Auf dem Gebiet der Blechverarbeitung beeinflusst die Oberflächenbehandlung nicht nur das Erscheinungsbild des Produkts, sondern hängt auch in direktem Zusammenhang mit seiner Haltbarkeit, Funktionalität und Marktwettbewerbsfähigkeit zusammen. Unabhängig davon, ob es sich um industrielle Geräte, Automobilherstellung oder elektronische Geräte angewendet wird, können hochwertige Oberflächenbehandlungsprozesse die Produktqualität und den Mehrwert erheblich verbessern. Die folgenden 10 wichtigsten Tipps sind so konzipiert, dass Sie den Prozessfluss der Blechoberflächenbehandlung optimieren und hervorragende Ergebnisse effizienter erzielen.
Tipp 1: Genauige Vorbehandlung
Bevor ein Oberflächenbehandlungsprozess beginnt, ist eine gründliche Vorbehandlung der Oberflächen die Grundlage für die Gewährleistung der Wirkung der anschließenden Behandlung.
Das Entfernen von Oberflächenöl, Oxiden und Rost ist die erste Aufgabe. Sie können professionelle Entfetter oder Rostentferner verwenden, kombiniert mit Einweichen, Sprühen oder manuellem Wisching.
Für hartnäckige Kontaminationen können mechanisches Schleifen (wie Sandpapier, Schleifrad usw.) verwendet werden.
Achten Sie beim Betrieb:Kontrollieren Sie die Kraft, um zu vermeiden, dass die Substratoberfläche insbesondere für dünnere Blechenteile beschädigt wird.
Verbesserungsvorschläge: Verwenden Sie automatisierte Vorbehandlungsgeräte (wie Sprühsysteme), um die Verarbeitungseffizienz und -konsistenz, insbesondere bei der Massenproduktion, sicherzustellen.
Tipp 2: Wählen Sie das richtige Beschichtungsmaterial
Unterschiedliche Nutzungsszenarien haben unterschiedliche Anforderungen für die Beschichtungsmaterialien von Blechteilen:
Outdoor -Umgebung: Es wird empfohlen, eine Beschichtung mit hoher Wetterresistenz wie Fluorkohlenstoffbeschichtung oder Acrylbeschichtung zu verwenden.
Teile mit hoher Reibung: Polyurethanbeschichtung oder Keramikbeschichtung wird bevorzugt, um die Verschleißfestigkeit zu erhöhen.
Gleichzeitig sollte auch der Haftung der Beschichtung beachtet werden, die durch Primer verbessert werden kann. Für Szenarien für besondere Nachfrage (wie antibakterielle oder isolierende Oberflächen) können Funktionsbeschichtungen berücksichtigt werden.
Tipps:Der Umweltfreundlichkeit und der niedrige VOC -Gehalt (flüchtiger organischer Verbindungen) von Beschichtungsmaterialien werden zu einem Markttrend, und umweltfreundliche und umweltfreundliche Beschichtungen können bevorzugt werden.
Tipp 3: Sprühprozessparameter optimieren
Sprühprozessparameter bestimmen direkt die Qualität und das Aussehen der Beschichtung:
Sprühpistolenentfernung: Es sollte zwischen 15 und 25 cm gehalten werden, um schlaffe oder grobe Partikel zu vermeiden.
Sprühdruck: Es wird empfohlen, zwischen 0,3 und 0,6 MPa zu liegen, um eine gleichmäßige Zerstörung der Farbe zu gewährleisten.
Sprühgeschwindigkeit und Winkel: Passen Sie für Werkstücke mit komplexen Formen den Winkel der Sprühpistole ein, um eine gleichmäßige Beschichtungsabdeckung an den Kanten und Rillen zu gewährleisten.
Verbesserungsvorschläge:Führen Sie Probenbeschichtungsexperimente während der Prozessverifizierungsphase durch, um die Parametereinstellungen zu optimieren und die Stabilität der großflächigen Produktion zu gewährleisten.
Tipp 4: Verwenden Sie die elektrostatische Sprühtechnologie
Das elektrostatische Sprühen ist aufgrund ihrer hohen Adhäsionsrate und Gleichmäßigkeit die erste Wahl für die moderne Oberflächenbehandlung geworden:
Der Erdungseffekt ist der Schlüssel zur Qualität des Sprühens, und professionelle Erdungsausrüstung sollte verwendet werden, um ein stabiles elektrisches Feld zu gewährleisten.
Stellen Sie die elektrostatische Spannung nach der Komplexität des Blechs ein, der im Allgemeinen zwischen 50 und 80 kV gesteuert wird.
Für komplexe Werkstücke mit blinden Löchern oder inneren Hohlräumen kann ein Dual-Gun-System oder ein manuell unterstütztes Sprühen verwendet werden, um schwache Bereiche der Beschichtung zu vermeiden, die durch den Effekt der elektrischen Feldabschaltung verursacht wird.
