal processing services to the global market and are constantly working to improve the quality of our products and services.
Packaging and Delivery
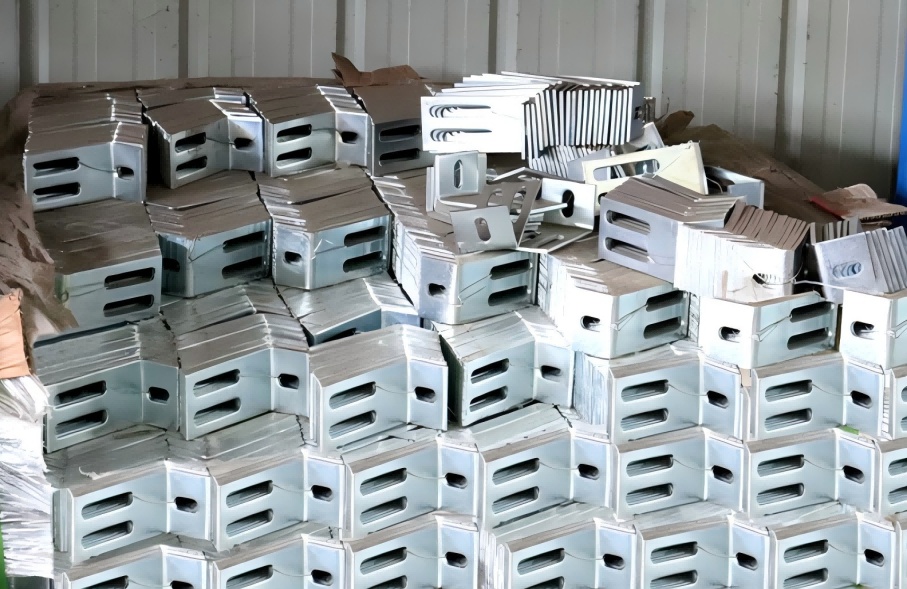
Angle Steel Brackets
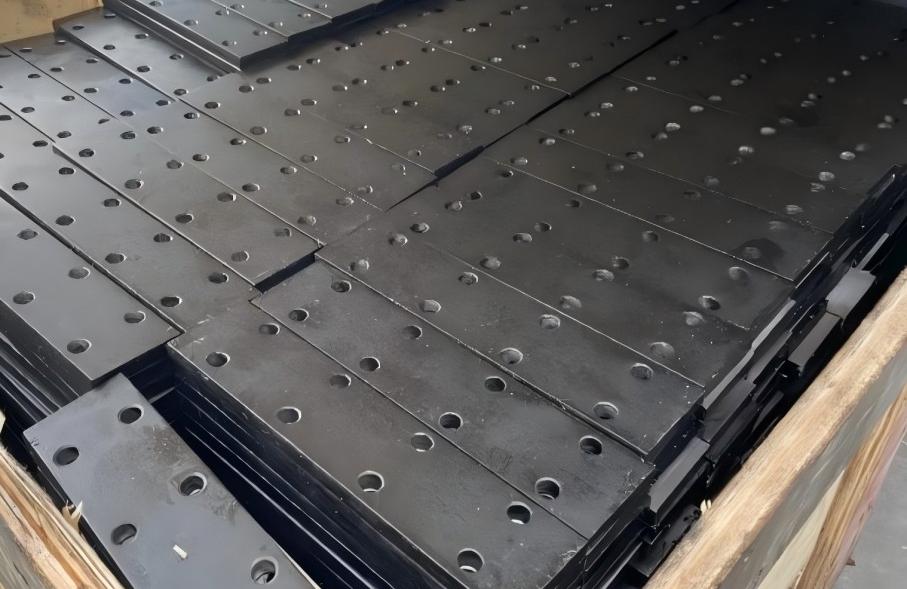
Elevator Guide Rail Connection Plate
