В областта на обработката на ламарина повърхностната обработка не само влияе върху външния вид на продукта, но е пряко свързана и с неговата издръжливост, функционалност и конкурентоспособност на пазара. Независимо дали се прилага за индустриално оборудване, производство на автомобили или електронни уреди, висококачествените процеси на повърхностна обработка могат значително да подобрят качеството на продукта и добавената стойност. Следващите 10 ключови съвета са създадени, за да ви помогнат да оптимизирате процеса на обработка на повърхността на ламарина и да помогнете за постигането на отлични резултати по-ефективно.
Съвет 1: Прецизна предварителна обработка
Преди да започне какъвто и да е процес на повърхностна обработка, задълбочената предварителна обработка на повърхността е основата за осигуряване на ефекта от последващата обработка.
Отстраняването на повърхностно масло, оксиди и ръжда е първата задача. Можете да използвате професионални обезмаслители или препарати за отстраняване на ръжда, комбинирани с накисване, пръскане или ръчно забърсване.
За упорити замърсявания може да се използва механично шлайфане (като шкурка, шлифовъчно колело и др.).
Обърнете внимание при работа:контролирайте силата, за да избегнете повреда на повърхността на субстрата, особено за по-тънки метални части.
Предложения за подобрение: Използвайте автоматизирано оборудване за предварителна обработка (като системи за пръскане), за да осигурите ефективност и последователност на обработката, особено при масово производство.
Съвет 2: Изберете правилния материал за покритие
Различните сценарии на употреба имат различни изисквания за материалите за покритие на детайлите от ламарина:
Външна среда: Препоръчително е да използвате покритие с висока устойчивост на атмосферни влияния, като флуоровъглеродно покритие или акрилно покритие.
Части с високо триене: Предпочита се полиуретаново или керамично покритие за увеличаване на устойчивостта на износване.
В същото време трябва да се обърне внимание и на адхезията на покритието, която може да се подобри с грунд. За сценарии със специално търсене (като антибактериални или изолиращи повърхности) могат да се обмислят функционални покрития.
Съвети:Екологичността и ниското съдържание на VOC (летливи органични съединения) в покривните материали се превръщат в пазарна тенденция и могат да се предпочитат зелени и екологично чисти покрития.
Съвет 3: Оптимизирайте параметрите на процеса на пръскане
Параметрите на процеса на пръскане директно определят качеството и външния вид на покритието:
Разстояние от пистолета за пръскане: Трябва да се поддържа между 15-25 см, за да се избегне увисване или груби частици.
Налягане при пръскане: Препоръчително е да бъде между 0,3-0,6 MPa, за да се осигури равномерно разпръскване на боята.
Скорост и ъгъл на пръскане: За детайли със сложни форми, регулирайте ъгъла на пистолета за пръскане, за да осигурите равномерно покритие на ръбовете и жлебовете.
Предложения за подобрение:Провеждайте експерименти с пробно покритие по време на фазата на проверка на процеса, за да оптимизирате настройките на параметрите и да осигурите стабилност при широкомащабно производство.
Съвет 4: Използвайте технология за електростатично пръскане
Електростатичното пръскане се превърна в първия избор за съвременна повърхностна обработка поради високата степен на адхезия и еднородност:
Ефектът на заземяване е ключът към качеството на пръскането и трябва да се използва професионално оборудване за заземяване, за да се осигури стабилно електрическо поле.
Регулирайте електростатичното напрежение според сложността на металния лист, като обикновено се контролира между 50-80 KV.
За сложни детайли със слепи отвори или вътрешни кухини може да се използва система с двоен пистолет или ръчно подпомагано пръскане, за да се избегнат слаби зони на покритието, причинени от ефекта на екраниране на електрическото поле.
