Dans le domaine du traitement de la tôle, le traitement de surface affecte non seulement l'apparence du produit, mais est également directement lié à sa durabilité, sa fonctionnalité et sa compétitivité sur le marché. Qu'il s'agisse d'équipements industriels, de construction automobile ou d'appareils électroniques, des procédés de traitement de surface de haute qualité peuvent améliorer considérablement la qualité et la valeur ajoutée des produits. Les 10 conseils clés suivants vous aideront à optimiser le processus de traitement de surface de la tôle et à obtenir d'excellents résultats plus efficacement.
Astuce 1 : Prétraitement précis
Avant de commencer tout processus de traitement de surface, un prétraitement de surface approfondi est la base pour garantir l'effet du traitement ultérieur.
La première étape consiste à éliminer l'huile, les oxydes et la rouille en surface. Vous pouvez utiliser des dégraissants ou des produits antirouille professionnels, associés à un trempage, une pulvérisation ou un essuyage manuel.
En cas de contamination tenace, un meulage mécanique (comme du papier de verre, une meule, etc.) peut être utilisé.
Faites attention lors de l'utilisation :contrôler la force pour éviter d'endommager la surface du substrat, en particulier pour les pièces en tôle plus minces.
Suggestions d’amélioration : Utiliser des équipements de prétraitement automatisés (tels que des systèmes de pulvérisation) pour garantir l’efficacité et la cohérence du traitement, en particulier dans la production de masse.
Conseil 2 : Choisissez le bon matériau de revêtement
Différents scénarios d'utilisation ont des exigences différentes pour les matériaux de revêtement des pièces en tôle :
Environnement extérieur : Il est recommandé d'utiliser un revêtement à haute résistance aux intempéries, tel qu'un revêtement fluorocarboné ou un revêtement acrylique.
Pièces à friction élevée : un revêtement en polyuréthane ou un revêtement en céramique est préféré pour augmenter la résistance à l'usure.
Parallèlement, il convient de prêter attention à l'adhérence du revêtement, qui peut être améliorée par un apprêt. Pour les applications spécifiques (surfaces antibactériennes ou isolantes, par exemple), des revêtements fonctionnels peuvent être envisagés.
Conseils:Le respect de l'environnement et la faible teneur en COV (composés organiques volatils) des matériaux de revêtement deviennent une tendance du marché, et les revêtements verts et respectueux de l'environnement peuvent être préférés.
Astuce 3 : Optimiser les paramètres du processus de pulvérisation
Les paramètres du processus de pulvérisation déterminent directement la qualité et l'apparence du revêtement :
Distance du pistolet pulvérisateur : Elle doit être maintenue entre 15 et 25 cm pour éviter les affaissements ou les particules grossières.
Pression de pulvérisation : Il est recommandé qu'elle soit comprise entre 0,3 et 0,6 MPa pour assurer une atomisation uniforme de la peinture.
Vitesse et angle de pulvérisation : Pour les pièces aux formes complexes, ajustez l'angle du pistolet de pulvérisation pour assurer une couverture uniforme du revêtement sur les bords et les rainures.
Suggestions d'amélioration :Réalisez des expériences de revêtement d'échantillons pendant la phase de vérification du processus pour optimiser les paramètres et garantir la stabilité de la production à grande échelle.
Astuce 4 : Utilisez la technologie de pulvérisation électrostatique
La pulvérisation électrostatique est devenue le premier choix pour le traitement de surface moderne en raison de son taux d'adhérence élevé et de son uniformité :
L'effet de mise à la terre est la clé de la qualité de la pulvérisation, et un équipement de mise à la terre professionnel doit être utilisé pour garantir un champ électrique stable.
Ajustez la tension électrostatique en fonction de la complexité de la tôle, généralement contrôlée entre 50 et 80 KV.
Pour les pièces complexes avec des trous borgnes ou des cavités intérieures, un système à double pistolet ou une pulvérisation assistée manuellement peut être utilisé pour éviter les zones faibles du revêtement causées par l'effet de blindage du champ électrique.