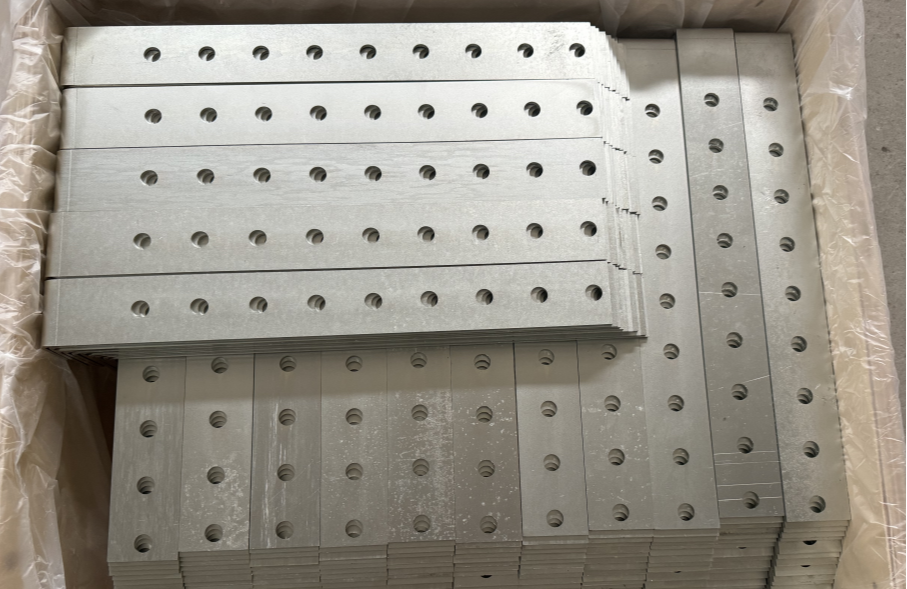
L-shaped Bracket Delivery
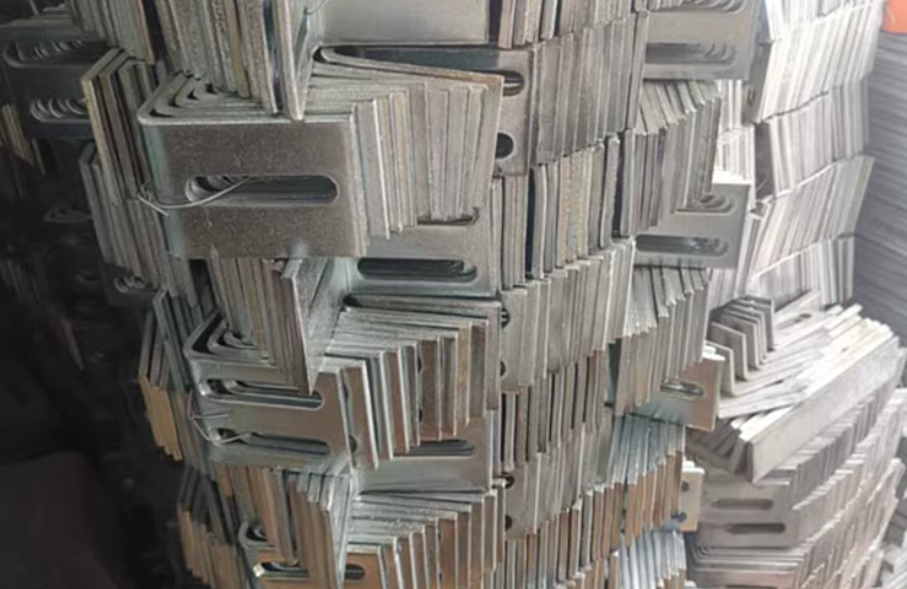
Angle Brackets
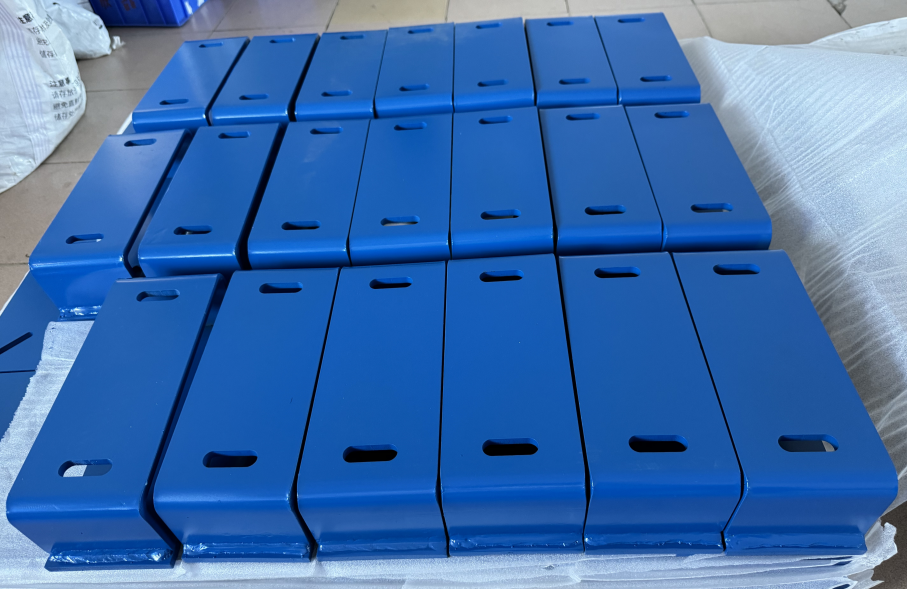
Elevator Mounting Kit
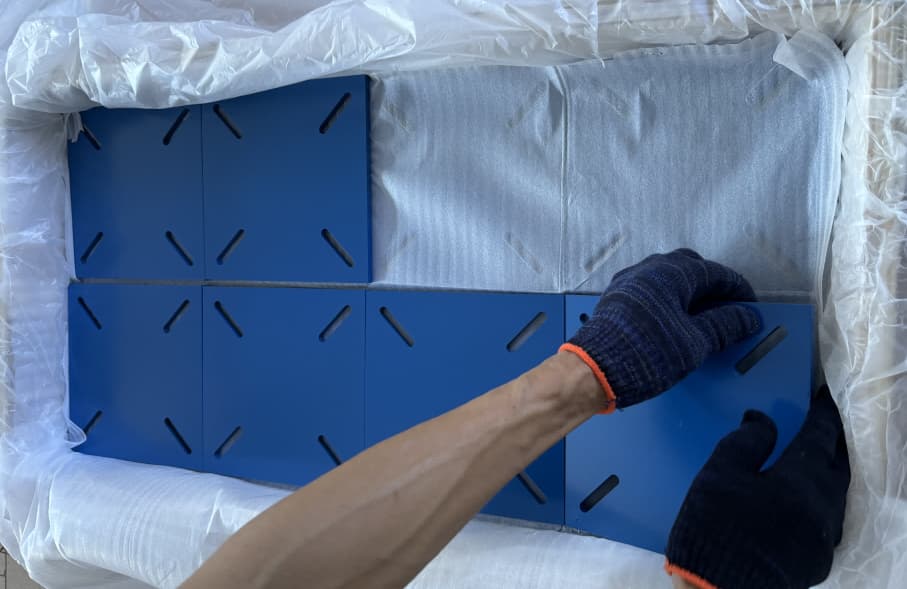
Elevator Accessories Connection Plate
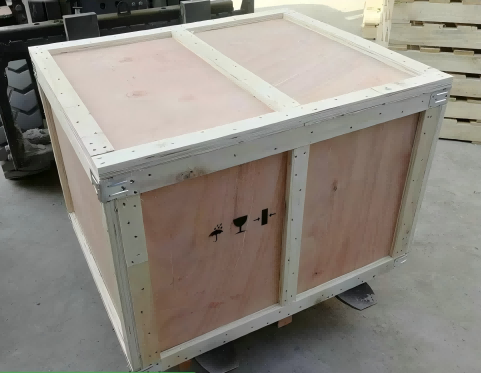