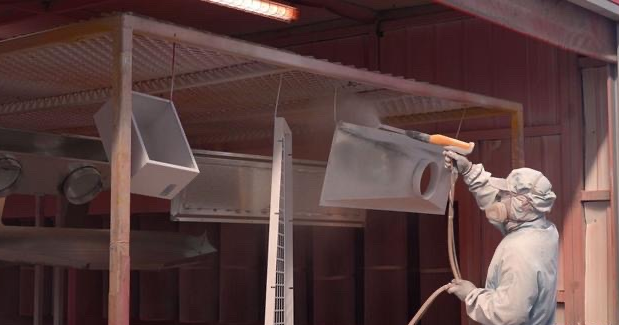
Tipp 5: Die Phosphatebehandlung verbessert die Anti-Korrosionsleistung
Die Phosphatebehandlung kann nicht nur die Korrosionsresistenz des Substrats verbessern, sondern auch die Adhäsion der nachfolgenden Beschichtungen verbessern:
Temperaturregelung: Die empfohlene Phosphattemperatur für Stahl liegt zwischen 50 und 70 ℃. Zu hoch oder zu niedrig wirkt sich die Gleichmäßigkeit des Phosphatfilms aus.
Zeiteinstellung: Im Allgemeinen 3-10 Minuten, eingestellt nach Material- und Prozessanforderungen.
Upgrade-Vorschlag: Verwenden Sie die Phosphattechnologie mit niedriger Temperatur, um den Energieverbrauch zu verringern, und kombinieren Sie sie mit umweltfreundlicher Phosphatelösung, um den Druck der industriellen Abwasserbehandlung zu verringern.
Tipp 6: Beherrschen Sie die Kernpunkte des Elektroplattenprozesses
Die Elektroplatte kann hervorragende dekorative und schützende Eigenschaften liefern, erfordert jedoch eine hohe Präzisionskontrolle des Prozesses:
Die Stromdichte und Temperatur müssen streng übereinstimmen. Zum Beispiel sollte die Temperatur bei der Galvanisierung zwischen 20 und 30 ° C liegen und die Stromdichte bei 2-4 A/DM² beibehalten werden.
Die Konzentration von Zusatzstoffe in der Elektroplattenlösung sollte regelmäßig überwacht werden, um die Glätte und Dichte der Beschichtung zu gewährleisten.
HINWEIS: Die Reinigung nach der Elektroplation ist entscheidend. Die verbleibende Elektroplattenlösung kann auf der Oberfläche der Beschichtung zu Fogging oder Korrosion führen.
Tipp 7: Anodisierung (exklusiv für Aluminiumteile)
Anodisierung ist der Kernprozess zur Verbesserung der Korrosionsbeständigkeit und der dekorativen Wirkung von Aluminiumblech -Teilen:
Es wird empfohlen, die Spannung bei 10-20 V zu steuern, und die Verarbeitungszeit wird entsprechend den Anforderungen (20-60 Minuten) angepasst.
Färben und Versiegelung nach Oxidation sind wichtige Schritte zur Verbesserung der Antioxidationskapazität und der Farbdauer.
Fortgeschrittene Technologie: Verwenden Sie die MIO-Technologie (Micro-ARC Oxidation), um die Härte und den Verschleiß Widerstand des Oxidfilms weiter zu verbessern.
Tipp 8: Oberflächenschleife und Polieren, um die Präzision zu verbessern
Eine hochwertige Oberflächenbehandlung ist untrennbar mit dem Schleifen und Polieren untrennbar miteinander verbunden:
Schleifpapierauswahl: Verwenden Sie beispielsweise zuerst 320# von grob bis fein, und wechseln Sie zuerst auf 800# oder höher.
Konsistenten Betrieb: Die Schleifrichtung muss konsistent sein, um Kreuzkratzer zu vermeiden, die das Erscheinungsbild beeinflussen.
Für Werkstücke mit hohen Glanzanforderungen kann das Spiegelpolieren verwendet werden, kombiniert mit Polierpaste oder Chromoxidpaste, um den Effekt zu verbessern.
Tipp 9: Stärken der Qualitätsinspektion und der Prozesskontrolle
Die Stabilität der Oberflächenbehandlungsqualität ist untrennbar mit Inspektion und Kontrolle verbunden:
Beschichtungsdicke: Erfassen Sie die Beschichtungsdicke.
Adhäsionstest: Um zu überprüfen, ob die Beschichtung fest ist.
Salzspray -Test: Bewertung der Korrosionsbeständigkeit.
Verbesserungsvorschläge: Durch Einführung automatisierter Testgeräte stellen Sie die Effizienz des Tests sicher und kombinieren Sie die Datenanalyse für die Echtzeitprozessoptimierung.
Tipp 10: kontinuierliches Lernen und technologische Innovation
Die Oberflächenbehandlungstechnologie verändert sich mit jedem Tag und die technologische Führung erfordert:
Achten Sie auf Branchentrends: Fassen Sie die neuesten Prozesstrends durch die Teilnahme an Ausstellungen und Seminaren.
Technologie F & E -Investition: Intelligente Geräte und neue umweltfreundliche Materialien einführen, um die Effizienz und den Umweltschutz zu verbessern.
Zum Beispiel werden aufstrebende Technologien wie Nanobeschichtungen und Plasmasprühen allmählich gefördert und bieten mehr Möglichkeiten für das Feld der Oberflächenbehandlung.
Postzeit: Dezember 06-2024