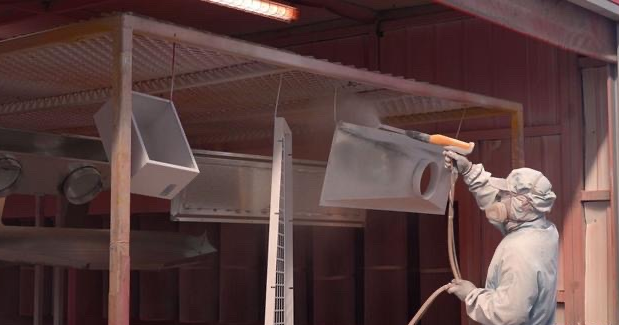
Съвет 5: Фосфатирането подобрява антикорозионните характеристики
Третирането с фосфатиране може не само да подобри корозионната устойчивост на основата, но и да подобри адхезията на следващите покрития:
Контрол на температурата: Препоръчителната температура на фосфатиране за стомана е между 50-70 ℃. Твърде високо или твърде ниско ще повлияе на еднородността на фосфатиращия филм.
Настройка на времето: Обикновено 3-10 минути, коригирани според изискванията на материала и процеса.
Предложение за надграждане: Използвайте технология за нискотемпературно фосфатиране, за да намалите потреблението на енергия и комбинирайте с екологичен разтвор за фосфатиране, за да намалите налягането при пречистване на промишлени отпадъчни води.
Съвет 6: Овладейте основните точки на процеса на галванопластика
Галванопластиката може да осигури отлични декоративни и защитни свойства, но изисква високо прецизен контрол на процеса:
Плътността на тока и температурата трябва да бъдат строго съгласувани. Например при поцинковане температурата трябва да бъде между 20-30 ℃ и плътността на тока трябва да се поддържа на 2-4 A/dm².
Концентрацията на добавките в разтвора за галванопластика трябва да се следи редовно, за да се гарантира гладкостта и плътността на покритието.
Забележка: Почистването след галванопластика е от решаващо значение. Остатъчният галваничен разтвор може да причини замъгляване или корозия на повърхността на покритието.
Съвет 7: Анодиране (изключително за алуминиеви части)
Анодирането е основният процес за подобряване на устойчивостта на корозия и декоративния ефект на частите от алуминиев лист:
Напрежението се препоръчва да се контролира на 10-20 V, а времето за обработка се регулира според нуждите (20-60 минути).
Боядисването и запечатването след оксидиране са ключови стъпки за подобряване на антиоксидантния капацитет и устойчивостта на цвета.
Усъвършенствана технология: Използвайте технология за микродъгово оксидиране (MAO), за да подобрите допълнително твърдостта и устойчивостта на износване на оксидния филм.
Съвет 8: Повърхностно шлайфане и полиране за подобряване на прецизността
Висококачествената повърхностна обработка е неделима от шлайфането и полирането:
Избор на шкурка: От груба към фина, стъпка по стъпка, например, първо използвайте 320#, след това преминете към 800# или по-висока мрежа.
Постоянна работа: Посоката на смилане трябва да е постоянна, за да се избегнат кръстосани драскотини, които влияят на външния вид.
За детайли с високи изисквания за гланц може да се използва огледално полиране, комбинирано с полираща паста или паста от хромен оксид за подобряване на ефекта.
Съвет 9: Засилете проверката на качеството и контрола на процеса
Стабилността на качеството на повърхностната обработка е неделима от проверката и контрола:
Уред за измерване на дебелината на покритието: открива дебелината на покритието.
Тест за адхезия: като напречен разрез или тест за издърпване, за да се провери дали покритието е здраво.
Тест със солен спрей: за оценка на устойчивостта на корозия.
Предложения за подобрение: чрез въвеждане на автоматизирано оборудване за тестване, осигурете ефективността на тестването и комбинирайте анализ на данни за оптимизиране на процеса в реално време.
Съвет 10: Непрекъснато учене и технологични иновации
Технологията за повърхностна обработка се променя с всеки изминал ден и за поддържане на технологично лидерство са необходими:
Обърнете внимание на тенденциите в индустрията: разберете най-новите тенденции в процесите, като участвате в изложения и семинари.
Инвестиции в научноизследователска и развойна дейност в областта на технологиите: въвеждане на интелигентно оборудване и нови екологично чисти материали за подобряване на ефективността и нивото на защита на околната среда.
Например нововъзникващите технологии като нано покрития и плазмено пръскане постепенно се насърчават, предоставяйки повече възможности за областта на повърхностната обработка.
Време на публикуване: 6 декември 2024 г