Wooden Box
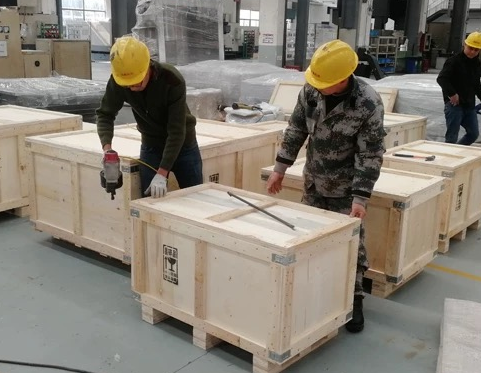
Packing
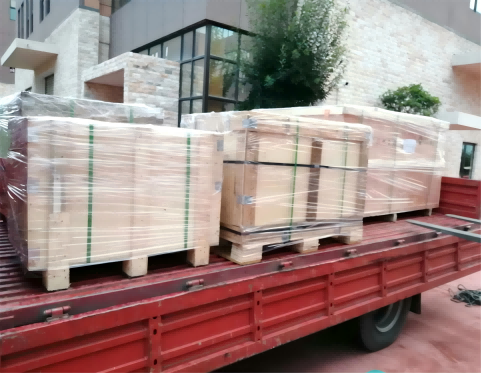
Loading
FAQ
Q: How can I receive a quote?
A: Simply email or WhatsApp us your drawings and necessary supplies, and we'll get back to you with the most affordable quotation as soon as we can.