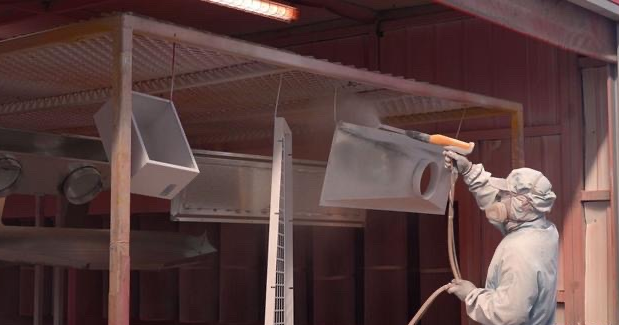
Astuce 5 : Le traitement de phosphatation améliore les performances anticorrosion
Le traitement de phosphatation peut non seulement améliorer la résistance à la corrosion du substrat, mais également renforcer l'adhérence des revêtements ultérieurs :
Contrôle de la température : La température de phosphatation recommandée pour l'acier est comprise entre 50 et 70 °C. Une température trop élevée ou trop basse affectera l'uniformité du film de phosphatation.
Réglage du temps : généralement 3 à 10 minutes, ajusté en fonction des exigences du matériau et du processus.
Suggestion de mise à niveau : utilisez la technologie de phosphatation à basse température pour réduire la consommation d'énergie et combinez-la avec une solution de phosphatation respectueuse de l'environnement pour réduire la pression du traitement des eaux usées industrielles.
Astuce 6 : Maîtrisez les points essentiels du processus de galvanoplastie
La galvanoplastie peut offrir d’excellentes propriétés décoratives et protectrices, mais elle nécessite un contrôle de haute précision du processus :
La densité de courant et la température doivent être rigoureusement adaptées. Par exemple, pour la galvanisation, la température doit être comprise entre 20 et 30 °C et la densité de courant doit être maintenue entre 2 et 4 A/dm².
La concentration d'additifs dans la solution de galvanoplastie doit être surveillée régulièrement pour garantir la douceur et la densité du revêtement.
Remarque : Le nettoyage après galvanoplastie est essentiel. Les résidus de solution de galvanoplastie peuvent provoquer de la buée ou de la corrosion à la surface du revêtement.
Astuce 7 : Anodisation (exclusive pour les pièces en aluminium)
L'anodisation est le processus de base pour améliorer la résistance à la corrosion et l'effet décoratif des pièces en tôle d'aluminium :
Il est recommandé de contrôler la tension à 10-20 V et d'ajuster le temps de traitement en fonction des besoins (20-60 minutes).
La teinture et le scellement après oxydation sont des étapes clés pour améliorer la capacité antioxydante et la durabilité de la couleur.
Technologie de pointe : utilisez la technologie d'oxydation par micro-arc (MAO) pour améliorer encore la dureté et la résistance à l'usure du film d'oxyde.
Astuce 8 : Meulage et polissage de surface pour améliorer la précision
Le traitement de surface de haute qualité est indissociable du meulage et du polissage :
Sélection du papier de verre : du grossier au fin, étape par étape, par exemple, utilisez d'abord du 320#, puis passez à un maillage de 800# ou plus.
Fonctionnement cohérent : Le sens de meulage doit être cohérent pour éviter que les rayures croisées n'affectent l'apparence.
Pour les pièces nécessitant une brillance élevée, le polissage miroir peut être utilisé, combiné avec une pâte à polir ou une pâte à l'oxyde de chrome pour améliorer l'effet.
Conseil 9 : Renforcez l'inspection qualité et le contrôle des processus
La stabilité de la qualité du traitement de surface est indissociable de l'inspection et du contrôle :
Jauge d'épaisseur de revêtement : détecte l'épaisseur du revêtement.
Test d'adhérence : tel que le test de coupe transversale ou d'arrachement, pour vérifier si le revêtement est ferme.
Test au brouillard salin : pour évaluer la résistance à la corrosion.
Suggestions d'amélioration : en introduisant des équipements de test automatisés, garantir l'efficacité des tests et combiner l'analyse des données pour une optimisation des processus en temps réel.
Astuce 10 : Apprentissage continu et innovation technologique
La technologie de traitement de surface évolue de jour en jour et pour maintenir son leadership technologique, il faut :
Soyez attentif aux tendances du secteur : saisissez les dernières tendances en matière de processus en participant à des expositions et à des séminaires.
Investissement en R&D technologique : introduire des équipements intelligents et de nouveaux matériaux respectueux de l'environnement pour améliorer l'efficacité et le niveau de protection de l'environnement.
Par exemple, les technologies émergentes telles que les nano-revêtements et la pulvérisation plasma sont progressivement promues, offrant davantage de possibilités dans le domaine du traitement de surface.
Date de publication : 06/12/2024