Q: What is the minimum order quantity that you require?
A: We require a minimum order quantity of 100 pieces for our small products and 10 pieces for our large products.
Q: How long does it take for my order to be delivered after I place it?
A: Samples can be shipped within seven days.
35 to 40 days after payment, mass manufacturing products are produced.
Q: What method do you use to make payments?
A: We take bank accounts, PayPal, Western Union, and TT as forms of payment.
Multiple Transportation Options
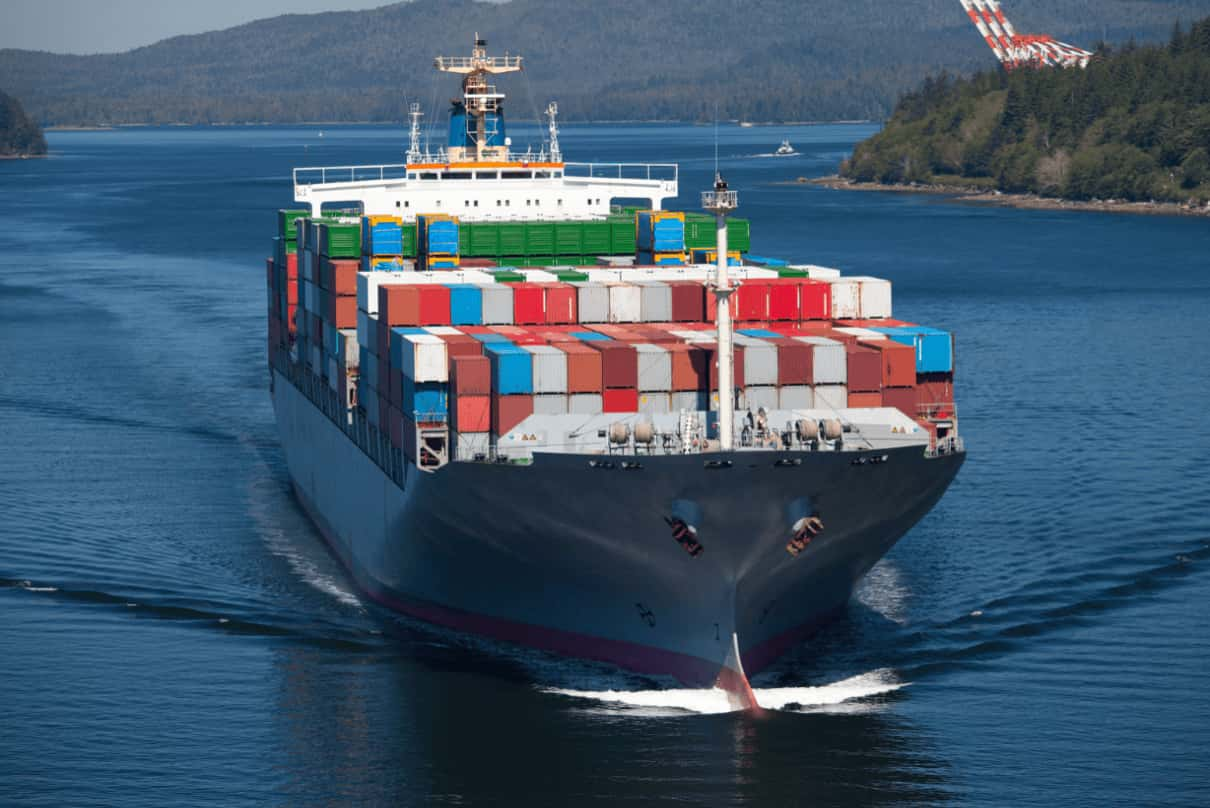
Ocean Freight
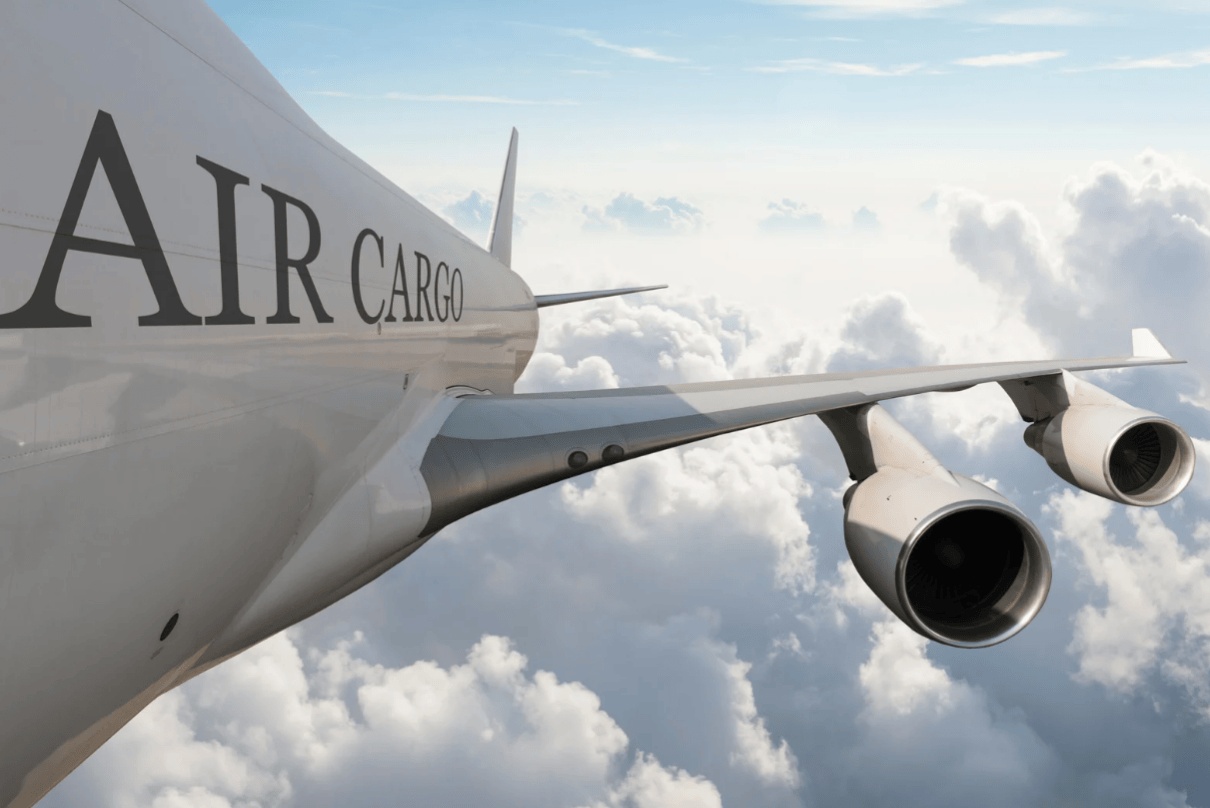
Air Freight
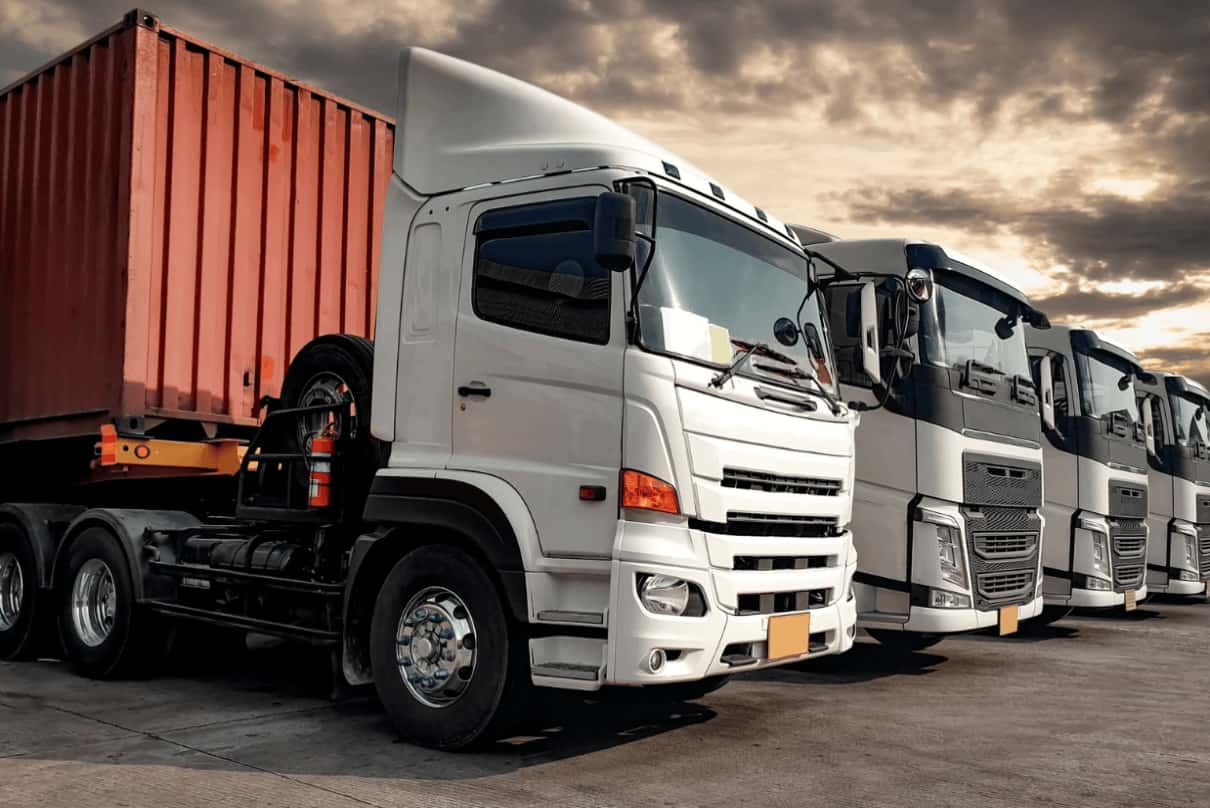
Road Transportation
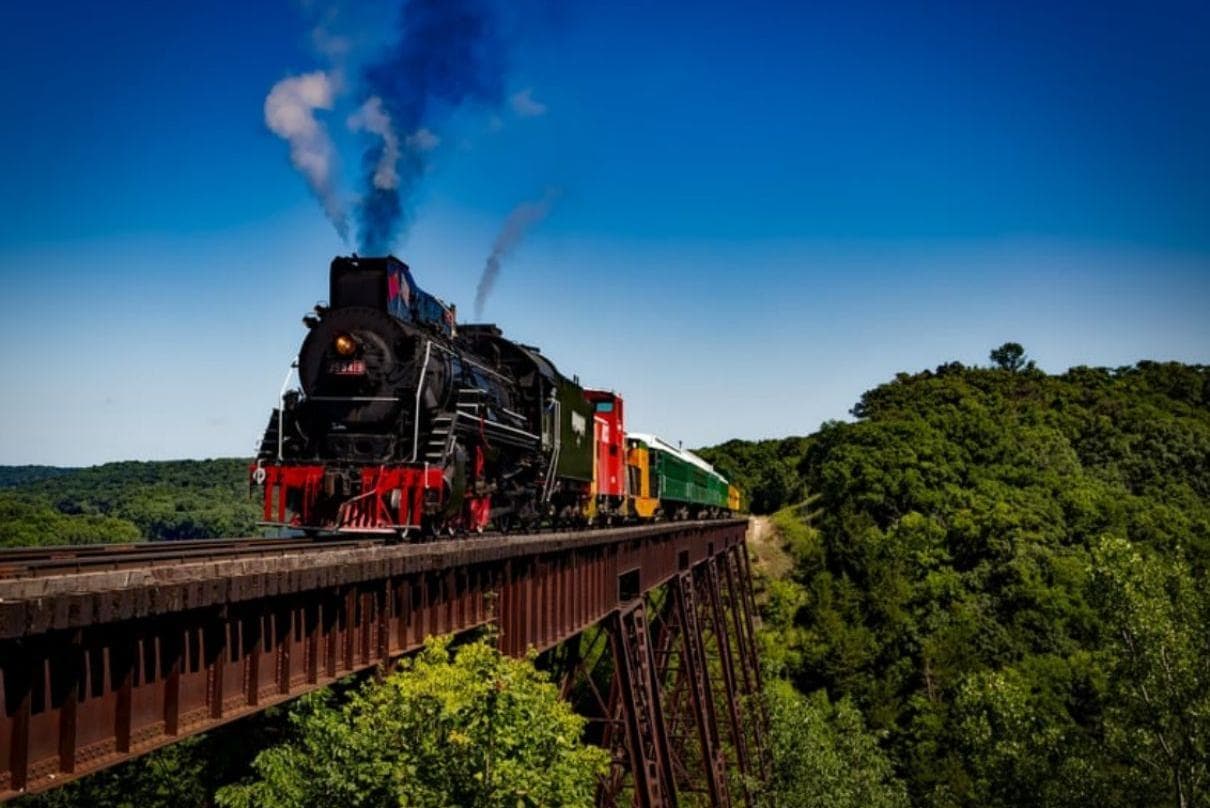